Ipqa Officer
60+ Ipqa Officer Interview Questions and Answers
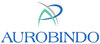
Asked in Aurobindo Pharma

Q. Why line clearance to be taken and were it is mentioned.
Line clearance is taken to ensure safety and prevent cross-contamination in pharmaceutical manufacturing.
Line clearance is a procedure followed in pharmaceutical manufacturing to ensure that all equipment, materials, and personnel are removed from a production line before starting a new product or batch.
It is mentioned in various regulatory guidelines such as Good Manufacturing Practices (GMP) and Standard Operating Procedures (SOPs).
Line clearance helps prevent cross-contami...read more
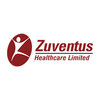
Asked in Zuventus Healthcare

Q. What are the critical parameters in BMR and BPR?
Critical parameters in BMR and BPR
Critical parameters in BMR include temperature, pH, agitation rate, and dissolved oxygen level
Critical parameters in BPR include temperature, pressure, mixing speed, and gas flow rate
Monitoring and controlling these parameters is essential for ensuring product quality and consistency
Ipqa Officer Interview Questions and Answers for Freshers


Q. 1)What is Stability? 2)What is the shelf life? 3)What is line clearance? 4) What is the Critical process parameter?
Answers to questions related to IPQA Officer interview
Stability refers to the ability of a drug to maintain its physical, chemical, and microbiological properties over time
Shelf life is the period of time during which a drug product is expected to remain within its approved specifications if stored under defined conditions
Line clearance is the process of ensuring that all equipment, materials, and personnel are removed from a production area before starting a new process
Criti...read more
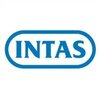
Asked in Intas Pharmaceuticals

Q. Which apparatus have you handled?
I have handled various apparatus including HPLC, UV-Vis spectrophotometer, dissolution apparatus, and pH meter.
Handled HPLC for analysis of drug substances and drug products
Operated UV-Vis spectrophotometer for quantitative analysis of drugs
Used dissolution apparatus for testing drug release from solid dosage forms
Calibrated and used pH meter for measuring pH of solutions
Familiar with other laboratory apparatus such as balances, pipettes, and burettes
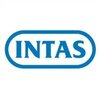
Asked in Intas Pharmaceuticals

Q. What are the different types of process validation?
There are three types of process validation: prospective, concurrent, and retrospective.
Prospective validation is performed before the process is put into routine use.
Concurrent validation is performed during routine production.
Retrospective validation is performed on processes that have been in routine use without formal validation.
Each type of validation requires different approaches and documentation.
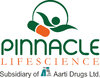
Asked in Pinnacle Life Science

Q. 1 Defination of tablets 2 Type of doses form 3 Weight veriation limit of tablet as per IP ,B and USP . 4. About schedule 5 process of balance calibration.
Tablets are solid dosage forms containing active pharmaceutical ingredients and excipients, compressed into a specific shape and size for oral administration.
Tablets are one of the most common types of solid dosage forms used in pharmaceuticals.
They can be classified based on their release mechanism (immediate release, extended release, etc.) or formulation (film-coated, chewable, effervescent, etc.).
Weight variation limits for tablets are specified in pharmacopoeias like IP,...read more
Ipqa Officer Jobs


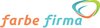
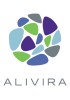
Asked in Alivira Animal Health

Q. What are the types of observations and how are they classified?
Observations can be classified as critical, major, or minor based on their impact on quality and compliance.
Critical observations have a significant impact on product quality and regulatory compliance.
Major observations have a moderate impact on product quality and regulatory compliance.
Minor observations have a minimal impact on product quality and regulatory compliance.
Observations can be related to equipment, processes, documentation, or personnel.
Examples of critical obse...read more
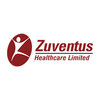
Asked in Zuventus Healthcare

Q. Process monitoring in manufacturing and packing
Process monitoring in manufacturing and packing involves closely observing and controlling the various stages of production to ensure quality and efficiency.
Monitoring the parameters and variables that affect the manufacturing and packing processes
Regularly checking and recording data such as temperature, pressure, and time
Using statistical process control techniques to analyze data and identify trends or deviations
Implementing corrective actions when necessary to maintain pr...read more
Share interview questions and help millions of jobseekers 🌟
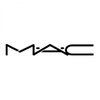
Asked in MAC

Q. If a tablet batch fails, what measures will you take as a QA officer?
I would investigate the root cause of the failure, implement corrective actions, and ensure proper documentation and communication.
Investigate the root cause of the failure by reviewing batch records, testing data, and manufacturing processes
Implement corrective actions to address the identified issues and prevent recurrence
Ensure proper documentation of the investigation, actions taken, and communication with relevant stakeholders
Collaborate with cross-functional teams to de...read more
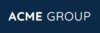
Asked in Acme Formulation

Q. How do you perform a leak test?
Leak test is performed by subjecting the product to a specific pressure and observing for any pressure drop over a specified time period.
Select appropriate equipment for the test
Set the pressure and time parameters as per the product specifications
Connect the product to the equipment and initiate the test
Observe for any pressure drop during the test period
Record the results and take necessary actions if the product fails the test
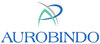
Asked in Aurobindo Pharma

Q. Sensors in vial washing Machine and vial depyrogenated tunnel.
Sensors are used in vial washing machines and vial depyrogenated tunnels to ensure proper cleaning and sterilization.
Sensors detect the presence of contaminants or particles in the vials during the washing process.
Sensors also monitor the temperature and humidity levels in the depyrogenated tunnel to ensure proper sterilization.
If the sensors detect any issues, the machine will automatically stop and alert the operator.
Regular calibration and maintenance of the sensors is nec...read more
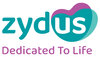
Asked in Zydus Healthcare

Q. If the continuous line clearance activities fail, how should they be corrected?
Addressing failures in continuous line clearance requires systematic evaluation and corrective measures to ensure compliance and efficiency.
Conduct a root cause analysis to identify underlying issues, such as equipment malfunction or procedural gaps.
Implement corrective actions, such as retraining staff on proper line clearance protocols to prevent future failures.
Enhance monitoring systems to provide real-time feedback on line clearance activities, allowing for immediate adj...read more
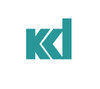
Asked in Kilitch Drugs

Q. What are wet and dry granulation?
Wet and dry granulation are two methods of forming granules from powder materials.
Wet granulation involves adding a liquid binder to the powder mixture, which is then agitated and dried to form granules.
Dry granulation involves compacting the powder mixture without the use of a liquid binder, using a roller compactor or tablet press.
Wet granulation is often used for materials that are difficult to compress, while dry granulation is preferred for materials that are sensitive t...read more
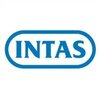
Asked in Intas Pharmaceuticals

Q. What do you know about UV?
UV stands for ultraviolet radiation, which is a type of electromagnetic radiation with a wavelength shorter than that of visible light.
UV radiation is commonly used for sterilization and disinfection purposes.
It can also cause damage to living organisms, including humans, if exposure is prolonged.
UV radiation is divided into three categories: UVA, UVB, and UVC.
UVA and UVB are responsible for skin tanning and sunburns, while UVC is absorbed by the Earth's atmosphere and does n...read more
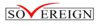
Asked in Sovereign Pharma

Q. Explain the difference between primary and secondary packaging.
Primary packing is the packaging that directly contains the product, while secondary packing is the packaging that contains the primary packaging.
Primary packing is in direct contact with the product, while secondary packing is not.
Primary packing protects the product from contamination, damage, and tampering, while secondary packing provides additional protection during transportation and storage.
Examples of primary packing include blister packs, vials, and ampoules, while e...read more
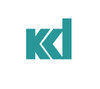
Asked in Kilitch Drugs

Q. What are the responsibilities of the store department?
The store department manages inventory, procurement, and distribution of materials and supplies within an organization.
Inventory Management: Keeping track of stock levels to avoid shortages or overstocking.
Procurement: Sourcing and purchasing materials needed for operations, such as medical supplies in a hospital.
Distribution: Ensuring timely delivery of supplies to various departments, like delivering surgical instruments to the operating room.
Record Keeping: Maintaining acc...read more
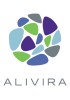
Asked in Alivira Animal Health

Q. What is the difference between ANF and Nutch filter?
ANF and Nutch filter are both used in the field of information retrieval, but they have different purposes and functionalities.
ANF (Approximate Nearest Neighbor Filtering) is a technique used to efficiently filter out irrelevant data points in a dataset based on their proximity to a query point.
Nutch filter, on the other hand, is a component of the Apache Nutch web crawler framework that is used to filter and prioritize web pages during the crawling process.
ANF is primarily u...read more

Asked in Wallace Pharmaceuticals

Q. What are the storage conditions for different stability studies?
Different stability studies require specific storage conditions to ensure accurate results.
Storage conditions vary based on the type of stability study being conducted (e.g. accelerated, long-term, intermediate)
Common storage conditions include temperature, humidity, and light exposure
Examples of storage conditions: 25°C/60% RH, 40°C/75% RH, 2-8°C
It is important to follow the specified storage conditions to maintain the integrity of the samples
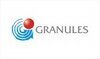
Asked in Granules India Limited

Q. How do you handle out-of-limits observations during compression?
Addressing out of limits observations during compression involves investigation, documentation, and corrective actions.
Identify the specific parameter that is out of limits, e.g., tablet weight or hardness.
Investigate the root cause by reviewing the compression process, equipment calibration, and material properties.
Document the observation in a deviation report, detailing the nature of the out-of-limit condition.
Implement corrective actions, such as adjusting machine setting...read more
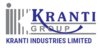
Asked in Kranti Industries

Q. What is a SOP?
A SOP (Standard Operating Procedure) is a documented step-by-step guide that outlines the approved methods to perform a specific task or process.
SOPs are used to ensure consistency and quality in operations.
They provide clear instructions and guidelines for employees to follow.
SOPs can cover various areas such as manufacturing, quality control, safety, and more.
Examples of SOPs include procedures for equipment calibration, batch record review, and cleaning validation.
SOPs are...read more
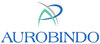
Asked in Aurobindo Pharma

Q. Challenge tests in packing.
Challenge tests in packing involve conducting tests to ensure the packaging materials and processes meet the required standards.
Challenge tests assess the integrity and performance of packaging materials.
These tests simulate real-life conditions to evaluate the packaging's ability to protect the product.
Examples of challenge tests include drop tests, vibration tests, and temperature tests.
The purpose of challenge tests is to identify any weaknesses or potential issues in the ...read more
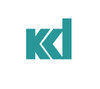
Asked in Kilitch Drugs

Q. How do you perform line clearance?
Line clearance is the process of ensuring that a production line or equipment is ready for use or changeover.
Perform a visual inspection of the production line or equipment to ensure it is clean and free from any previous product or material.
Verify that all necessary materials, tools, and documents are available and ready for use.
Check that all safety measures and precautions are in place, such as lockout/tagout procedures.
Ensure that all previous batch records or documentati...read more

Asked in Wallace Pharmaceuticals

Q. How much water is taken for rinse collection?
The amount of water taken for rinse collection depends on the specific procedure and requirements of the IPQA Officer.
The amount of water taken for rinse collection is typically specified in the standard operating procedures (SOPs) of the company.
It is important to follow the instructions in the SOPs to ensure accurate and consistent results.
The volume of water required for rinse collection may vary depending on the size and type of equipment being tested.
In some cases, a spe...read more
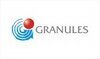
Asked in Granules India Limited

Q. What are the process parameters in compression?
Compression in pharmaceuticals involves key parameters like pressure, speed, and material properties affecting tablet quality.
Pressure: The force applied during compression affects tablet density and hardness. Example: Higher pressure can lead to harder tablets.
Speed: The rate of compression can influence the uniformity of the tablet. Example: Faster speeds may lead to inconsistent tablet weight.
Material Properties: The characteristics of the powder blend, such as flowability...read more
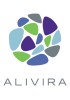
Asked in Alivira Animal Health

Q. Explain the difficulties you have faced during line clearance.
Difficulties during line clearance include time constraints, equipment availability, and potential contamination risks.
Time constraints can make it challenging to thoroughly clean and inspect the production line before starting a new batch.
Limited availability of cleaning equipment or resources can hinder the efficiency of line clearance.
There is a risk of cross-contamination if residues or contaminants from the previous product are not completely removed.
Ensuring proper docu...read more
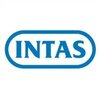
Asked in Intas Pharmaceuticals

Q. Inprocess during batch manu
Inprocess checks during batch manufacturing
Inprocess checks are performed during batch manufacturing to ensure quality and consistency
These checks include monitoring of critical process parameters such as temperature, pressure, and pH
Sampling and testing of the product at various stages of manufacturing is also done to ensure compliance with specifications
Documentation of all inprocess checks is important for traceability and quality assurance
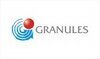
Asked in Granules India Limited

Q. What are CQA and CPP during granule formation?
CQA refers to Critical Quality Attributes, while CPP denotes Critical Process Parameters in granule formation.
CQA are the physical, chemical, biological, or microbiological properties that must be controlled to ensure product quality.
Examples of CQA include particle size, moisture content, and dissolution rate of granules.
CPP are the parameters that can be controlled during the manufacturing process to ensure that CQA are met.
Examples of CPP include mixing time, granulation t...read more
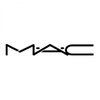
Asked in MAC

Q. What is LOD and why is it performed?
LOD stands for Limit of Detection. It is the lowest concentration of a substance that can be reliably detected by a particular analytical procedure.
LOD is important in quality control to ensure that the analytical method is sensitive enough to detect low levels of impurities or contaminants.
It helps in determining the accuracy and reliability of the analytical method.
LOD is typically determined by analyzing samples with known low concentrations of the substance and measuring ...read more
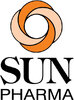
Asked in Sun Pharmaceutical Industries

Q. What I do in manufacturing area
In the manufacturing area, I ensure that processes are carried out according to standard operating procedures to maintain quality and compliance.
Performing in-process checks to ensure quality standards are met
Monitoring equipment calibration and maintenance schedules
Documenting all activities and deviations for review
Implementing corrective and preventive actions as needed
Training manufacturing personnel on quality procedures
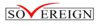
Asked in Sovereign Pharma

Q. Explain what IPQA is.
IPQA stands for In-Process Quality Assurance. It is a quality control process that ensures products meet quality standards during production.
IPQA involves monitoring and verifying the quality of products during the manufacturing process.
It includes checking raw materials, equipment, and processes to ensure they meet quality standards.
IPQA helps identify and correct any issues that may arise during production, preventing defects and ensuring consistent quality.
Examples of IPQA...read more
Interview Questions of Similar Designations
Interview Experiences of Popular Companies
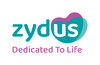
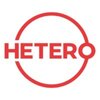
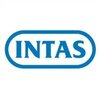
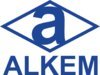
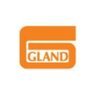
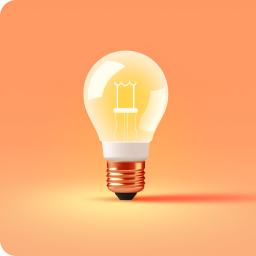
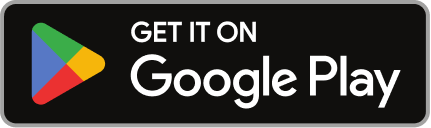
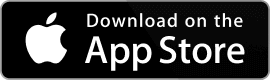
Reviews
Interviews
Salaries
Users
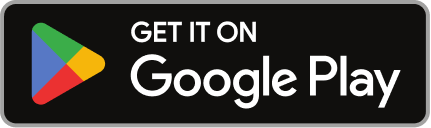
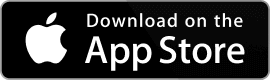