Senior Design Engineer
200+ Senior Design Engineer Interview Questions and Answers

Asked in ZF India Technology Center

Q. Noise, Vibration, and Harshness (NVH) in gearboxes are influenced by several factors, which can broadly be categorized into design, material, manufacturing, and operational factors. Here are some key factors af...
read moreAddressing NVH in gearboxes involves optimizing design, material, manufacturing, and operational factors.
Optimizing gear geometry like tooth profile and helix angle can reduce noise.
Proper material quality and heat treatment can minimize vibrations.
Precision machining and assembly quality are crucial for reducing NVH.
Consider load conditions, lubrication, and operational speed for NVH control.
Environmental factors like temperature and external vibrations also impact gearbox N...read more
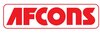
Asked in Afcons Infrastructure

Q. How many methods are used to forecast population?
There are multiple methods used to forecast population.
Demographic analysis
Cohort-component method
Time series analysis
Mathematical models
Survival analysis
Migration analysis
Senior Design Engineer Interview Questions and Answers for Freshers
Asked in Mohite Electronics

Q. 1. What is GD and T? 2. Selection of motor as per weight. 3. Types of gears. 4 Basic conveyor related questions.
GD&T is a system for defining and communicating engineering tolerances. Motor selection depends on weight, power, and speed requirements. Types of gears include spur, helical, bevel, and worm. Conveyor questions may relate to design, operation, or maintenance.
GD&T is an abbreviation for Geometric Dimensioning and Tolerancing, which is a system for defining and communicating engineering tolerances.
When selecting a motor for a particular application, factors to consider include...read more

Asked in GGS Engineering Services

Q. How do you decide whether a sheet metal bracket or casting is required?
The decision between sheetmetal bracket or casting is based on factors like complexity, strength, cost, and production volume.
Consider the complexity of the part - sheetmetal brackets are generally simpler to design and manufacture compared to castings.
Evaluate the required strength and load-bearing capacity - castings are often preferred for heavy-duty applications due to their superior strength.
Assess the cost implications - sheetmetal brackets are usually more cost-effecti...read more
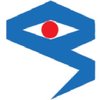
Asked in Vision Mechatronics Private Limited

Q. What is the internal band radius for a rod sheet with a thickness of 0.3 mm and a total length of 100 meters?
The internal band radius for a rod sheet can be calculated using the formula: radius = thickness / (2 * pi)
Calculate the internal band radius using the formula: radius = thickness / (2 * pi)
For a rod sheet with a thickness of 0.3 mm, the internal band radius would be 0.0477 mm
The total length of 100 meters is not relevant to calculating the internal band radius
Asked in Bbm Acoustic India

Q. What are the formulae of area of circle, rectangle, square, cone and formulae of volume of cube, cuboid, cylinder, cone, etc?
Formulae for area and volume of common shapes.
Area of circle: πr²
Area of rectangle: l x w
Area of square: s²
Area of cone: πr² + πrl
Volume of cube: s³
Volume of cuboid: l x w x h
Volume of cylinder: πr²h
Volume of cone: (1/3)πr²h
Senior Design Engineer Jobs
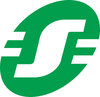
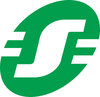
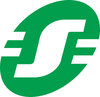

Asked in Becton Dickinson

Q. 1. Design controls used 2. Traceability between user requirement, Design input, and design output with an example 3. Difference between Design Verification and Design validation with an example 4. Why is design...
read moreInterview questions for Senior Design Engineer position
Design controls used to ensure product meets user requirements and regulatory standards
Traceability matrix used to link user requirements to design inputs and outputs
Design verification ensures design meets requirements, while design validation ensures product meets user needs
Design validation is performed to ensure product meets user needs in real-world scenarios
Standards such as ISO 13485 and FDA regulations are commonl...read more
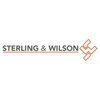
Asked in Sterling & Wilson

Q. What is the difference between a control module and a relay module?
A control module is a device that manages and regulates the operation of a system, while a relay module is a device that controls the flow of electrical current.
Control modules are responsible for monitoring and adjusting various parameters in a system, such as temperature, pressure, or speed.
Relay modules act as switches that open or close circuits to control the flow of electrical current.
Control modules are typically more complex and have advanced functionalities, while re...read more
Share interview questions and help millions of jobseekers 🌟
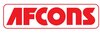
Asked in Afcons Infrastructure

Q. What is the design period for designing pumping machinery and ESR?
The design period for pumping machinery and ESR refers to the intended lifespan or duration of operation for the equipment.
The design period is typically determined based on factors such as expected usage, maintenance requirements, and technological advancements.
It is important to consider the design period when selecting materials, components, and manufacturing processes to ensure durability and reliability.
For example, in the design of a water pump for a municipal water sup...read more
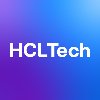
Asked in HCLTech

Q. What is the K-factor in sheet metal design? Explain.
K Factor is a constant value used in sheet metal design to calculate the neutral axis and bend allowance.
K Factor determines the amount of stretching that occurs during the bending process.
It is used to calculate the bend allowance, which is the length of the neutral axis in the bent part.
The K Factor value depends on the material being used, thickness, and bending method.
Common K Factor values range from 0.3 to 0.5 for most materials.
For example, a K Factor of 0.4 means that...read more
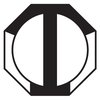

Q. Geometric dimensioning and tolerancing symbols and their use.
Geometric dimensioning and tolerancing symbols are used to specify the dimensions, tolerances, and geometric characteristics of a part.
GD&T symbols are used to communicate design requirements and ensure proper fit, function, and interchangeability of parts.
Some common GD&T symbols include position, concentricity, perpendicularity, and flatness.
These symbols are typically placed on engineering drawings and provide precise instructions for manufacturing and inspection processes...read more
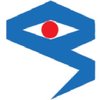
Asked in Vision Mechatronics Private Limited

Q. What factors do you consider when evaluating the quality of your design?
Factors considered include functionality, reliability, manufacturability, cost, and user experience.
Functionality - Does the design meet all the required specifications and perform its intended function?
Reliability - Will the design consistently perform as expected over its lifespan?
Manufacturability - Can the design be easily and cost-effectively produced?
Cost - Is the design cost-effective to produce and maintain?
User experience - Does the design meet the needs and expectat...read more
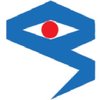
Asked in Vision Mechatronics Private Limited

Q. What is meant by band radius, and what factors should be considered in the design of sheet metal?
Band radius refers to the minimum inside radius that can be achieved in a sheet metal design.
Band radius is influenced by material thickness, bend angle, and tooling capabilities.
Factors to consider in sheet metal design include material selection, bend radius, and tolerances.
Design for manufacturability is crucial to ensure the sheet metal can be produced efficiently and accurately.

Q. What is the concept of Geometric Dimensioning and Tolerancing (GD&T) in depth, and what are the different types of GD&T and their symbols?
GD&T is a system for defining and communicating engineering tolerances using symbols on engineering drawings.
GD&T is a system used to define and communicate engineering tolerances on drawings.
It uses symbols to specify the allowable variations in form, size, orientation, and location of features.
Some common GD&T symbols include concentricity, perpendicularity, flatness, and position.
Types of GD&T include form controls, orientation controls, location controls, and runout contr...read more

Q. What types of different materials have you used, and what are their machinability characteristics and properties?
I have experience working with a variety of materials with different machinability characteristics and properties.
Metals: aluminum, steel, titanium
Plastics: ABS, polycarbonate, nylon
Composites: carbon fiber, fiberglass
Ceramics: alumina, zirconia
Understanding of material properties such as hardness, strength, thermal conductivity
Knowledge of machining processes like milling, turning, drilling
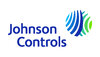
Asked in Johnson Controls

Q. What is Rosov, dbbv, BQD, Barrigade logic, PLC, SCADA
Rosov, dbbv, BQD, Barrigade logic, PLC, SCADA are all related to engineering and automation.
Rosov is a type of valve used in the oil and gas industry.
dbbv stands for Double Block and Bleed Valve, used to isolate sections of a pipeline.
BQD is a type of circuit breaker used in electrical systems.
Barrigade logic is a type of control system used in industrial automation.
PLC stands for Programmable Logic Controller, used to automate industrial processes.
SCADA stands for Supervisor...read more
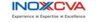
Asked in INOXCVA

Q. 1. PWHT & PFHT requirement / Cycle. 2. Difference between Stress relieving & Normalising. 3. U stamp nameplate description 4. UG- 44b significance 5. Rate of Heating/Cooling formula during heat treatment cycle....
read moreThe interview questions cover topics related to heat treatment, material properties, and industry standards in engineering.
PWHT (Post Weld Heat Treatment) and PFHT (Preheat and Post Weld Heat Treatment) are required for certain materials to relieve residual stresses and improve mechanical properties.
Stress relieving involves heating the material to a specific temperature and holding it for a period of time to reduce internal stresses, while normalizing involves heating the ma...read more
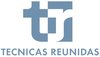
Asked in Técnicas Reunidas

Q. How do you design underground concrete structures, and what checks are necessary?
Designing underground concrete structures requires careful planning and consideration of various factors.
Determine the purpose and function of the structure
Consider the soil conditions and water table
Select appropriate materials and reinforcement
Ensure proper drainage and waterproofing
Perform structural analysis and testing
Follow local building codes and regulations
Regularly inspect and maintain the structure
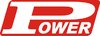
Asked in Chheda Electricals and Electronics

Q. What is GD&T , How we can measure and through which instruments
GD&T stands for Geometric Dimensioning and Tolerancing. It is a system used to define and communicate engineering tolerances.
GD&T is a symbolic language used to specify the dimensions, form, orientation, and location of features on a part.
It allows engineers to accurately communicate design requirements and ensure proper fit, function, and interchangeability of parts.
GD&T uses various symbols, such as position, concentricity, flatness, and perpendicularity, to define toleranc...read more
Asked in Ksd Technologies

Q. Tell us about the welded assembly?. and what are the factors consider while selecting the weld size for the particular type of joint.
A welded assembly is a joining method where two or more metal pieces are fused together using heat and pressure.
Factors to consider when selecting weld size include material thickness, joint type, and required strength
The size of the weld should be sufficient to provide the necessary strength without excess material
Consideration should also be given to the welding process being used and any applicable codes or standards
Examples of weld sizes include fillet welds, groove welds...read more
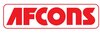
Asked in Afcons Infrastructure

Q. What peak factors are used for distribution design?
Peak factors are used in distribution design to account for peak loads and ensure safe and efficient operation.
Peak factors are used to determine the maximum load that a distribution system can handle.
They take into consideration factors such as diversity of loads, power factor, and future growth.
For example, a peak factor of 1.5 means that the system should be designed to handle 50% more than the average load.
Peak factors vary depending on the type of distribution system and...read more
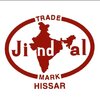
Asked in Jindal Industries Private Limited

Q. What are the necessities of designing, even if you can create parts without drawings?
Designing is essential for ensuring parts fit together correctly, meet performance requirements, and can be manufactured efficiently.
Designing helps ensure parts fit together correctly and function as intended
Designing allows for optimization of part performance and efficiency
Designing helps identify potential issues before production, saving time and resources
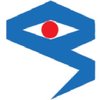
Asked in Vision Mechatronics Private Limited

Q. How do you determine the appropriate thickness for sheet metal?
The appropriate thickness for sheet metal is determined based on factors like material type, application, structural requirements, and cost.
Consider the material type and its properties such as strength and flexibility
Evaluate the application of the sheet metal, whether it will be used for structural support or aesthetic purposes
Determine the structural requirements such as load-bearing capacity and resistance to deformation
Take into account cost considerations, as thicker sh...read more
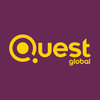
Asked in Quest Global

Q. Materials grades,which area working in rolling stock, PDM, VPM, CATIA, STACKUP ANALYSIS, CDR, DDR, PDR etc
I have experience working with materials grades in rolling stock and using various software tools such as PDM, VPM, CATIA, and performing stackup analysis, CDR, DDR, and PDR.
Experience with materials grades in rolling stock
Proficient in PDM and VPM software
Skilled in using CATIA for design engineering
Expertise in performing stackup analysis
Familiarity with CDR, DDR, and PDR processes
Asked in Hydrodyne Industries

Q. What is relief valve, check valve and flow control valve?
Relief valve, check valve and flow control valve are types of valves used in fluid systems.
Relief valve is used to release excess pressure in a system to prevent damage or failure.
Check valve allows fluid to flow in one direction only, preventing backflow and protecting equipment.
Flow control valve regulates the flow rate of fluid in a system, maintaining a constant flow rate or adjusting it as needed.
Examples of relief valves include safety valves and pressure relief valves....read more
Asked in Ksd Technologies

Q. What is the importance of spring back effect in sheet metal design. How we will defining the bend radius for the any sheet metal part.
Spring back effect in sheet metal design is important for achieving accurate dimensions and shapes. Bend radius is defined based on material properties and manufacturing processes.
Spring back effect refers to the tendency of a metal to return to its original shape after being bent or formed.
It is important to account for spring back in sheet metal design to ensure the final part meets dimensional requirements.
Bend radius is defined as the inside radius of a bend in a sheet me...read more
Asked in Bbm Acoustic India

Q. What is the difference between continuous and continual improvement?
Continuous improvement is ongoing and focuses on small, incremental changes, while continual improvement is periodic and focuses on larger, more significant changes.
Continuous improvement involves making small, incremental changes to processes or products on an ongoing basis.
Continual improvement involves periodic reviews of processes or products to identify larger, more significant changes that can be made.
Continuous improvement is often associated with Lean or Six Sigma met...read more
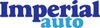
Asked in Imperial Auto Industries

Q. What do you know about the heat treatment of metals and rubbers?
Heat treatment of metals and rubbers involves controlled heating and cooling processes to alter their properties.
Heat treatment is used to improve the mechanical properties of metals by changing their microstructure.
Common heat treatment processes for metals include annealing, quenching, tempering, and normalizing.
Rubbers can also undergo heat treatment processes like vulcanization to improve their strength and elasticity.
Heat treatment can enhance the hardness, toughness, du...read more
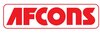
Asked in Afcons Infrastructure

Q. What is the design period for a distribution system and headwork?
The design period for distribution system and headwork refers to the expected lifespan or duration for which the system is designed to function effectively.
The design period is determined based on factors such as expected growth, technological advancements, and maintenance requirements.
It is important to consider the long-term needs and goals of the distribution system and headwork when determining the design period.
For example, if the distribution system is expected to serve...read more
Asked in Hydrodyne Industries

Q. How do you determine the bore of a cylinder given the pressure and load?
Bore of cylinder is decided based on pressure and load given.
Calculate the force required to move the load
Determine the pressure required to generate the force
Select a cylinder with a bore size that can generate the required pressure
Consider safety factors and application requirements
Consult industry standards and guidelines
Example: For a load of 1000 N and pressure of 10 bar, bore size can be calculated using formula: bore = (4 x force)/(pi x pressure)
Example: Safety factor ...read more
Interview Questions of Similar Designations
Interview Experiences of Popular Companies
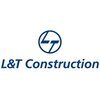
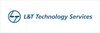
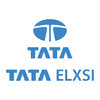
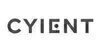
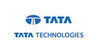
Top Interview Questions for Senior Design Engineer Related Skills
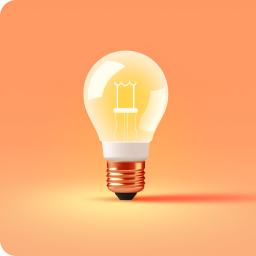
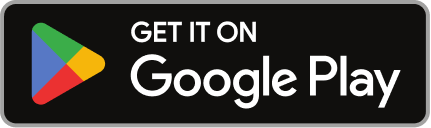
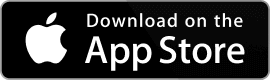
Reviews
Interviews
Salaries
Users
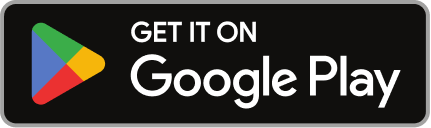
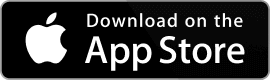