CAE Engineer
70+ CAE Engineer Interview Questions and Answers
Asked in Dheya Engineering Technologies

Q. Two different materials with the same cross-section are subjected to equal tensile forces. Which material will deflect more?
The material with lower Young's modulus will deflect more.
Young's modulus determines the stiffness of a material.
The material with lower Young's modulus will have more deflection under the same force.
For example, rubber has a lower Young's modulus than steel and will deflect more under the same force.
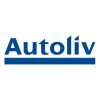
Asked in Autoliv

Q. What is meant by density? And how you calculate the weight of any object without weighing it directly?
Density is the measure of mass per unit volume. Weight can be calculated using density and volume.
Density is calculated by dividing the mass of an object by its volume.
Weight can be calculated using the formula: weight = density x volume x gravity
Gravity is a constant value of 9.81 m/s^2 on Earth.
For example, the weight of a 1 cubic meter block of iron with a density of 7.87 g/cm^3 would be 77,910 N.
CAE Engineer Interview Questions and Answers for Freshers
Asked in Dheya Engineering Technologies

Q. How does stiffness vary, and what factors affect it?
Stiffness varies with material, geometry, and loading conditions.
Stiffness is the ability of a material to resist deformation under load.
Materials with higher Young's modulus have higher stiffness.
Stiffness also depends on the geometry of the structure.
For example, a thicker beam will be stiffer than a thinner beam.
Loading conditions such as the magnitude and direction of the load also affect stiffness.
For instance, a beam will be stiffer when loaded in compression than in be...read more
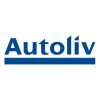
Asked in Autoliv

Q. What is the difference between frequency and vibration?
Frequency is the number of vibrations per unit of time, while vibration is the oscillation or movement back and forth of an object.
Frequency refers to the rate at which an object vibrates or oscillates.
Vibration is the physical movement or oscillation of an object.
Frequency is measured in hertz (Hz), while vibration is measured in amplitude or displacement.
Frequency can be constant or varying, while vibration can have different patterns and amplitudes.
For example, a guitar st...read more
Asked in Dheya Engineering Technologies

Q. How do you determine the deflection of a material or component?
Deflection of a material/component can be determined by analyzing its stress and strain under a load.
Calculate the stress and strain of the material/component
Use the material's Young's modulus to determine its stiffness
Apply the load and calculate the resulting deflection using the stiffness and stress/strain
Consider any external factors that may affect the deflection, such as temperature or moisture
Use simulation software to model the deflection and verify the results
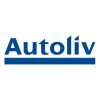
Asked in Autoliv

Q. What do you mean by atmospheric pressure? And how it's very with height
Atmospheric pressure refers to the force exerted by the weight of the air in the Earth's atmosphere.
Atmospheric pressure is the pressure exerted by the weight of the air above a given point on the Earth's surface.
It is caused by the gravitational attraction of the Earth on the air molecules.
At sea level, the average atmospheric pressure is about 1013.25 millibars or 14.7 pounds per square inch (psi).
As you go higher in the atmosphere, the air becomes less dense and the atmosp...read more
CAE Engineer Jobs
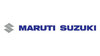
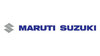
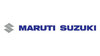
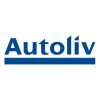
Asked in Autoliv

Q. What is meant by mechanical vibration?
Mechanical vibration refers to the oscillation or movement of an object or structure due to an applied force or disturbance.
Mechanical vibration is the back-and-forth motion of an object or structure.
It occurs when an external force or disturbance is applied to the object.
Vibration can be caused by various factors such as machinery, engines, earthquakes, or even human activities.
It can have both beneficial and detrimental effects depending on the context.
Examples of mechanica...read more
Asked in Hexdof Engineering Services

Q. What components have you worked on before?
I have worked on various components including engine blocks, suspension systems, and body structures.
Designed and analyzed engine blocks for durability and performance
Optimized suspension systems for ride comfort and handling
Performed crash simulations on body structures to ensure safety
Conducted thermal analysis on exhaust systems to prevent overheating
Collaborated with cross-functional teams to integrate components into vehicle designs
Share interview questions and help millions of jobseekers š
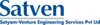
Asked in Satyam Venture Engineering Services

Q. 1.What is stress? 2.Bending moment? 3.Quality criteria in FEA? 4.What is tet collapse What is test correlation 5.Process of FEA modelling 6.Types of elements in Nastran, dyna?
Answers to questions related to CAE engineering including stress, bending moment, quality criteria in FEA, tet collapse, test correlation, FEA modelling process, and types of elements in Nastran and Dyna.
Stress is the force per unit area that a material experiences when subjected to an external load.
Bending moment is the moment that causes a beam to bend.
Quality criteria in FEA include accuracy, convergence, and stability.
Tet collapse is a phenomenon where tetrahedral element...read more
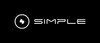
Asked in Simple Energy

Q. Can you provide a brief explanation of the stress-strain curve of elastic materials?
Stress-strain curve of elastic materials shows relationship between applied stress and resulting strain.
The curve typically consists of linear elastic region, yield point, plastic deformation, and ultimate failure.
Elastic materials return to their original shape after stress is removed within the linear region.
Yield point marks the transition from elastic to plastic deformation.
Plastic deformation is permanent and leads to structural changes in the material.
Ultimate failure o...read more
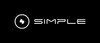
Asked in Simple Energy

Q. What are the plastic material grades used in the automotive industry?
Plastic material grades commonly used in automotive industry.
Polypropylene (PP)
Polyethylene (PE)
Acrylonitrile Butadiene Styrene (ABS)
Polyamide (PA)
Polycarbonate (PC)
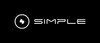
Asked in Simple Energy

Q. What are the quality criteria for 2D and 3D meshing, and what are the corresponding values?
Quality criteria for 2D and 3D meshing include element shape, aspect ratio, skewness, and element size.
Element shape should be close to regular shapes like triangles or quadrilaterals for 2D meshing and tetrahedra or hexahedra for 3D meshing.
Aspect ratio should be close to 1 for both 2D and 3D meshing to avoid distorted elements.
Skewness should be minimized to ensure better accuracy in simulation results.
Element size should be appropriate for capturing the geometry details an...read more
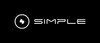
Asked in Simple Energy

Q. What are the various types of transmission systems used in two-wheelers?
Various types of transmission systems used in two-wheelers include manual, automatic, semi-automatic, and CVT.
Manual transmission: Requires the rider to manually shift gears using a clutch and gear lever.
Automatic transmission: Shifts gears automatically without the need for manual intervention.
Semi-automatic transmission: Allows the rider to manually shift gears without using a clutch.
CVT (Continuously Variable Transmission): Offers seamless gear ratio changes for smooth acc...read more
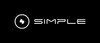
Asked in Simple Energy

Q. What materials are commonly used in the parts of electric scooters?
Common materials used in electric scooters include aluminum, steel, plastic, and rubber.
Aluminum: Lightweight and durable, commonly used for scooter frames and components.
Steel: Provides strength and stability, often used in structural parts like handlebars and forks.
Plastic: Used for body panels, covers, and other non-structural components.
Rubber: Found in tires, grips, and suspension components for traction and vibration dampening.
Asked in Dheya Engineering Technologies

Q. What is stress, poisons ratio, endurance limit?
Stress is the force per unit area, Poisson's ratio is the ratio of lateral to axial strain, and endurance limit is the maximum stress a material can withstand without breaking after a certain number of cycles.
Stress is the measure of the internal forces acting within a material, which can cause deformation or failure.
Poisson's ratio is a measure of a material's ability to deform in response to an applied force, and is defined as the ratio of lateral strain to axial strain.
End...read more
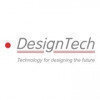
Asked in DesignTech Systems

Q. What is the difference between ductile and brittle materials?
Ductile materials can undergo significant plastic deformation before failure, while brittle materials fail without significant deformation.
Ductile materials can be stretched into wires or hammered into thin sheets without breaking.
Brittle materials break with little or no plastic deformation.
Ductile materials have high toughness and are able to absorb a large amount of energy before fracturing.
Examples of ductile materials include metals like copper and aluminum.
Examples of b...read more
Asked in Dheya Engineering Technologies

Q. What is Young's modulus of steel?
Young's modulus of steel is around 200 GPa.
Young's modulus is a measure of the stiffness of a material.
It is defined as the ratio of stress to strain within the elastic limit.
Steel has a high Young's modulus, making it a strong and rigid material.
The value of Young's modulus for steel can vary depending on the specific type and grade of steel.
For example, the Young's modulus of mild steel is around 200 GPa, while for high-strength steel it can be up to 300 GPa.
Asked in Hexdof Engineering Services

Q. How do you use Hypermesh tools and shortcuts?
Hypermesh tools & shortcuts are used for meshing and pre-processing tasks in CAE. They help in saving time and improving efficiency.
Use Ctrl + M to open the mesh panel
Use Ctrl + Shift + M to open the model panel
Use Ctrl + G to group selected components
Use Ctrl + Shift + G to ungroup selected components
Use F12 to toggle between graphics and text view
Use Ctrl + E to edit the selected component
Use Ctrl + Shift + E to edit the selected property
Use Ctrl + D to duplicate the select...read more
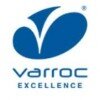
Asked in Varroc Group

Q. What is process capability, and what is the difference between Pp and Cp?
Process capability is the ability of a process to produce output within specification limits. PP is for initial process setup and CP is for ongoing process control.
Process capability is a statistical measure of the ability of a process to produce output within specification limits.
PP (Process Performance) is used for initial process setup and measures the process's ability to meet specifications.
CP (Process Capability) is used for ongoing process control and measures the proc...read more
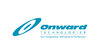
Asked in Onward Technologies Inc

Q. Meshing with the given quality criteria
Meshing with quality criteria involves creating a finite element mesh that meets specific requirements.
Understand the quality criteria and how it affects the simulation results
Choose appropriate meshing techniques and element types
Use mesh refinement to improve accuracy in critical areas
Perform mesh sensitivity analysis to ensure mesh independence
Validate the mesh with experimental or analytical data
Optimize the mesh for computational efficiency
Asked in Hexdof Engineering Services

Q. What is Shell Meshing in Hypermesh?
Shell meshing is a technique used in Hypermesh to create a mesh of thin-walled structures.
Shell meshing is used for structures that have a thickness much smaller than their other dimensions.
It involves creating a mesh of the mid-surface of the structure and then extruding it to create a 3D mesh.
Shell meshing is commonly used in the aerospace and automotive industries for components such as panels and shells.
It can help reduce the computational time and memory required for sim...read more
Asked in Hinode Technologies

Q. Expain your UG project? What tools did you used?
My UG project focused on optimizing airflow in automotive engines using computational fluid dynamics. I used ANSYS Fluent and MATLAB for simulations.
Studied airflow patterns in automotive engines
Utilized computational fluid dynamics for simulations
Optimized engine performance using ANSYS Fluent and MATLAB
Asked in Hinode Technologies

Q. How comfortable are you with the software?
I am very comfortable with the software and have extensive experience using it.
I have been using the software for several years and have mastered its features and capabilities.
I have completed numerous projects using the software, showcasing my proficiency.
I regularly attend training sessions and workshops to stay updated on the latest software updates and enhancements.
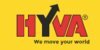
Asked in Hyva

Q. What is Pascal's law?
Pascal's law states that pressure applied to a fluid in a confined space is transmitted equally in all directions.
Pascal's law is a fundamental principle in fluid mechanics.
It states that when pressure is applied to a fluid in a closed container, the pressure is transmitted equally in all directions.
This means that if you apply pressure to one part of a fluid, the entire fluid will experience the same increase in pressure.
Pascal's law is the basis for many hydraulic systems a...read more
Asked in Quantum Point

Q. How strong are you in the basic concepts of structural mechanics?
I have a strong understanding of basic concepts in structural mechanics.
I have a solid foundation in statics and dynamics, including concepts such as equilibrium, forces, moments, and motion.
I am familiar with stress and strain analysis, including concepts like Hooke's Law and material properties.
I understand the principles of structural analysis, including methods like finite element analysis (FEA) and boundary conditions.
I am knowledgeable about structural behavior under di...read more
Asked in ELEATION

Q. What are the advantages and limitations of CAD and CAM software, and how do they simplify the work process?
CAD and CAM software enhance design and manufacturing efficiency but have limitations in flexibility and cost.
Increased accuracy: CAD software allows for precise designs, reducing errors in the manufacturing process.
Time-saving: CAM automates machining processes, significantly speeding up production times.
Enhanced collaboration: CAD files can be easily shared among team members, facilitating better communication.
Cost efficiency: Reduces material waste through optimized design...read more
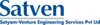
Asked in Satyam Venture Engineering Services

Q. What is elasticity, and explain the stress-strain curve?
Elasticity is the ability of a material to return to its original shape after being deformed. Stress and strain curve shows the relationship between stress and strain.
Elasticity is a property of materials that allows them to return to their original shape after being stretched or compressed.
Stress is the force applied to a material per unit area, while strain is the resulting deformation of the material.
The stress-strain curve shows the relationship between stress and strain ...read more
Asked in GNS Engineering India Pvt Ltd

Q. Are you comfortable with a 27-month service agreement, a salary of 14 LPA in hand plus 2.2 LPA, and working Saturdays for one year?
Accepting a 27 month service agreement with 14 in hand and 2.2 lpa, including Saturday working for one year.
Consider the overall compensation package including salary and benefits
Evaluate the long-term career growth opportunities with the company
Assess the impact of Saturday working on work-life balance
Negotiate for potential changes in the terms if necessary
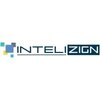
Asked in Intelizign Lifecycle Services

Q. What is Degree of Freedom?
Degree of Freedom refers to the number of independent parameters required to define the position or configuration of a system.
It is a measure of the number of ways a system can move or change.
In engineering, it is used to describe the number of independent variables that can be changed to alter the behavior of a system.
For example, a rigid body in three-dimensional space has six degrees of freedom: three for translation and three for rotation.
In CAE, degree of freedom is used...read more
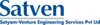
Asked in Satyam Venture Engineering Services

Q. How do you create spot welds and bolts in ANSA?
Spot welds and bolts can be created in ANSA using various tools and methods.
For spot welds, use the Spot Weld tool and select the two surfaces to be welded together.
For bolts, use the Bolt tool and select the two surfaces to be bolted together. Specify the bolt type, size, and other parameters.
ANSA also provides options to create spot welds and bolts automatically based on predefined rules and criteria.
Ensure that the spot welds and bolts are placed correctly and in the appro...read more
Interview Questions of Similar Designations
Interview Experiences of Popular Companies
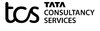
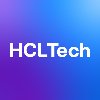
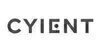
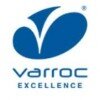
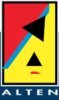
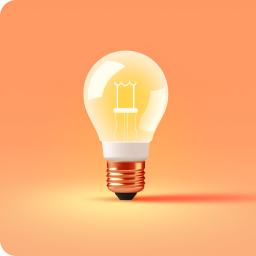
Calculate your in-hand salary
Confused about how your in-hand salary is calculated? Enter your annual salary (CTC) and get your in-hand salary
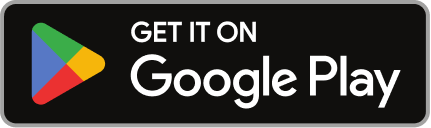
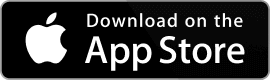
Reviews
Interviews
Salaries
Users
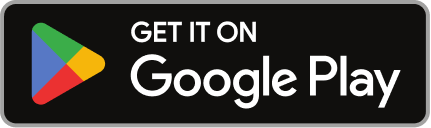
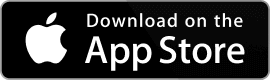