Quality Manager
200+ Quality Manager Interview Questions and Answers
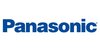
Asked in Panasonic Life Solutions India

Q. What is sig sigma? where it is used and what is the purpose?
Six Sigma is a data-driven methodology used to improve processes by reducing defects and variations.
Six Sigma is a quality management methodology that aims to improve processes by identifying and removing causes of defects and minimizing variability.
It uses statistical analysis to measure and improve process performance, aiming for no more than 3.4 defects per million opportunities.
Six Sigma is widely used in industries such as manufacturing, healthcare, finance, and telecomm...read more
Asked in Velvin Paper Products

Q. What is ISO and what is major difference in ISO 2008 : ISO 2015. And how to control them
ISO is a set of international standards for quality management systems. The major difference between ISO 2008 and ISO 2015 is the structure.
ISO stands for International Organization for Standardization
ISO provides a framework for quality management systems
ISO 2008 had a different structure than ISO 2015
ISO 2015 follows a high-level structure (HLS) that is common to all ISO management system standards
To control ISO standards, organizations must implement and maintain a quality...read more
Quality Manager Interview Questions and Answers for Freshers
Asked in Seal Industries

Q. 1. What is contingency plan, 2. What is MSA 3. What is SPC, 4. What is layout inspection frequency, 5. howmany documents are there in ppap , 5. What are apqp, fmea, imds, all related to QA and QMS.
Contingency plan is a backup plan to address unexpected events, MSA is Measurement System Analysis, SPC is Statistical Process Control, layout inspection frequency is how often inspections are conducted, PPAP has multiple documents, APQP, FMEA, and IMDS are all related to QA and QMS.
Contingency plan is a plan devised for an unexpected event that may affect the organization's ability to function.
MSA (Measurement System Analysis) is a method used to assess the variation in meas...read more
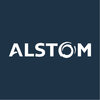
Asked in Alstom Transportation

Q. How you are handling customer inspection? If customer found the defect how you manage, how you are going to take action to avoid repetition
Handling customer inspection involves prompt action on defects found, implementing corrective measures, and preventing recurrence.
Promptly address customer concerns and investigate the root cause of the defect
Implement corrective actions to resolve the issue and prevent recurrence
Communicate with the customer regarding the actions taken and ensure satisfaction
Conduct internal audits to identify potential areas of improvement
Train employees on quality standards and procedures ...read more
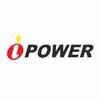
Asked in Anand I-power

Q. How will you handle a customer when there is a field failure?
I will prioritize communication and investigation to identify the root cause and provide a timely resolution to the customer.
Listen to the customer's concerns and acknowledge their frustration
Gather all necessary information about the failure and investigate the root cause
Provide regular updates to the customer on the progress of the investigation and resolution
Offer a timely and satisfactory resolution to the customer, such as a replacement or repair
Implement corrective acti...read more
Asked in Velvin Paper Products

Q. Describe the glue-making process and the ratios required to achieve good strength in glue for corrugation.
The glue making process for corrugation requires specific ratios to achieve good strength.
The glue should have a good balance of solids and water.
The ratio of solids to water should be around 50:50.
The type of adhesive used can also affect the strength of the glue.
The temperature and humidity of the environment can also impact the glue's strength.
Testing the glue's strength through various methods is important to ensure quality.
Examples of testing methods include lap shear, p...read more
Quality Manager Jobs
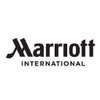
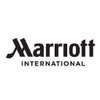
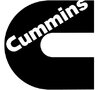
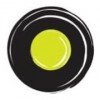
Asked in Ola Cabs

Q. How would you set up an audit for a cab attachment process?
Setting an audit for a cab attachment process involves defining criteria, planning, and executing the audit effectively.
Define audit objectives: Ensure compliance with safety and quality standards.
Identify key processes: Focus on cab attachment steps like alignment and fastening.
Develop audit checklist: Include items like torque specifications and visual inspections.
Schedule audits: Regular intervals, e.g., monthly or quarterly, to ensure consistency.
Train auditors: Ensure th...read more
Asked in NewAge Fire Protection Industries

Q. What's the difference between quality control and quality assurance?
Quality control is reactive and focuses on identifying defects, while quality assurance is proactive and focuses on preventing defects.
Quality control involves inspecting products or services to identify defects and ensure they meet standards.
Quality assurance involves implementing processes and procedures to prevent defects from occurring in the first place.
Quality control is reactive, meaning it occurs after the product or service has been produced.
Quality assurance is proa...read more
Share interview questions and help millions of jobseekers 🌟
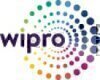
Asked in Wipro

Q. In a medical device manufacturing industry, what processes need to be monitored according to the current ISO 13485 and MDR regulations, especially regarding safety and risk management?
Monitoring processes in medical device manufacturing is crucial for compliance with ISO 13485 and MDR regulations, focusing on safety and risk management.
Establish a risk management process to identify, evaluate, and control risks associated with medical devices.
Conduct regular audits and inspections to ensure compliance with ISO 13485 requirements.
Implement a robust design control process to ensure safety and efficacy of the device.
Monitor post-market surveillance data to id...read more
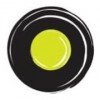
Asked in Ola Cabs

Q. There is an increase in customer complaints, how will you address it?
To address increased customer complaints, I would analyze data, engage stakeholders, and implement corrective actions.
Conduct a root cause analysis to identify the main issues behind the complaints.
Engage with customers to gather feedback and understand their concerns better.
Implement corrective actions based on findings, such as improving product quality or service delivery.
Monitor the effectiveness of changes through follow-up surveys and complaint tracking.
Train staff on q...read more
Asked in R.L.Khanna & Co. (Overseas)

Q. What can you explain about fabric testing, weaving, dyeing, the manufacturing process of home furnishing products, and the inspection procedures involved?
Fabric testing, weaving, dyeing, manufacturing process of home furnishing products, and inspection procedures are essential aspects of ensuring quality in the textile industry.
Fabric testing involves evaluating the quality and performance of fabrics through various tests such as tear strength, colorfastness, and shrinkage.
Weaving is the process of interlacing two sets of yarn to create fabric, with different weaving techniques producing different types of fabrics like plain w...read more

Asked in Superhouse

Q. How would you control the quality of this factory?
To control the quality of the factory, various measures can be implemented.
Implement a quality management system
Establish quality control processes and procedures
Conduct regular inspections and audits
Train and educate employees on quality standards
Monitor and analyze production data
Implement corrective and preventive actions
Collaborate with suppliers to ensure quality materials
Implement continuous improvement initiatives
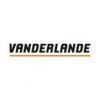
Asked in Vanderlande Industries

Q. How do you deal with cross-functional/multi-disciplinary issues?
I handle cross functional/multi disciplinary issues by promoting effective communication, collaboration, and problem-solving.
Encourage open and transparent communication between different teams and departments
Facilitate regular meetings or workshops to address and resolve any conflicts or issues
Promote a culture of collaboration and teamwork
Implement effective problem-solving techniques, such as root cause analysis or brainstorming sessions
Ensure clear roles, responsibilities...read more
Asked in Loomtex Exports

Q. Can you manage a team to assure the quality of home textile products at each stage?
Yes, I can manage a team to assure quality of home textile products in each stage.
I have experience in managing teams and ensuring quality in the textile industry.
I would establish clear quality standards and guidelines for each stage of production.
I would train and educate team members on quality control processes and techniques.
Regular inspections and audits would be conducted to identify and address any quality issues.
I would collaborate with suppliers and manufacturers to...read more
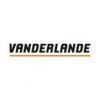
Asked in Vanderlande Industries

Q. How do you explain issues and potential solutions to acquire resources?
To explain issues and potential solutions to get resources, it is important to clearly communicate the problem, demonstrate the impact, propose feasible solutions, and highlight the benefits.
Clearly communicate the problem and its impact on quality and productivity
Provide data and evidence to support the need for additional resources
Propose feasible solutions that address the root cause of the issues
Highlight the benefits of allocating resources, such as improved quality, red...read more
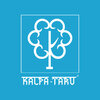
Asked in Kalpataru Limited

Q. What is the difference between FE550 and FE550D, and what tests are performed on them in the laboratory?
FE550 and FE550D are different grades of steel with varying properties and testing standards.
FE550 is a grade of structural steel, while FE550D is a ductile variant with enhanced toughness.
FE550 is typically used in construction, while FE550D is preferred in seismic zones due to its ductility.
Common tests for FE550 include tensile strength, yield strength, and elongation tests.
FE550D undergoes additional tests for impact resistance and toughness at low temperatures.
Asked in NewAge Fire Protection Industries

Q. Are you capable of preparing a Quality Assurance Plan (QAP)?
Yes, I am capable of preparing a quality assurance plan (QAP).
I have experience in developing QAPs for various projects.
I am familiar with industry standards and regulations related to quality assurance.
I can identify potential risks and develop strategies to mitigate them.
I can collaborate with cross-functional teams to ensure the QAP is comprehensive and effective.
Asked in R.L.Khanna & Co. (Overseas)

Q. Can you explain what a technical audit and compliance process involves?
A technical audit and compliance process involves evaluating systems, processes, and procedures to ensure they meet industry standards and regulations.
Conducting thorough reviews of technical documentation and procedures
Identifying areas of non-compliance or potential risks
Implementing corrective actions to address any issues found
Ensuring ongoing monitoring and maintenance of compliance measures
Collaborating with various departments to ensure alignment with regulations
Exampl...read more
Asked in Seal Industries

Q. What are apqp, fmea, imds, all related to QA and QMS.
APQP, FMEA, and IMDS are all tools and processes related to Quality Assurance (QA) and Quality Management Systems (QMS).
APQP (Advanced Product Quality Planning) is a framework used in the automotive industry to define and establish the steps necessary to ensure that a product satisfies the customer.
FMEA (Failure Mode and Effects Analysis) is a structured approach to identifying and prioritizing potential failure modes in a system, product, or process, and their effects.
IMDS (...read more
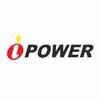
Asked in Anand I-power

Q. Describe your experience with the PPAP and APQP procedures.
PPAP and APQP are essential quality assurance processes in manufacturing, ensuring product quality and compliance.
PPAP (Production Part Approval Process) ensures that suppliers meet quality standards before mass production.
APQP (Advanced Product Quality Planning) is a framework for developing products and processes to ensure quality.
PPAP includes five levels of submission, with Level 1 being the simplest and Level 5 requiring the most documentation.
APQP involves phases like p...read more
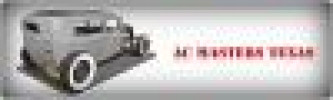
Asked in Acmas Technologies

Q. What instruments using in last company and Least count of vernier,micrometer and team leader and co operation with engineers team handling,controlling etc.
In my last company, I utilized various precision instruments for quality control, ensuring accurate measurements and effective teamwork.
Vernier Caliper: Used for measuring internal and external dimensions with a least count of 0.02 mm, ensuring precise measurements in product specifications.
Micrometer: Employed for measuring small dimensions with a least count of 0.01 mm, crucial for components requiring high accuracy.
Team Leadership: Coordinated with engineers to implement q...read more
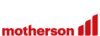
Asked in Samvardhana Motherson Group

Q. What products are manufactured in your current organization?
Our current organization manufactures a range of electronic products.
Electronic gadgets such as smartphones, tablets, and laptops
Home appliances like refrigerators, washing machines, and air conditioners
Audio and video equipment like speakers, headphones, and televisions
Industrial equipment like generators, motors, and transformers
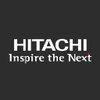
Asked in Hitachi Astemo

Q. If the job requires you to work overtime, would you be willing to do so?
As a Quality Manager, I understand the importance of flexibility and commitment to meet work requirements, including extra time when necessary.
Quality assurance often requires additional time to ensure standards are met, especially during critical project phases.
For example, if a product fails a quality check, I would prioritize addressing the issue, even if it means working late.
Collaboration with team members may also require extra hours to align on quality objectives and e...read more
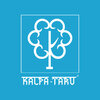
Asked in Kalpataru Limited

Q. What are the different types of waterproofing, and on what basis should they be selected?
Waterproofing types include membranes, coatings, and sealants, chosen based on application, environment, and material compatibility.
1. Membrane Waterproofing: Used for roofs and foundations; examples include bituminous and PVC membranes.
2. Liquid Coating: Applied as a liquid that cures to form a waterproof layer; examples are polyurethane and epoxy coatings.
3. Cementitious Waterproofing: Ideal for water tanks and basements; uses cement-based products for durability.
4. Sealant...read more

Asked in V.S. Enterprises

Q. Define 8D and CAPA . What is 8 D . How to control in house rejection
8D and CAPA are problem-solving methodologies used in quality management. 8D is an eight-step process and CAPA stands for Corrective and Preventive Action.
8D is an eight-step process used to identify, correct, and prevent problems in a product or process.
CAPA is a process used to investigate and address the root cause of a problem, and to prevent it from recurring.
To control in-house rejection, it is important to implement a robust quality control system, including regular in...read more

Q. How would you manage a conflict through a positive approach?
I approach conflict management by fostering open communication, understanding perspectives, and seeking collaborative solutions.
Encourage open dialogue: Create a safe space for all parties to express their views without fear of judgment.
Active listening: Demonstrate empathy by listening attentively to understand the underlying concerns of each party.
Identify common goals: Focus on shared objectives to shift the conversation from conflict to collaboration.
Facilitate compromise...read more
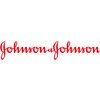
Asked in Johnson & Johnson

Q. What is your role in handling QMS activities?
As a Quality Manager, my role in handling QMS activities includes developing, implementing, and maintaining the QMS system.
Developing and implementing QMS policies and procedures
Ensuring compliance with regulatory requirements
Conducting internal audits and identifying areas for improvement
Managing corrective and preventive actions
Providing training and support to employees
Monitoring and analyzing QMS performance metrics
Reporting to senior management on QMS effectiveness
Collab...read more
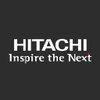
Asked in Hitachi Astemo

Q. Which type of tool do you use to analyze defects?
I use various tools such as Pareto charts, fishbone diagrams, control charts, and statistical software to analyze defects.
Pareto charts help identify the most significant defects by showing the frequency of each type of defect.
Fishbone diagrams (Ishikawa diagrams) help identify potential causes of defects by categorizing them into different factors like people, methods, materials, etc.
Control charts help monitor the stability of a process by plotting data points over time and...read more
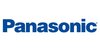
Asked in Panasonic Life Solutions India

Q. What are Cp and Cpk values?
Cp & Cpk values are statistical measurements used to assess the capability of a process to produce products within specifications.
Cp is a process capability index that measures how well a process can meet the specifications of a product.
Cpk is a process capability index that takes into account the centering of the process mean with respect to the specification limits.
A Cp value of 1 indicates that the process spread is equal to the specification spread, while a Cp value great...read more
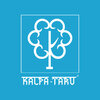
Asked in Kalpataru Limited

Q. Can higher grade materials be used for early de-shuttering than those typically required?
Using higher grade materials for early de-shuttering can enhance structural integrity but may not always be necessary.
Higher grade materials can provide better strength and durability, allowing for earlier de-shuttering.
For example, using high-strength concrete can reduce curing time and allow for earlier removal of formwork.
However, this may increase costs and may not be justified if standard materials meet project requirements.
It's essential to consider the specific project...read more
Interview Questions of Similar Designations
Interview Experiences of Popular Companies
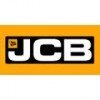
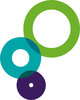
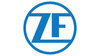
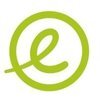

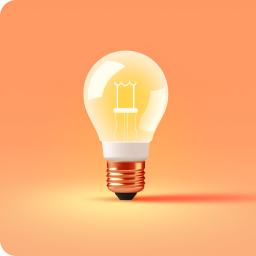
Calculate your in-hand salary
Confused about how your in-hand salary is calculated? Enter your annual salary (CTC) and get your in-hand salary
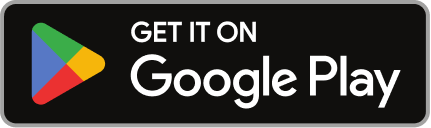
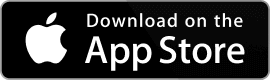
Reviews
Interviews
Salaries
Users
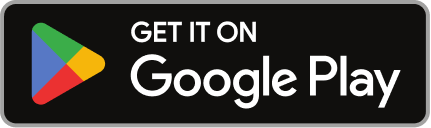
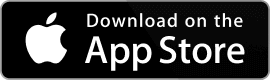