Instrumentation Incharge
Instrumentation Incharge Interview Questions and Answers
Asked in Dev Priya Product

Q. How do you calculate the linear load of a hydraulic press?
Linear load of hydraulic press can be calculated by dividing the force applied by the area of the piston.
Divide the force applied by the area of the piston to get the linear load.
Linear load is measured in units of force per unit of length.
The formula for calculating linear load is: Force / Piston Area.
Linear load is an important parameter to monitor in hydraulic presses to ensure safe and efficient operation.
Asked in Dev Priya Product

Q. What is the proportional term in PID control, how does it work, and what are its applications?
Proportional is a term used in PID control. It determines the output based on the error between the setpoint and the process variable.
Proportional gain is a constant that determines the output change for a given error.
It is directly proportional to the error signal.
A higher proportional gain results in a faster response but can lead to overshoot and instability.
Proportional control is used in applications such as temperature control, level control, and flow control.
Asked in Dev Priya Product

Q. What should be checked if the pressure gauge load is hunting?
We check for any fluctuations or oscillations in the pressure gauge reading.
Check for any sudden changes in the pressure reading
Observe if the pressure reading is oscillating
Ensure that the pressure reading is stable
Check for any leaks or blockages in the system
Verify that the pressure gauge is calibrated correctly
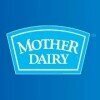
Asked in Mother Dairy Fruit & Vegetable

Q. Justify some plc and instrumentation engineering and all type of sensors, weighing system.
PLC and instrumentation engineering play a crucial role in automation and control systems, while sensors and weighing systems provide accurate data for monitoring and decision-making.
PLC (Programmable Logic Controller) systems are used to automate industrial processes, improving efficiency and reliability.
Instrumentation engineering involves designing and implementing control systems for various applications, such as temperature, pressure, and flow control.
Sensors are essenti...read more
Asked in Dev Priya Product

Q. What are the advantages of better PID tuning?
Better PID tuning leads to improved control performance and stability.
Improved control performance and stability
Reduced overshoot and settling time
Better disturbance rejection
Increased process efficiency and productivity
Optimized energy consumption
Prevention of equipment damage and wear
Enhanced safety and reliability
Examples: better temperature control in chemical reactors, improved speed control in motors
Asked in Dev Priya Product

Q. What is the meaning of PID tuning?
PID tuning is the process of adjusting the parameters of a proportional-integral-derivative controller to achieve optimal performance.
PID stands for proportional-integral-derivative
It is used to control a system's output based on its error signal
Tuning involves adjusting the controller's parameters to achieve desired response
Optimal tuning results in stable and responsive control of the system
Examples include tuning the PID controller of a temperature control system or a robo...read more
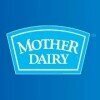
Asked in Mother Dairy Fruit & Vegetable

Q. All type pn system and automation
All type pn system and automation refers to various types of pneumatic systems and automation technologies used in industrial settings.
Pneumatic systems use compressed air to control mechanical motion.
Automation technologies include PLCs, sensors, actuators, and control systems.
Examples of pneumatic systems include pneumatic cylinders, valves, and air compressors.
Examples of automation technologies include programmable logic controllers (PLCs) and industrial robots.
Interview Questions of Similar Designations
Interview Experiences of Popular Companies
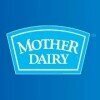


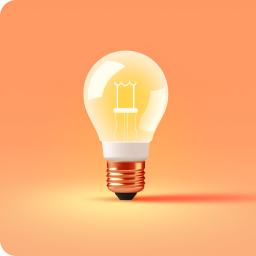
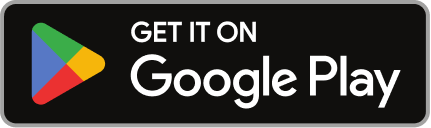
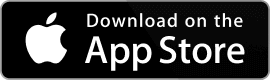
Reviews
Interviews
Salaries
Users
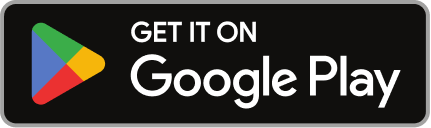
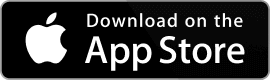