Team Leader-Quality Assurance/Quality Control
60+ Team Leader-Quality Assurance/Quality Control Interview Questions and Answers
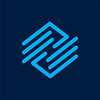
Asked in HGS

Q. Suppose you learn that you are going to face unplanned shrinkage and unplanned attrition. What would be your first step, and how would you manage it?
Assess the situation and take immediate action to prevent further damage. Implement corrective measures to address the issue.
Assess the extent of the unplanned shrinkage and attraction
Identify the root cause of the issue
Implement corrective measures to prevent further damage
Communicate the issue to relevant stakeholders
Monitor the situation to ensure the issue is resolved

Asked in Udaan

Q. What knowledge do you have about warehouse management?
Warehouse management involves overseeing the operations and processes within a warehouse to ensure efficient storage, handling, and distribution of goods.
Inventory management
Receiving and inspecting incoming shipments
Organizing and optimizing storage space
Implementing quality control measures
Coordinating with suppliers and logistics teams
Ensuring compliance with safety regulations
Implementing efficient picking and packing processes
Managing returns and exchanges
Utilizing wareh...read more
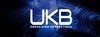
Asked in Ukb Electronics

Q. How do you monitor and balance manpower handling, CTQ, and CTF stages?
Manpower handling and CTQ/CTF stages are monitored and balanced through effective planning, communication, and continuous improvement.
Effective planning is necessary to ensure adequate manpower is available at each stage of the process
Communication between team members is crucial to identify and address any issues that may arise
Continuous improvement efforts should be implemented to optimize the balance between manpower and CTQ/CTF stages
Regular monitoring of key performance ...read more
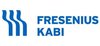
Asked in Fresenius Kabi

Q. Describe the sampling process for raw materials.
Sampling process in raw material involves selecting a representative portion of the material for testing.
Identify the lot or batch number of the raw material
Select a random sample from the lot or batch
Ensure the sample is representative of the entire lot or batch
Test the sample for quality and purity
Accept or reject the lot or batch based on the test results
Asked in LifePharma FZE

Q. How do you handle in-house preventive maintenance deviation handling for equipment?
Inhouse preventive maintenance deviation handling for equipment
Establish a standard operating procedure (SOP) for handling deviations
Document all deviations and investigate the root cause
Implement corrective actions to prevent future deviations
Ensure all equipment is properly maintained and calibrated
Train staff on the importance of following SOPs and reporting deviations
Regularly review and update the SOP as needed
Asked in LifePharma FZE

Q. Elaborate on an example of a market complaint and the respective corrective and preventative action taken.
Market complaint example and respective corrective and preventative action.
A customer complained about a faulty product.
Corrective action: Replace the faulty product and apologize to the customer.
Preventative action: Improve quality control measures to prevent similar issues in the future.
Another example: A customer complained about a long wait time for customer service.
Corrective action: Address the customer's issue and provide compensation if necessary.
Preventative action: ...read more
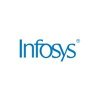
Asked in Infosys

Q. How do you control quality during production?
Quality control for production can be controlled through various methods and processes.
Implementing quality control measures at each stage of production
Setting up quality control checkpoints and inspections
Using statistical process control techniques to monitor and analyze production data
Training and educating production staff on quality control standards
Implementing corrective and preventive actions to address quality issues
Regularly reviewing and updating quality control pr...read more
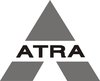
Asked in ATRA Pharmaceuticals

Q. Give a example of major deviation which includes investigation, corre tion, preventive action & corrective action. Workflow of change control, risk assessment procedure, self inspection procedures.
A major deviation occurred in the production process, leading to investigation, correction, preventive and corrective actions.
During the production process, a batch of medicine was found to have incorrect labeling.
An investigation was conducted to determine the root cause of the labeling error.
The correction involved re-labeling the affected batch and ensuring proper labeling procedures were followed.
Preventive actions included retraining staff on labeling procedures and impl...read more
Share interview questions and help millions of jobseekers 🌟
Asked in LifePharma FZE

Q. How do you handle misbranded or improperly labeled drugs during a recall?
Misbranded/improperly labelled drugs during recall can be handled by following proper procedures and guidelines.
Immediately stop distribution and recall the product
Notify regulatory authorities and customers
Investigate the root cause of the misbranding/improper labelling
Correct the labelling and repackage the product if necessary
Dispose of the recalled product properly
Implement corrective actions to prevent future occurrences
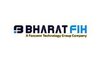
Asked in Bharat FIH

Q. Why are you searching for this type of field?
I am searching for this field because of my passion for ensuring quality and improving processes.
Passion for ensuring quality
Interest in improving processes
Enjoy leading and motivating a team
Strong attention to detail
Experience in quality assurance/control
Desire to contribute to the success of the organization
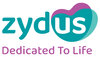
Asked in Zydus Healthcare

Q. How do you investigate OOT, incidents, and deviations?
Investigating OOT, incidents, deviations, etc.
Gather all relevant information about the OOT, incident, or deviation
Review documentation, records, and data related to the issue
Interview personnel involved to gather additional details
Perform root cause analysis to identify the underlying cause
Implement corrective actions to prevent recurrence
Document the investigation process and findings for future reference
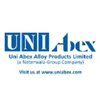
Asked in Uni Abex Alloy Products

Q. If a product needs urgent dispatch, what action would you take as a quality assurance/quality control team leader?
I would ensure that the urgent dispatch does not compromise the quality of the product.
I would quickly assess the situation and identify any potential quality issues that may arise from the urgent dispatch.
I would communicate with the production team to understand the urgency and the reason for the urgent dispatch.
I would prioritize the quality checks and inspections to ensure that the product meets the required quality standards.
I would document all the quality checks and in...read more
Asked in Amaze Solutions

Q. If your parcel and shipment are held at your station, what immediate actions would you take?
I would immediately investigate the reason for the hold and take necessary actions to resolve the issue.
Check the reason for the hold
Communicate with relevant parties such as the shipping company and customs officials
Take necessary actions to resolve the issue such as providing additional documentation or addressing any issues with the shipment
Ensure timely delivery of the parcel

Asked in Udaan

Q. What is FIFO, LIFO, MBQ and SKU?
FIFO, LIFO, MBQ and SKU are inventory management terms.
FIFO stands for First-In-First-Out and is a method of inventory management where the oldest stock is sold first.
LIFO stands for Last-In-First-Out and is a method of inventory management where the newest stock is sold first.
MBQ stands for Minimum Buy Quantity and is the minimum quantity of a product that must be purchased in a single order.
SKU stands for Stock Keeping Unit and is a unique identifier for each distinct produ...read more
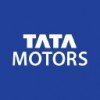
Asked in Tata Motors

Q. Drilling machine and rimar machine different
Drilling machine and rimar machine are different in terms of their purpose and functionality.
Drilling machine is used to create holes in various materials, while rimar machine is used for shaping and finishing rims of objects.
Drilling machine typically has a rotating drill bit, while rimar machine may have different tools such as grinding wheels or cutters.
Drilling machine is commonly used in construction, woodworking, and metalworking industries, while rimar machine is often...read more
Asked in Almity Auto Ancillary

Q. Why need quality products in manufacturing unit &Any where any how.
Quality products are essential for customer satisfaction, brand reputation, and compliance with regulations.
Quality products ensure customer satisfaction and loyalty.
Quality products enhance brand reputation and increase market share.
Quality products comply with regulations and avoid legal penalties.
Quality products reduce waste, rework, and production costs.
Quality products improve employee morale and productivity.
Examples: medical devices, food and beverages, automotive par...read more
Asked in LifePharma FZE

Q. What is data integrity for a prospective validation batch, and what CAPA is necessary?
Data integrity is crucial for prospective validation batch. CAPA is necessary to address any issues.
Ensure accurate and complete data collection and documentation
Perform regular audits and reviews to identify any potential issues
Implement corrective and preventive actions (CAPA) to address any identified issues
Document all actions taken and ensure they are effective in maintaining data integrity
Examples of CAPA include retraining staff, updating procedures, and improving equi...read more
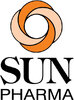
Asked in Sun Pharmaceutical Industries

Q. What is the role of quality controls?
Quality controls ensure that products or services meet specified standards and customer expectations.
Quality controls are processes or systems put in place to monitor and evaluate the quality of products or services.
They help identify and correct any defects or deviations from the desired standards.
Quality controls ensure consistency and reliability in the production or delivery of goods or services.
They involve setting quality standards, establishing inspection procedures, a...read more

Asked in Escorts Kubota Limited

Q. What is a quality circle?
Quality circle is a group of employees who voluntarily come together to identify and solve work-related problems.
Quality circle is a participatory management technique.
It involves a group of employees who meet regularly to identify and solve work-related problems.
The group is usually led by a facilitator and includes members from different departments.
The aim is to improve quality, productivity, and employee morale.
Examples of quality circle activities include brainstorming s...read more
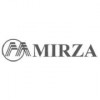
Asked in Mirza International

Q. What are the three main sizing systems?
The three main sizing systems are metric, imperial, and alphabetic.
Metric system is based on units of measurement such as meters, kilograms, and liters.
Imperial system is commonly used in the United States and includes units like inches, pounds, and gallons.
Alphabetic sizing system is used for clothing and shoe sizes, such as XS, S, M, L, XL, etc.
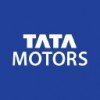
Asked in Tata Motors

Q. What are the differences between Vernier calipers and micrometers?
Vernier calipers and micrometers are different measuring tools used in quality control.
Vernier calipers are used to measure dimensions with high accuracy, while micrometers are used for precise measurements.
Vernier calipers have a sliding scale and a main scale, allowing for both internal and external measurements.
Micrometers have a spindle and anvil, and are typically used for measuring thickness or diameter.
Both tools are commonly used in quality control to ensure accurate ...read more
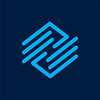
Asked in HGS

Q. What is your definition of a leader?
A leader is someone who guides, inspires, and motivates a group of people towards a common goal.
Leaders have a clear vision and communicate it effectively
They lead by example and set high standards for themselves and their team
They empower their team members and encourage collaboration
Leaders are adaptable and able to make tough decisions
They inspire trust and respect through their actions and words
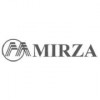
Asked in Mirza International

Q. What is an aglet and why is it necessary?
An aglet is a small plastic or metal tube used to secure the ends of shoelaces and prevent fraying.
Aglets are necessary to keep shoelaces from unraveling and fraying.
They provide a clean and finished look to the ends of shoelaces.
Aglets make it easier to thread shoelaces through eyelets or holes.
They help prevent wear and tear on the shoelaces, increasing their lifespan.
Aglets can also be decorative and add personal style to footwear.
Examples of aglets can be found on various...read more
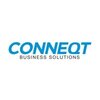
Asked in Conneqt Business Solutions

Q. Why is analysis required to fix quality problems?
Analysis is required to fix quality problems as it helps in identifying the root cause and implementing effective solutions.
Analysis helps in identifying the root cause of the quality problem
It helps in implementing effective solutions to prevent the problem from recurring
Without analysis, the problem may persist or even worsen
Analysis can also help in improving overall quality processes and systems
Examples of analysis tools include Pareto charts, fishbone diagrams, and stati...read more
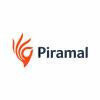
Asked in Piramal Group

Q. Line clearance check points in shop floor activities.
Line clearance check points are critical to ensure product quality and safety.
Line clearance should be performed before starting any new activity or batch.
All equipment, tools, and surfaces should be cleaned and sanitized.
Personnel should wear appropriate PPE and follow proper hygiene practices.
Documentation of line clearance should be maintained for audit purposes.
Examples of line clearance check points include cleaning of mixing vessels, verification of batch records, and i...read more
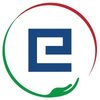
Asked in Equitas Small Finance Bank

Q. What is your strength?
My strength is attention to detail and problem-solving skills.
I have a keen eye for detail and can spot even the smallest errors or inconsistencies.
I am able to analyze complex problems and come up with effective solutions.
I am highly organized and can prioritize tasks to ensure quality standards are met.
I have strong communication skills, which helps in effectively conveying quality requirements and resolving issues.
I am proactive in identifying potential quality issues and ...read more
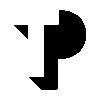
Asked in Teleperformance

Q. What is customer satisfaction?
Customer satisfaction is the measure of how happy customers are with a company's products or services.
It is important to regularly measure customer satisfaction through surveys or feedback forms.
Customer satisfaction can impact a company's reputation and bottom line.
Improving customer satisfaction can lead to increased customer loyalty and repeat business.
Examples of factors that can impact customer satisfaction include product quality, customer service, and pricing.
A high le...read more
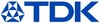
Asked in TDK India Private Limited

Q. How can you provide a zero rejection report?
To give a zero rejection report, we need to implement a robust quality control system and ensure adherence to it.
Establish clear quality standards and communicate them to all team members
Conduct regular quality checks at every stage of the production process
Implement corrective actions immediately when quality issues are identified
Train team members on quality control procedures and provide regular feedback
Maintain accurate records of quality checks and corrective actions tak...read more
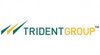
Asked in Trident Group

Q. weiving and types of machines looms
Weaving machines, also known as looms, are used to create woven fabrics.
There are various types of looms, including handlooms, power looms, and automatic looms.
Handlooms are operated manually and are commonly used for small-scale production or traditional weaving.
Power looms are mechanized and can produce fabrics on a larger scale.
Automatic looms are computer-controlled and can perform complex weaving patterns.
Different types of looms have different features and capabilities,...read more
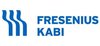
Asked in Fresenius Kabi

Q. What is a pH calibration point?
pH calibration point is the value at which a pH meter is calibrated to ensure accurate readings.
pH calibration point is a reference point used to calibrate pH meters.
It is usually set to pH 7.0, which is considered neutral.
Other calibration points may be used depending on the specific application.
Calibration is important to ensure accurate pH measurements.
Calibration should be performed regularly to maintain accuracy.
Interview Experiences of Popular Companies
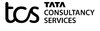
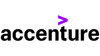
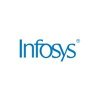
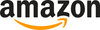
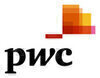
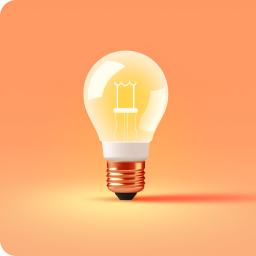
Calculate your in-hand salary
Confused about how your in-hand salary is calculated? Enter your annual salary (CTC) and get your in-hand salary
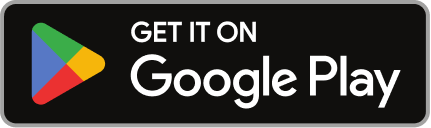
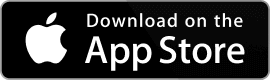
Reviews
Interviews
Salaries
Users
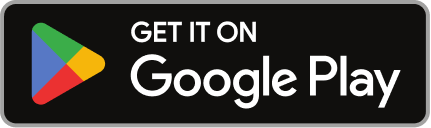
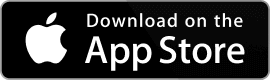