Project Manager-Production/Manufacturing/Maintenance
30+ Project Manager-Production/Manufacturing/Maintenance Interview Questions and Answers
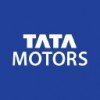
Asked in Tata Motors

Q. What is mean by production engineer and what actual define the production word in all the auto sector?
A production engineer is responsible for designing, implementing, and improving manufacturing processes in the auto sector.
Production engineer is involved in the planning and execution of manufacturing processes.
They focus on optimizing production efficiency, quality, and cost-effectiveness.
They design and implement production systems, equipment, and tools.
Production engineers analyze data and identify areas for improvement.
They collaborate with cross-functional teams to ensu...read more
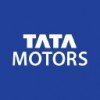
Asked in Tata Motors

Q. Give the reason behind this production field,,why it is needed to create a circle of the automobile industries
The production field is needed to create a circle of automobile industries to ensure efficient and cost-effective manufacturing processes.
Production field helps in streamlining the manufacturing process of automobile industries
It ensures efficient and cost-effective production of automobiles
It helps in maintaining quality standards and meeting customer demands
The circle of automobile industries includes suppliers, manufacturers, distributors, and retailers
Collaboration among ...read more
Project Manager-Production/Manufacturing/Maintenance Interview Questions and Answers for Freshers
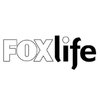
Asked in Foxlink Group

Q. What is uph and upph,material management
UPH stands for Units Per Hour and UPPH stands for Units Per Person Per Hour. Material management involves the planning, procurement, storage, and control of materials used in production.
UPH is a measure of production efficiency, indicating the number of units produced in an hour.
UPPH is a measure of individual productivity, indicating the number of units produced by each person in an hour.
Material management ensures the availability of required materials at the right time, in...read more
Asked in Iisd

Q. What precautions should be taken while doing service work of heavy machinery?
Precautions for service work of heavy machinery
Ensure proper lockout/tagout procedures are followed
Wear appropriate personal protective equipment (PPE)
Inspect machinery for any signs of damage or wear
Use proper lifting techniques and equipment
Follow manufacturer's instructions and maintenance guidelines
Train and educate workers on safe service procedures
Have a clear communication plan in place
Perform regular risk assessments and implement necessary controls
Keep work areas cle...read more
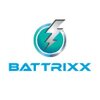
Asked in Battrixx

Q. What issues might we face during the battery warranty period?
Issues during battery warranty period
Battery failure due to manufacturing defects
Reduced battery life due to improper usage or maintenance
Inadequate charging infrastructure leading to battery damage
Difficulty in obtaining replacement batteries
Disputes over warranty coverage
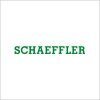
Asked in Schaeffler India

Q. Automobile sector next 10 years what condition?
The automobile sector is expected to experience significant advancements and changes in the next 10 years.
Increased adoption of electric vehicles
Advancements in autonomous driving technology
Integration of artificial intelligence in manufacturing processes
Shift towards sustainable and eco-friendly practices
Rise of shared mobility services
Development of connected cars and smart infrastructure
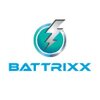
Asked in Battrixx

Q. Which type of welding should be used for lithium batteries?
Lithium batteries require welding with low heat input and minimal deformation. Laser welding is the best option.
Lithium batteries are sensitive to heat and pressure, so welding should be done with low heat input and minimal deformation.
Laser welding is the best option for welding lithium batteries as it provides precise and controlled heat input.
Other welding methods like resistance welding and ultrasonic welding can also be used, but they require careful control of heat and ...read more
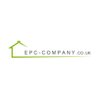
Asked in EPC Company

Q. What is the management process for a business operational cycle? Explain step by step.
The management process for business operational cycle involves planning, execution, monitoring, and control.
Planning involves setting goals, defining objectives, and creating a strategy.
Execution involves implementing the plan and carrying out the tasks.
Monitoring involves tracking progress and identifying any issues or deviations from the plan.
Control involves taking corrective action to address any issues and ensure the plan stays on track.
The cycle then repeats with contin...read more
Share interview questions and help millions of jobseekers 🌟
Asked in Iisd

Q. What checks should be performed before starting heavy machinery?
Before starting heavy machinery, it is important to check various aspects to ensure safety and proper functioning.
Inspect the machinery for any visible damage or wear and tear.
Check the fluid levels, such as oil, coolant, and hydraulic fluid.
Ensure all safety guards and devices are in place and functioning correctly.
Verify that all necessary maintenance and repairs have been performed.
Test the emergency stop button and other safety features.
Confirm that the machinery is prope...read more
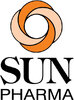
Asked in Sun Pharmaceutical Industries

Q. Types of reactors and their MOC, liquid handling.?
Reactors used in production/manufacturing/maintenance and their materials of construction and liquid handling.
Types of reactors include batch, continuous, stirred tank, and plug flow reactors.
Materials of construction for reactors include stainless steel, glass-lined steel, and exotic alloys.
Liquid handling systems include pumps, valves, and piping made of materials compatible with the process fluids.
Selection of reactor type and materials of construction depends on the proce...read more
Asked in Taco Prestolite Electric

Q. What is the 5S methodology?
5S is a methodology used to organize and maintain a clean and efficient workplace.
5S stands for Sort, Set in Order, Shine, Standardize, and Sustain.
Sort involves removing unnecessary items from the workplace.
Set in Order focuses on arranging necessary items in a logical and efficient manner.
Shine involves cleaning and maintaining the workplace.
Standardize establishes consistent processes and procedures.
Sustain ensures the ongoing adherence to the 5S principles.
Example: Implem...read more
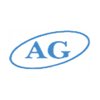
Asked in Ag Industries

Q. WHAT 4.0 MANUFACTURING,WHAT IS PROGNOSTIC?
Prognostic is a predictive maintenance technique used in Industry 4.0 manufacturing.
Prognostic uses data analysis and machine learning to predict when maintenance is needed.
It helps prevent unexpected downtime and reduces maintenance costs.
Examples of prognostic techniques include vibration analysis and oil analysis.
Prognostic is a key component of smart manufacturing and Industry 4.0.
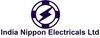
Asked in India Nippon Electricals

Q. What are the manufactured products?
Manufacturing products are goods produced through a systematic process involving raw materials, machinery, and labor.
Manufacturing products involve transforming raw materials into finished goods.
The process includes various stages such as design, production, quality control, and packaging.
Examples of manufacturing products include automobiles, electronics, clothing, furniture, and food products.
Asked in X-Byte Technolab

Q. What is your plan for consequence management?
Consequence management plan involves identifying potential risks, developing mitigation strategies, and establishing protocols for responding to incidents.
Identify potential risks and hazards
Develop mitigation strategies to minimize the impact of incidents
Establish protocols for responding to incidents
Train employees on the consequence management plan
Regularly review and update the plan to ensure its effectiveness
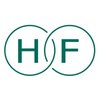
Asked in Hindustan Foods

Q. what is sweft volume?
Sweft volume refers to the total volume of air or gas that is moved or exchanged in a specific area or system.
Sweft volume is a measure used in production, manufacturing, and maintenance to assess the efficiency of air or gas flow.
It is often used in HVAC systems to determine the amount of air being circulated in a building.
Sweft volume can be calculated by multiplying the air velocity by the cross-sectional area of the duct or system.
For example, if the air velocity is 10 me...read more
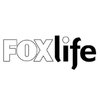
Asked in Foxlink Group

Q. What are the KPIs of production?
KPI of production refers to the key performance indicators that measure the effectiveness and efficiency of production processes.
KPIs help monitor and evaluate the performance of production activities.
Examples of production KPIs include production output, quality, efficiency, downtime, and cost per unit.
KPIs provide insights into areas for improvement and help in making data-driven decisions.
KPIs should be specific, measurable, achievable, relevant, and time-bound (SMART).
Reg...read more
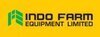
Asked in Indo Farm Equipment

Q. What metal is a file made of?
The metal of a file is typically steel.
The metal used in files is usually steel due to its hardness and durability.
Steel files are commonly used in production, manufacturing, and maintenance industries.
Other metals like high carbon steel or tungsten carbide may also be used for specific applications.
The choice of metal depends on the intended use of the file, such as cutting, shaping, or smoothing materials.
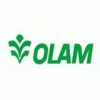
Asked in Olam

Q. Describe the different types of HSE permits.
Permits are documents that authorize specific work activities and ensure compliance with safety regulations.
Types of permits include hot work permits, confined space permits, excavation permits, and electrical permits.
Hot work permits are required for any work involving open flames or heat sources.
Confined space permits are required for work in enclosed spaces with limited entry and exit points.
Excavation permits are required for any work involving digging or excavation.
Elect...read more
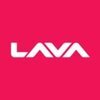
Asked in Lava International

Q. What is DPR?
DPR stands for Daily Progress Report.
DPR is a document that provides a summary of the progress made on a project on a daily basis.
It includes information about tasks completed, milestones achieved, challenges faced, and resources utilized.
DPR helps in tracking the project's progress, identifying bottlenecks, and making informed decisions.
It is commonly used in project management, particularly in production, manufacturing, and maintenance.
Example: A DPR for a manufacturing pro...read more
Asked in Autonix Auto Industries

Q. Reality of the company Manufacturer PPM , quantity of manpower
The reality of Manufacturer PPM company and quantity of manpower.
Manufacturer PPM is a well-established company with a strong reputation in the industry.
The company has a large workforce that is skilled and experienced in production, manufacturing, and maintenance.
The quantity of manpower varies depending on the specific needs of each project.
The company is committed to providing high-quality products and services to its customers.
Efficient management of manpower is a key fac...read more
Asked in Avon Flavours

Q. What is the difference between FSSAI and ISO?
FSSAI is a regulatory body in India for food safety and standards while ISO is a set of international standards for quality management.
FSSAI ensures the safety and quality of food products in India while ISO focuses on quality management systems in various industries.
FSSAI is a government body while ISO is a non-governmental organization.
FSSAI provides licenses and certifications to food businesses while ISO provides certifications for quality management systems.
FSSAI has spe...read more
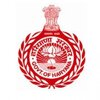
Asked in Haryana Industries

Q. How do you plan to advance your career?
Continuous learning, networking, and taking on challenging projects can improve my career.
Pursue additional education or certifications
Attend industry conferences and events
Join professional organizations and networking groups
Take on new and challenging projects to gain experience
Seek feedback and mentorship from experienced professionals
Asked in GlobalYDK Electric

Q. What is a check sheet?
A check sheet is a simple tool used to collect and organize data for analysis and problem-solving.
It is a structured form or template used to record data
It helps in standardizing data collection
It can be used to track defects, errors, or other types of observations
It provides a visual representation of data for easy analysis
Examples include a checklist for equipment maintenance, a tally sheet for counting defects, or a log sheet for recording production data
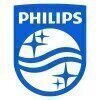
Asked in Philips

Q. How do you solve critical problems?
Critical problems can be solved by identifying the root cause, brainstorming solutions, and implementing the best one.
Identify the root cause of the problem
Brainstorm potential solutions with a team
Evaluate each solution and choose the best one
Implement the chosen solution and monitor its effectiveness
Make adjustments as necessary
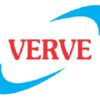
Asked in Verve Human Care Laboratories

Q. What is CIP?
CIP stands for Clean-in-Place, a method used in production/manufacturing to clean equipment without disassembly.
CIP is a cleaning technique used in industries like food processing, pharmaceuticals, and dairy.
It involves circulating cleaning solutions through the equipment to remove contaminants.
CIP eliminates the need for manual cleaning and reduces downtime.
Examples of CIP systems include automated cleaning of pipelines, tanks, and filling machines.
CIP ensures hygiene, produ...read more
Asked in X-Byte Technolab

Q. How will you manage KPIs?
I will manage KPI by setting clear objectives, tracking performance, analyzing data, and implementing corrective actions.
Define key performance indicators (KPIs) that align with the project goals and objectives
Establish a baseline for each KPI to measure progress and performance
Regularly track and monitor the KPIs using appropriate tools and systems
Analyze the data collected to identify trends, patterns, and areas for improvement
Implement corrective actions or strategies to a...read more
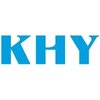
Asked in KHY ELECTRONIC

Q. What is CAPA?
CAPA stands for Corrective and Preventive Action. It is a systematic approach to identify, investigate, and resolve issues in order to prevent their recurrence.
CAPA is a quality management process used to address and resolve problems or non-conformities in a systematic manner.
It involves identifying the root cause of the problem, implementing corrective actions to address the immediate issue, and preventive actions to prevent its recurrence.
CAPA typically includes steps like ...read more
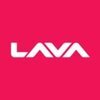
Asked in Lava International

Q. What is acceptance quality limit (AQL) sampling?
Waking according to AQL refers to the process of inspecting a sample of products to determine if they meet the acceptable quality level.
AQL stands for Acceptable Quality Level
It is a statistical sampling method used to determine if a batch of products meets the required quality standards
The sample size and acceptance criteria are determined based on the level of risk and the importance of the product
If the number of defects found in the sample exceeds the AQL, the entire batc...read more
Asked in X-Byte Technolab

Q. How do you ensure consistent performance?
Performance consistency can be assured through proper planning, monitoring, and control of processes.
Establish clear performance standards and communicate them to the team
Regularly monitor and measure performance against these standards
Identify and address any deviations from the standards
Implement corrective actions to prevent future deviations
Continuously improve processes to optimize performance
Provide training and development opportunities to enhance skills and knowledge
U...read more
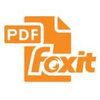
Asked in Foxit

Q. What is the difference between QA and QC?
QA ensures quality in the process of product development while QC ensures quality in the final product.
QA focuses on preventing defects while QC focuses on identifying and correcting defects.
QA is a proactive approach while QC is a reactive approach.
QA involves continuous monitoring and improvement of the process while QC involves testing and inspection of the final product.
QA is a responsibility of everyone involved in the process while QC is usually the responsibility of a ...read more
Interview Experiences of Popular Companies
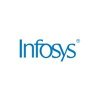
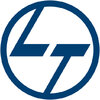
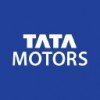
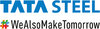
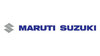
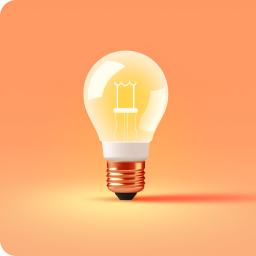
Calculate your in-hand salary
Confused about how your in-hand salary is calculated? Enter your annual salary (CTC) and get your in-hand salary
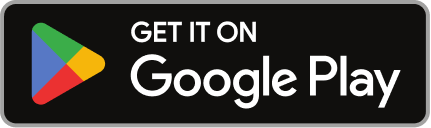
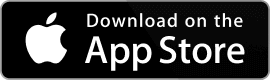
Reviews
Interviews
Salaries
Users
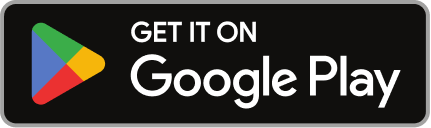
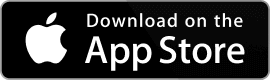