Head of Department Qa
10+ Head of Department Qa Interview Questions and Answers
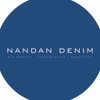
Asked in Nandan Denim

Q. What is Six Sigma and how can it be applied at the plant level?
Six Sigma is a data-driven methodology used to improve processes by reducing defects and variation, leading to increased efficiency and quality.
Six Sigma focuses on identifying and eliminating causes of defects and errors in a process.
It uses statistical analysis to measure and improve process performance.
Six Sigma aims for a process capability of 6 standard deviations between the process mean and the nearest specification limit.
It can be applied in plant level by analyzing p...read more
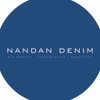
Asked in Nandan Denim

Q. What is the daily prodn and efficiency status ? What is the present Uster quality level ? How is the attrition and turnover rate in this group
The daily production and efficiency status, Uster quality level, and attrition/turnover rate are key metrics for evaluating the performance of the QA team.
Daily production and efficiency status are monitored to ensure targets are being met and to identify areas for improvement.
Uster quality level indicates the standard of quality being maintained in the production process.
Attrition and turnover rates reflect the stability of the QA team and can impact overall performance.
Regu...read more
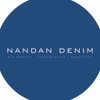
Asked in Nandan Denim

Q. What is the current attrition rate in the company?
The present attrition rate in the company is 15%.
The current attrition rate is 15%.
Attrition rate can be calculated by dividing the number of employees who left the company by the average number of employees, then multiplying by 100.
High attrition rates can indicate potential issues within the company such as poor work culture, lack of growth opportunities, or inadequate compensation.
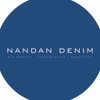
Asked in Nandan Denim

Q. What are the common TQM concepts used?
Common TQM concepts include continuous improvement, customer focus, employee involvement, and process management.
Continuous improvement: Striving for incremental improvements in processes and products over time.
Customer focus: Meeting customer needs and expectations through quality products and services.
Employee involvement: Engaging employees in quality improvement initiatives and decision-making.
Process management: Managing and optimizing processes to ensure quality and eff...read more
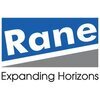
Asked in Rane (Madras)

Q. How do you handle customer complaints?
Handling customer complaints involves active listening, empathy, prompt resolution, and follow-up.
Listen attentively to the customer's complaint without interrupting
Show empathy and understanding towards the customer's concerns
Apologize for any inconvenience caused and assure the customer that their complaint will be addressed
Resolve the complaint promptly and effectively, offering appropriate solutions or compensation if necessary
Follow up with the customer to ensure their s...read more
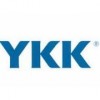
Asked in YKK

Q. What is Six Sigma?
Six Sigma is a data-driven methodology used to improve business processes by reducing defects and variability.
Six Sigma aims to achieve near-perfect quality by minimizing process variation.
It uses statistical analysis to identify and eliminate the root causes of defects.
The goal is to reduce defects to a level of 3.4 per million opportunities (DPMO).
Six Sigma follows a structured approach known as DMAIC: Define, Measure, Analyze, Improve, and Control.
It is widely used in indu...read more
Asked in Discover Tooling & Precision Works

Q. What is the PFMEA process?
PFMEA is a process used to identify and mitigate potential failures in a product or process.
PFMEA stands for Process Failure Mode and Effects Analysis.
It is a systematic approach to identify and prioritize potential failure modes and their effects.
The process involves analyzing each step of a process or component to identify failure modes, their causes, and potential effects.
Risk priority numbers (RPNs) are assigned to each failure mode to prioritize actions for mitigation.
PF...read more
Asked in Discover Tooling & Precision Works

Q. What is the PPAP document?
PPAP stands for Production Part Approval Process. It is a standardized documentation process used in manufacturing to ensure that parts meet quality requirements.
PPAP is a set of documents and records that manufacturers must submit to their customers to demonstrate that the production process can consistently produce parts that meet specifications.
It includes documents such as control plans, process flow diagrams, measurement system analysis, and sample parts.
PPAP helps ensur...read more
Share interview questions and help millions of jobseekers 🌟
Asked in Jai Surgicals

Q. What are your experiences with validation and calibration?
Validation and calibration are important processes to ensure accuracy and reliability of measurements and data.
Validation involves testing and verifying that a system or process meets its intended requirements and specifications.
Calibration involves comparing measurements taken by a device or instrument to a known standard to ensure accuracy.
Both validation and calibration are important in industries such as healthcare, manufacturing, and research.
Examples of validation and c...read more
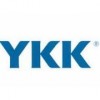
Asked in YKK

Q. What is Kaizen?
Kaizen is a Japanese term meaning continuous improvement. It refers to the philosophy of making small, incremental changes to improve processes and systems.
Kaizen is a key principle of Lean manufacturing and Six Sigma methodologies.
It involves identifying and eliminating waste, reducing defects, and improving efficiency.
Kaizen encourages employee involvement and empowerment in the improvement process.
Examples of Kaizen activities include implementing standardized work procedu...read more
Asked in Discover Tooling & Precision Works

Q. What is the 8D/SCAP methodology?
8D/SCAP is a problem-solving methodology used in quality assurance to identify, analyze, and resolve issues.
8D stands for Eight Disciplines and SCAP stands for Structured Problem Analysis and Correction.
It is a systematic approach that involves a team-based problem-solving process.
The 8D/SCAP methodology includes steps such as defining the problem, establishing a team, identifying root causes, implementing corrective actions, and preventing recurrence.
It is commonly used in i...read more
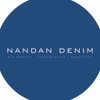
Asked in Nandan Denim

Q. Present burning problems
Some burning problems include lack of automation in testing, inconsistent test environments, and inadequate test coverage.
Lack of automation in testing leads to slower testing processes and increased chances of human error.
Inconsistent test environments can result in unreliable test results and difficulty in reproducing bugs.
Inadequate test coverage may lead to undetected bugs in production.
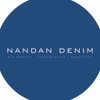
Asked in Nandan Denim

Q. Present quality level
Our current quality level is meeting industry standards but there is room for improvement.
Regular quality audits are conducted to ensure compliance with standards
Defect tracking and resolution process is in place
Continuous improvement initiatives are being implemented
Customer feedback is actively collected and analyzed
Interview Questions of Similar Designations
Interview Experiences of Popular Companies
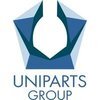

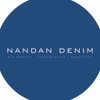

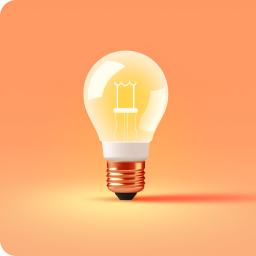
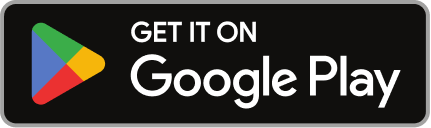
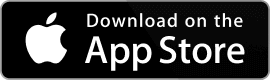
Reviews
Interviews
Salaries
Users
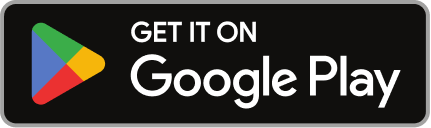
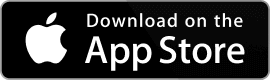