Quality Lead
20+ Quality Lead Interview Questions and Answers
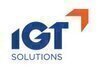
Asked in IGT Solutions

Q. What is Root cause analysis, FMEA, CTQ, 7QC tools, SIPOC, COPIS?
Root cause analysis, FMEA, CTQ, 7QC tools, SIPOC, COPIS are quality tools used to identify and solve problems.
Root cause analysis is a problem-solving technique used to identify the underlying cause of a problem.
FMEA (Failure Mode and Effects Analysis) is a proactive approach to identify and mitigate potential failures in a process or product.
CTQ (Critical to Quality) is a tool used to identify the critical parameters that affect the quality of a product or service.
7QC tools ...read more
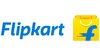
Asked in Flipkart

Q. How closely have you worked with supply chain operations, and what would you do to reduce picking time in the warehouse?
I have closely worked with supply chain operations and would implement process improvements to reduce picking time in the warehouse.
I have collaborated with supply chain teams to optimize inventory management and streamline processes.
Implemented barcode scanning technology to improve accuracy and efficiency in picking orders.
Analyzed data to identify bottlenecks in the picking process and implemented solutions such as rearranging warehouse layout or adjusting picking routes.
T...read more
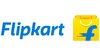
Asked in Flipkart

Q. What technique would you use to reduce the SCM operations in a warehouse?
Implementing lean principles such as 5S, Kanban, and Just-in-Time inventory management can help reduce SCM operations in a warehouse.
Implement 5S methodology to organize the warehouse and reduce waste
Utilize Kanban system to optimize inventory levels and streamline processes
Adopt Just-in-Time inventory management to minimize excess inventory and improve efficiency
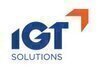
Asked in IGT Solutions

Q. How do you handle employees with performance issues?
Address the root cause of the will issues and provide support and resources to help employees overcome them.
Have a conversation with the employee to understand the underlying cause of their lack of will
Provide resources such as counseling or training to help employees overcome personal or professional challenges
Set clear expectations and goals for the employee and provide regular feedback and support
Recognize and reward employees for their efforts and achievements
Consider dis...read more
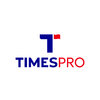
Asked in TimesPro

Q. What parameters do you check on content to ensure its quality?
Parameters checked for content quality include accuracy, relevance, clarity, consistency, and tone.
Accuracy - Ensure information is factually correct and up-to-date.
Relevance - Confirm content aligns with the target audience and purpose.
Clarity - Check for clear and understandable language, avoiding jargon or ambiguity.
Consistency - Maintain uniformity in style, formatting, and tone throughout the content.
Tone - Evaluate the appropriateness of the tone for the intended messag...read more
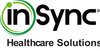
Asked in inSync Healthcare Solutions

Q. Tell me about the quality tools you have used to improve user experience.
I have used various quality tools such as Six Sigma, Lean, and Root Cause Analysis to improve user experience.
Implemented Six Sigma methodology to reduce defects and improve customer satisfaction
Utilized Lean principles to streamline processes and eliminate waste
Conducted Root Cause Analysis to identify and address underlying issues
Used Fishbone diagrams to identify potential causes of problems
Implemented Statistical Process Control to monitor and improve quality over time
Quality Lead Jobs
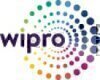
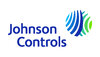
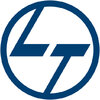
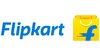
Asked in Flipkart

Q. What are your problem-solving techniques?
I use a combination of root cause analysis, brainstorming, and data analysis to solve problems efficiently.
Identify the root cause of the problem before jumping to solutions
Brainstorm potential solutions with a team or individually
Use data analysis to make informed decisions and track progress
Implement solutions and monitor results for effectiveness
Adjust strategies as needed based on feedback and outcomes
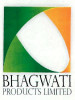
Asked in Bhagwati Products

Q. 5s and 7QC tools, what is quality
5S and 7QC tools are methods used to ensure quality in a workplace.
Quality is meeting or exceeding customer expectations.
5S focuses on workplace organization and cleanliness to improve efficiency and reduce errors.
7QC tools are problem-solving techniques used to identify and address quality issues.
Examples of 7QC tools include Pareto charts, cause-and-effect diagrams, and statistical process control.
Quality is a continuous improvement process that involves everyone in the org...read more
Share interview questions and help millions of jobseekers 🌟
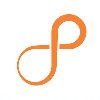
Asked in Persistent Systems

Q. Write a program to separate odd and even numbers using a third variable.
A program to write odd and even numbers using a third variable.
Declare three variables: num, even, and odd.
Take input from the user for num.
Use if-else statement to check if num is even or odd.
If even, assign num to even variable, else assign to odd variable.
Print even and odd variables.
Asked in Uges Powermax

Q. List of Indian standard code you will use in your work
The Indian standard codes commonly used in Quality Lead work.
IS 456:2000 - Code of practice for plain and reinforced concrete
IS 2062:2011 - Hot rolled medium and high tensile structural steel
IS 800:2007 - General construction in steel
IS 1343:2012 - Prestressed concrete
IS 383:2016 - Coarse and fine aggregates for concrete
IS 10262:2009 - Concrete mix proportioning
IS 2386:2016 - Methods of test for aggregates
IS 1200:Part 1:1992 - Method of measurement of building and civil engin...read more
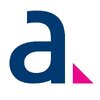
Asked in Accurate Background

Q. How will you ensure that errors are reduced?
I will implement a thorough quality control process and continuously analyze data to identify and address root causes of errors.
Establish clear quality standards and communicate them to the team
Conduct regular audits and inspections to identify errors
Analyze data to identify trends and root causes of errors
Implement corrective actions to address identified issues
Provide training and support to team members to prevent future errors
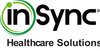
Asked in inSync Healthcare Solutions

Q. How many errors were you marking?
I marked a total of 25 errors during the quality check process.
I kept a record of all the errors I found during the quality check process.
The errors ranged from minor typos to major coding errors.
I made sure to communicate all the errors to the relevant team members for correction.
I also provided suggestions for preventing similar errors in the future.
Overall, I was able to ensure a high level of quality in the final product.
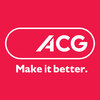
Asked in ACG Worldwide

Q. What is iso ? Explain the terms
ISO is a set of international standards that ensure quality, safety, and efficiency in various industries.
ISO stands for International Organization for Standardization
ISO standards cover various industries such as manufacturing, healthcare, and technology
ISO standards ensure quality, safety, and efficiency in products and services
Examples of ISO standards include ISO 9001 for quality management and ISO 27001 for information security
ISO certification is a process of verifying ...read more
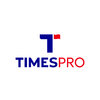
Asked in TimesPro

Q. What quality standards did you follow in your last organization?
ISO 9001:2015 and industry-specific standards were followed, with regular audits and continuous improvement initiatives.
ISO 9001:2015 certification maintained
Industry-specific quality standards adhered to
Regular internal and external audits conducted
Continuous improvement initiatives implemented
Quality metrics tracked and monitored
Asked in Uges Powermax

Q. How do you optimize SOP and SFQP?
To make SOP & SFQP the best, ensure clear and concise instructions, regular updates, employee training, and continuous improvement.
Create clear and concise Standard Operating Procedures (SOP) and Standardized Field Quality Plans (SFQP)
Regularly update SOP and SFQP to reflect changes in processes or regulations
Provide comprehensive training to employees on SOP and SFQP
Encourage feedback from employees to identify areas for improvement
Implement a continuous improvement process ...read more
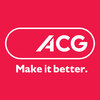
Asked in ACG Worldwide

Q. Is CAPA required? Explain briefly.
Yes, CAPA (Corrective and Preventive Action) is required for quality improvement.
CAPA is a systematic approach to identify, investigate, and correct quality issues.
It involves root cause analysis, corrective action, and preventive action.
CAPA helps to prevent recurrence of quality issues and improve overall quality.
Examples of CAPA include process improvements, training, and equipment maintenance.
CAPA is a key component of quality management systems such as ISO 9001 and FDA r...read more
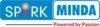
Asked in Spark Minda

Q. What is your definition of quality?
Quality is meeting or exceeding customer expectations through consistent and reliable performance.
Quality is a measure of how well a product or service meets the needs and expectations of the customer.
It involves consistent and reliable performance, meeting or exceeding customer requirements.
Quality can be achieved through effective processes, continuous improvement, and a focus on customer satisfaction.
Examples of quality include products that are durable, reliable, and perf...read more
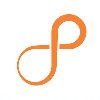
Asked in Persistent Systems

Q. Architecture of the prev project
The architecture of the previous project was based on a microservices approach.
The project was divided into smaller, independent services that communicated with each other through APIs.
Each service had its own database and could be developed and deployed independently.
The architecture allowed for better scalability and fault tolerance.
Examples of microservices used in the project include user authentication, payment processing, and order management.
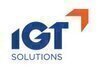
Asked in IGT Solutions

Q. What were your Key Result Areas (KRAs) in your last organization?
In my last organization, I focused on enhancing quality processes, ensuring compliance, and driving continuous improvement initiatives.
Developed and implemented quality assurance protocols that reduced defects by 30%.
Led cross-functional teams in root cause analysis to address recurring quality issues.
Conducted regular training sessions for staff on quality standards and best practices.
Collaborated with product development teams to integrate quality considerations from the de...read more
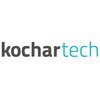
Asked in KocharTech

Q. 7 QC tools and their usages
The 7 QC tools are used for quality control and problem-solving in various industries.
Check sheet - for collecting and organizing data
Pareto chart - for identifying the most significant factors
Cause and effect diagram - for identifying root causes of problems
Histogram - for visualizing data distribution
Scatter diagram - for identifying relationships between variables
Control chart - for monitoring process performance over time
Flow chart - for documenting processes and identify...read more
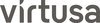
Asked in Virtusa Software Services

Q. Given a string, find the first non-repeating character from it.
Find the first non-repeating character in a string
Iterate through the string and count the frequency of each character
Return the first character with a frequency of 1
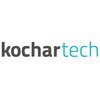
Asked in KocharTech

Q. Quality Tools and Techniques.
Quality tools and techniques are methods used to ensure products or services meet quality standards.
Quality tools like Pareto charts, fishbone diagrams, and control charts help identify and solve quality issues.
Techniques such as Six Sigma, Lean, and Total Quality Management are used to improve processes and reduce defects.
Quality audits, inspections, and statistical sampling are also common tools used to monitor and improve quality.
Training employees on quality tools and tec...read more
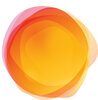
Asked in UPL

Q. What are your expectations from our company?
Our expectations from company include high quality standards, continuous improvement, adherence to regulations, and customer satisfaction.
Maintaining high quality standards in all products and services
Implementing continuous improvement processes to enhance quality
Adhering to regulations and standards set by relevant authorities
Ensuring customer satisfaction through quality products and services
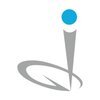
Asked in Infogain

Q. Metrics calculation for team
Metrics calculation for team
Identify key performance indicators (KPIs) to measure team performance
Collect relevant data to calculate the metrics
Define formulas or methods to calculate each metric
Analyze the metrics to identify trends, patterns, and areas for improvement
Present the metrics in a clear and concise manner to stakeholders
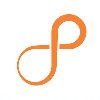
Asked in Persistent Systems

Q. Finding locator
A locator is a unique identifier used to find a specific element on a webpage.
Locators can be based on various attributes such as ID, class, name, tag name, link text, and CSS selector.
XPath is another commonly used locator that allows for more complex searches.
Locators should be chosen carefully to ensure they are stable and not prone to change.
Examples of locators: #id, .class, name, tagname, linktext, cssselector, xpath
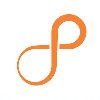
Asked in Persistent Systems

Q. How do you identify XPath?
XPath is a language used to locate elements in an XML document.
XPath uses path expressions to select nodes or node sets in an XML document
It can be used to navigate through elements and attributes
Examples of XPath expressions: //bookstore/book[price>35.00], /bookstore/book[1]/title
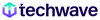
Asked in Techwave Consulting

Q. Real time challenges
Real time challenges faced in Quality Lead role
Managing conflicting priorities and deadlines
Ensuring compliance with regulations and standards
Dealing with unexpected quality issues
Balancing cost and quality
Managing stakeholder expectations
Keeping up with new technologies and industry trends
Interview Questions of Similar Designations
Interview Experiences of Popular Companies
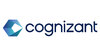
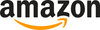
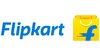
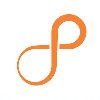
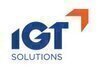
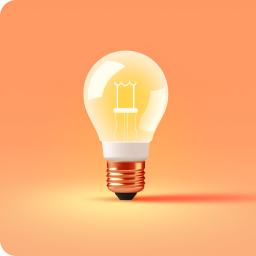
Calculate your in-hand salary
Confused about how your in-hand salary is calculated? Enter your annual salary (CTC) and get your in-hand salary
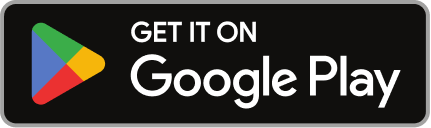
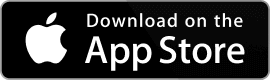
Reviews
Interviews
Salaries
Users
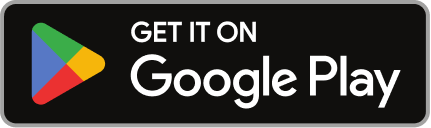
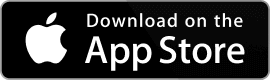