Safety Manager
80+ Safety Manager Interview Questions and Answers
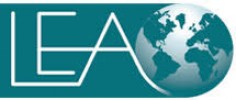
Asked in Lea Associates South Asia

Q. What types of legal documents shall be prepared by you?
As a Safety Manager, I would be responsible for preparing various legal documents to ensure compliance and promote safety in the workplace.
Safety policies and procedures
Incident reports and investigation documents
Training materials and manuals
Safety audits and inspection reports
Emergency response plans
Safety permits and licenses
Risk assessments and hazard identification documents
Asked in Hindustan Fluorocarbons

Q. How do you repair the inside of a pressure vessel if welding and cutting are involved?
Repairing inside pressure vessel with welding and cutting involved requires proper planning and safety measures.
Ensure proper ventilation and air monitoring before starting any work
Use appropriate personal protective equipment (PPE) such as respirators, gloves, and goggles
Follow proper welding and cutting procedures to prevent any damage to the vessel
Perform non-destructive testing (NDT) to ensure the integrity of the repair
Have a qualified inspector verify the repair before ...read more
Safety Manager Interview Questions and Answers for Freshers
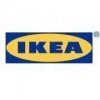
Asked in IKEA

Q. What welfare facilities should be provided at a construction site?
Welfare facilities at a construction site include restrooms, drinking water, first aid, and shelter.
Restrooms: Adequate number of clean and well-maintained toilets should be provided.
Drinking water: Accessible clean drinking water should be available for workers.
First aid: A designated area with necessary first aid supplies and trained personnel should be present.
Shelter: Adequate shelter should be provided to protect workers from extreme weather conditions.
Waste disposal: Pr...read more
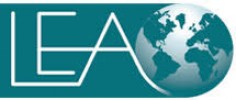
Asked in Lea Associates South Asia

Q. How can housekeeping be improved in congested and busy traffic zones?
Improving housekeeping in congestion and busy traffic zones requires effective planning, clear communication, and regular maintenance.
Develop a comprehensive housekeeping plan that includes regular cleaning schedules and designated areas for waste disposal.
Implement clear signage and markings to indicate designated walkways and traffic flow patterns.
Provide adequate training and education to employees on the importance of housekeeping and safe practices in congested areas.
Reg...read more
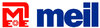
Asked in Megha Engineering & Infrastructures

Q. How can various types of accidents be prevented?
Preventing accidents requires a combination of training, safety protocols, and hazard identification.
Develop and implement safety protocols and procedures
Provide regular safety training to employees
Conduct regular hazard assessments and implement controls
Encourage reporting of near-misses and incidents for continuous improvement
Ensure equipment and machinery is properly maintained
Promote a culture of safety and accountability
Provide personal protective equipment (PPE) where n...read more
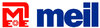
Asked in Megha Engineering & Infrastructures

Q. What are the key steps and skills in safety management?
The key skills in safety management include risk assessment, hazard identification, incident investigation, training, and emergency preparedness.
Risk assessment: Identifying potential risks and evaluating their likelihood and impact.
Hazard identification: Recognizing and assessing hazards in the workplace.
Incident investigation: Conducting thorough investigations to determine the causes of accidents or near misses.
Training: Providing comprehensive safety training to employees...read more
Safety Manager Jobs
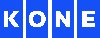
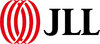
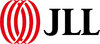
Asked in Hindustan Fluorocarbons

Q. If all safety measures fail and a gas leak occurs, similar to the Bhopal gas disaster, what would be your immediate course of action?
In the event of a gas leak similar to the Bhopal gas disaster, immediate action must be taken to mitigate the situation and ensure the safety of individuals.
Activate emergency response protocols
Evacuate affected areas
Provide medical assistance to those exposed to the gas
Contain and control the leak
Investigate the cause of the leak and take measures to prevent future incidents
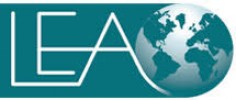
Asked in Lea Associates South Asia

Q. Do you have any initiatives or innovative ideas for a proactive safety culture?
Yes, I have several innovative ideas for promoting a proactive safety culture.
Implementing a safety rewards program to incentivize safe behavior
Developing a safety training program that focuses on proactive hazard identification
Creating a safety committee that regularly reviews and updates safety policies and procedures
Utilizing technology such as wearables or sensors to monitor and prevent potential safety hazards
Encouraging open communication and feedback channels for emplo...read more
Share interview questions and help millions of jobseekers 🌟
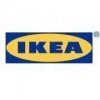
Asked in IKEA

Q. Is a near miss report a part of a leading indicator or a lagging indicator?
Near miss report is a leading indicator.
Near miss reports are proactive measures taken to prevent accidents or incidents.
They provide valuable information about potential hazards and risks in the workplace.
By analyzing near miss reports, safety managers can identify trends and implement preventive measures.
Near miss reports help in creating a culture of safety and continuous improvement.
Examples of near miss reports include observations of unsafe conditions, equipment malfunc...read more
Asked in Hindustan Fluorocarbons

Q. How can a zero-accident goal be achieved?
To achieve zero accidents goal, implement a comprehensive safety program, provide training and education, enforce safety policies, conduct regular inspections, and promote a culture of safety.
Implement a comprehensive safety program that includes clear safety policies and procedures.
Provide training and education to employees on safety practices and procedures.
Enforce safety policies consistently and hold employees accountable for their actions.
Conduct regular inspections and...read more
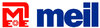
Asked in Megha Engineering & Infrastructures

Q. How do you calculate accident and incident rates?
Accident and incident rates are calculated by dividing the number of incidents by the total number of hours worked.
Collect data on the number of accidents and incidents that occurred during a specific time period.
Determine the total number of hours worked during that same time period.
Divide the number of incidents by the total number of hours worked to get the incident rate.
Multiply the incident rate by 200,000 to get the incident rate per 100 full-time employees.
Compare the ...read more
Asked in Hindustan Fluorocarbons

Q. How do you safely repair pressure vessels?
Pressure vessels can be safely repaired by following proper inspection, assessment, and repair procedures.
Inspect the pressure vessel thoroughly to identify any damage or defects.
Assess the severity of the damage and determine if repair is feasible or if replacement is necessary.
Follow industry standards and codes for repairing pressure vessels.
Ensure proper welding techniques and materials are used for repairs.
Perform pressure testing after repairs to ensure the vessel is sa...read more
Asked in Ardee Engineering Company

Q. What are the mandatory PPEs to be used to start work on the site?
The mandatory PPEs to start work on a site include hard hats, safety glasses, high-visibility vests, steel-toed boots, and ear protection.
Hard hats are essential to protect the head from falling objects and potential head injuries.
Safety glasses protect the eyes from flying debris, chemicals, and other hazards.
High-visibility vests ensure workers are easily seen and identified on the site.
Steel-toed boots provide foot protection against heavy objects and potential crushing in...read more
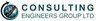
Asked in Consulting Engineers Group

Q. What safety measures should be taken when working at height?
Safety measures for working at height include fall protection equipment, proper training, regular inspections, and hazard identification.
Use fall protection equipment such as harnesses, lanyards, and safety nets.
Ensure workers are properly trained on working at height procedures and equipment usage.
Regularly inspect and maintain all equipment used for working at height.
Identify and eliminate or control hazards that may cause falls or accidents.
Implement safety protocols and p...read more
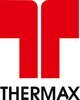
Asked in Thermax Limited

Q. What are lead and lag indicators in terms of safety, and can you explain them briefly?
Lead and lag indicators are used in safety management to measure proactive and reactive safety performance.
Lead indicators are proactive measures that help predict and prevent accidents, such as safety training completion rates or safety inspections.
Lag indicators are reactive measures that track past incidents, such as injury rates or near-miss reports.
Lead indicators focus on preventing accidents before they occur, while lag indicators focus on analyzing past incidents to i...read more
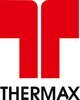
Asked in Thermax Limited

Q. What does Annexure 8 cover regarding the safety regulations or guidelines of Tata Steel?
Annexure 8 of Tata Steel's safety regulations outlines specific guidelines for working at heights.
Annexure 8 provides detailed instructions on the use of fall protection equipment.
It includes requirements for conducting risk assessments before working at heights.
The annexure also covers training requirements for employees working at heights.
It outlines procedures for emergency response in case of falls or accidents.
Compliance with Annexure 8 is mandatory for all employees wor...read more
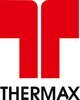
Asked in Thermax Limited

Q. What is Annexure 9 concerning the safety regulations or guidelines of Tata Steel?
Annexure 9 of Tata Steel contains safety guidelines for contractors working on Tata Steel premises.
Annexure 9 outlines specific safety requirements and procedures that contractors must adhere to while working on Tata Steel sites.
It covers aspects such as personal protective equipment (PPE), hazard communication, emergency procedures, and safety training.
Contractors are expected to follow Annexure 9 to ensure a safe working environment for themselves and Tata Steel employees.
F...read more
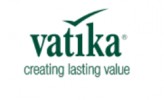
Asked in Vatika Group

Q. How much load can a mobile crane handle?
The load capacity of a mobile crane depends on various factors such as the crane's specifications, boom length, and load radius.
The load capacity of a mobile crane is typically specified by the manufacturer and can be found in the crane's documentation.
Factors that affect the load capacity include the crane's boom length, load radius, and the angle at which the load is lifted.
The load capacity should never be exceeded to ensure safe operation and prevent accidents.
It is impor...read more
Asked in Volmet

Q. What are the Lifting procedure, Lock Out Tag Out system, how to maintain safe environment on factory site.
Lifting procedures, Lock Out Tag Out system, and maintaining a safe environment on a factory site are crucial for ensuring workplace safety.
Lifting procedures involve proper training on how to lift heavy objects safely to prevent injuries.
Lock Out Tag Out system is a safety procedure used to ensure that dangerous machines are properly shut off and not started up again prior to the completion of maintenance or servicing work.
Maintaining a safe environment on a factory site inc...read more
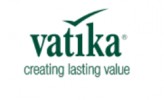
Asked in Vatika Group

Q. What steps should be taken before operating a mobile crane?
Before putting the mobile crane into use, it is important to perform a pre-operational inspection and ensure proper setup.
Perform a pre-operational inspection to check for any damages or malfunctions.
Ensure that the crane is set up on a stable and level ground.
Verify that all safety devices and controls are in working order.
Check the load capacity and ensure it is within the crane's limits.
Inspect the lifting gear and attachments for any defects or wear.
Review the site condit...read more
Asked in Volmet

Q. What are the safety procedures related to the maintenance work of paper machines?
Safety procedures for maintenance work on paper machines include lockout/tagout, proper training, use of PPE, and regular inspections.
Implement lockout/tagout procedures to ensure machines are properly shut off and cannot be restarted during maintenance.
Provide thorough training to maintenance workers on safe work practices and potential hazards associated with paper machines.
Require the use of appropriate personal protective equipment (PPE) such as gloves, goggles, and ear p...read more
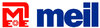
Asked in Megha Engineering & Infrastructures

Q. Various types of hazards present in Tunnels
Tunnels pose various hazards such as poor air quality, fire, flooding, and collapse.
Poor air quality due to exhaust fumes, dust, and lack of ventilation
Fire hazards due to electrical equipment, flammable materials, and smoking
Flooding due to water leaks or natural disasters
Collapse due to unstable ground or structural issues
Other hazards include noise, vibration, and limited visibility
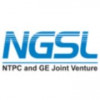
Asked in NTPC GE Power Services

Q. What is BOCW?
BOCW stands for Building and Other Construction Workers.
BOCW is a term used in the construction industry to refer to workers involved in building and other construction activities.
It includes workers engaged in construction, repair, alteration, demolition, and maintenance of buildings, roads, bridges, etc.
BOCW also covers workers involved in excavation, scaffolding, painting, plumbing, electrical work, etc.
The BOCW Act provides for the welfare and safety of these workers, inc...read more
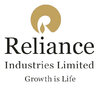
Asked in Reliance Industries

Q. What do Sections 18 and 19 of the Factory Act entail?
Sections 18 and 19 of the Factory Act focus on health and safety provisions for workers in industrial settings.
Section 18 mandates the provision of adequate ventilation in workspaces to ensure air quality.
Section 19 requires factories to maintain cleanliness and proper sanitation facilities for workers.
Example: Factories must provide clean drinking water and proper waste disposal systems.
Both sections aim to prevent occupational hazards and promote worker well-being.
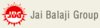
Asked in Jai Balaji Group

Q. What is the meaning of "Hira," and can you provide examples of its usage?
HIRA stands for Hazard Identification and Risk Assessment, crucial for workplace safety management.
HIRA is a systematic process to identify hazards in the workplace.
It involves assessing risks associated with identified hazards.
Example: Conducting HIRA for a construction site to identify fall risks.
HIRA helps in implementing control measures to mitigate risks.
Regular HIRA updates are essential as workplace conditions change.
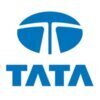
Asked in Tata Steel Downstream Products

Q. What are the risks in a confined space, and what gases are dangerous there?
Confined spaces pose risks due to limited ventilation, leading to hazardous gas accumulation and potential health hazards.
Oxygen deficiency: Levels below 19.5% can cause unconsciousness or death.
Toxic gases: Carbon monoxide (CO) can be lethal even in small amounts.
Flammable gases: Methane can lead to explosions in confined spaces.
Asphyxiants: Nitrogen can displace oxygen, leading to suffocation.
Corrosive gases: Hydrogen sulfide (H2S) can cause respiratory failure.
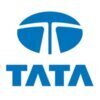
Asked in Tata Steel Downstream Products

Q. What is the difference between an on-site emergency plan and an emergency evacuation plan?
On-site emergency plans address immediate threats, while evacuation plans focus on safe exit procedures during emergencies.
On-site emergency plans include procedures for various emergencies like fires, chemical spills, or medical emergencies.
Emergency evacuation plans specifically outline the routes and methods for safely evacuating personnel from a building.
For example, an on-site emergency plan may include first aid protocols, while an evacuation plan details the nearest ex...read more
Asked in Hindustan Fluorocarbons

Q. Would you be willing to accept a lower position?
I appreciate the offer, but I believe my skills and experience align with a managerial role in safety.
My background includes extensive experience in safety management, which is crucial for the role.
I have successfully led safety initiatives that reduced incidents by 30% in my previous position.
Accepting a lower position may not utilize my full potential and could hinder my career growth.
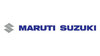
Asked in Maruti Suzuki

Q. Can you describe your experience with hazard identification?
I have extensive experience in hazard identification through conducting regular workplace inspections, analyzing incident reports, and implementing safety protocols.
Conducting regular workplace inspections to identify potential hazards
Analyzing incident reports to determine root causes of accidents
Implementing safety protocols to mitigate identified hazards
Training employees on hazard recognition and reporting procedures
Asked in Trayo Construction

Q. How do you manage safety rules and awareness at a work site?
Effective safety management involves clear communication, training, and continuous monitoring to ensure a safe work environment.
Regular Training Sessions: Conduct safety training workshops to educate employees about safety protocols and emergency procedures. For example, quarterly fire drills.
Clear Communication: Use signage and regular meetings to communicate safety rules. For instance, post safety reminders in common areas.
Safety Audits: Perform regular safety audits to ide...read more
Interview Questions of Similar Designations
Interview Experiences of Popular Companies
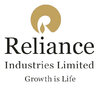
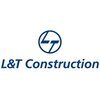
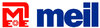
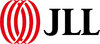
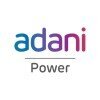
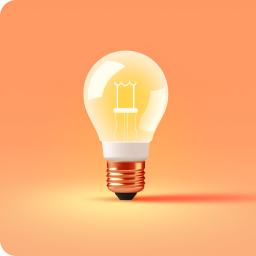
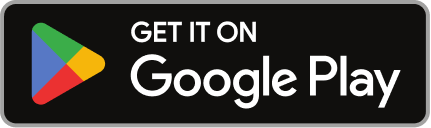
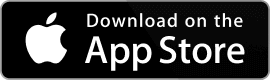
Reviews
Interviews
Salaries
Users
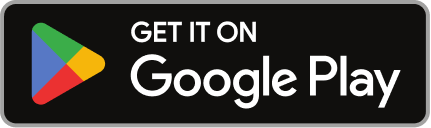
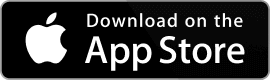