Assistant Manager Quality Assurance
60+ Assistant Manager Quality Assurance Interview Questions and Answers
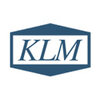
Asked in KLM Laboratories

Q. What are the guidelines for a Quality Management System (QMS), and can you provide an example of any QMS activity such as a corrective action (CC), deviation, or market complaint investigation?
Guidelines for a Quality Management System (QMS) and examples of QMS activities
Guidelines for QMS include establishing processes, monitoring performance, and implementing corrective actions
Example of a QMS activity like a corrective action could be identifying a root cause of a quality issue and implementing a solution
Another example could be investigating a deviation from standard procedures and implementing preventive measures
Market complaint investigation involves analyzin...read more
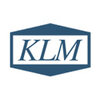
Asked in KLM Laboratories

Q. What is your knowledge of regulatory affairs, particularly in relation to dossiers, licensing, and product permissions?
Knowledge of regulatory affairs in relation to dossiers, licensing, and product permissions.
Understanding of regulatory requirements for submitting dossiers for product approval
Knowledge of the licensing process and requirements for different markets
Familiarity with obtaining product permissions from regulatory authorities
Experience in preparing and maintaining regulatory documentation
Ability to ensure compliance with regulatory standards and guidelines
Assistant Manager Quality Assurance Interview Questions and Answers for Freshers
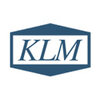
Asked in KLM Laboratories

Q. What are the guidelines for conducting hold time studies and the time periods for different stages in Oral Solid Dosage (OSD) forms?
Hold time studies in OSD forms involve determining the time periods at different stages to ensure product quality and stability.
Hold time studies should be conducted to determine the maximum time a product can be held at different stages without compromising quality.
Different stages in OSD forms include blending, compression, coating, and packaging.
Hold time periods can vary depending on the specific formulation and manufacturing process.
For example, hold time for blending ma...read more
Asked in abCoffee

Q. What is Haccp? Do you know how to make CAP? Basic food safety related questions
HACCP stands for Hazard Analysis and Critical Control Points. CAP refers to Corrective Action Plan.
HACCP is a systematic approach to identify, evaluate, and control food safety hazards.
It involves seven principles: conducting hazard analysis, determining critical control points, establishing critical limits, monitoring procedures, corrective actions, verification procedures, and record-keeping.
CAP is a plan developed to address and correct any identified non-conformities or d...read more
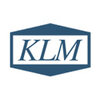
Asked in KLM Laboratories

Q. What are the different types of process validation and their descriptions?
Different types of process validation include prospective validation, concurrent validation, and retrospective validation.
Prospective validation: Validation conducted before the process is put into routine production.
Concurrent validation: Validation conducted during routine production.
Retrospective validation: Validation conducted on processes that have been in use for some time.
Examples: Prospective validation would involve testing a new manufacturing process before full-sc...read more
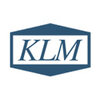
Asked in KLM Laboratories

Q. What are the applications of Quality Management System (QMS) tools in the investigation process?
QMS tools are used in the investigation process to ensure compliance with quality standards, identify root causes of issues, track corrective actions, and improve overall processes.
Ensuring compliance with quality standards and regulations
Identifying root causes of issues and implementing corrective actions
Tracking and documenting investigation processes
Improving overall processes and preventing future issues
Assistant Manager Quality Assurance Jobs
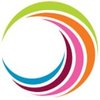
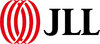
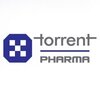
Asked in PMV Nutrient Products

Q. Audit exposure and ability to lead compliance and third party audits
I have extensive experience in leading compliance and third party audits, with a strong background in audit exposure.
Led multiple compliance audits to ensure adherence to industry regulations and standards
Managed third party audits by coordinating with external auditors and internal teams
Implemented corrective actions based on audit findings to improve quality processes
Trained team members on audit requirements and best practices
Maintained audit documentation and records for ...read more
Asked in PMV Nutrient Products

Q. Describe your troubleshooting skills. Provide an example of how you would resolve a shop floor issue.
Effective troubleshooting involves systematic analysis, collaboration, and implementation of solutions to resolve shop floor issues.
Identify the problem: Gather data from operators and review production logs to pinpoint the issue.
Analyze root causes: Use techniques like the 5 Whys or Fishbone Diagram to determine underlying causes.
Collaborate with team: Engage with cross-functional teams to brainstorm potential solutions and gather insights.
Implement solutions: Test the propo...read more
Share interview questions and help millions of jobseekers 🌟

Q. Explain the complete procedure of handling major change control step by step.
Handling major change control involves several steps to ensure proper implementation and minimal impact on operations.
Identify the need for change and document it
Convene a change control board to evaluate the change and its impact
Develop a plan for implementing the change and communicate it to all stakeholders
Implement the change and monitor its impact on operations
Evaluate the success of the change and document the results
Close out the change control process

Asked in AMPLUS SOLAR

Q. What types of sheds are available in the market, and what materials are commonly used for solar module installation?
Various types of sheds are available, and solar module installations commonly use materials like aluminum, steel, and wood.
Types of Sheds: Common types include garden sheds, storage sheds, and utility sheds, each serving different purposes.
Materials for Sheds: Sheds can be made from wood, metal (like steel or aluminum), or plastic, depending on durability and aesthetics.
Solar Module Mounting: Solar panels are typically installed on roofs or ground mounts, using materials like...read more
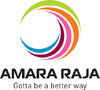
Asked in Amara Raja Energy & Mobility

Q. What raw materials are used in cathodes and anodes?
Raw materials used in cathode include lithium, cobalt, nickel, and aluminum. Anode materials typically consist of graphite, silicon, and lithium.
Cathode raw materials: lithium, cobalt, nickel, aluminum
Anode raw materials: graphite, silicon, lithium
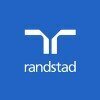
Asked in Randstad

Q. How well do you know about pivot tables and lookup functions in Excel?
I am proficient in pivot tables and lookup functions in Excel.
I have experience creating pivot tables to summarize and analyze data.
I am skilled in using lookup functions such as VLOOKUP and HLOOKUP to search for specific information in a dataset.
I can use pivot tables to create interactive dashboards and reports for data analysis.
I am familiar with advanced features of pivot tables like calculated fields and grouping.
I have used lookup functions to merge data from multiple s...read more
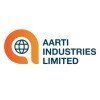
Asked in Aarti Industries

Q. What is the process for APQR (Annual Product Quality Review) preparation?
APQR preparation involves systematic data collection, analysis, and reporting to ensure product quality and compliance.
Collect data from various sources such as batch records, quality control results, and customer complaints.
Analyze trends in product quality, including deviations and non-conformances, to identify areas for improvement.
Review manufacturing processes and changes that occurred during the year to assess their impact on product quality.
Compile a comprehensive repo...read more
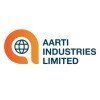
Asked in Aarti Industries

Q. What is the importance of Quality Assurance (QA) documentation?
QA documentation ensures consistency, compliance, and clarity in processes, enhancing product quality and stakeholder communication.
Provides a clear framework for processes, ensuring all team members understand their roles and responsibilities.
Facilitates compliance with industry standards and regulations, such as ISO 9001 or FDA requirements.
Acts as a reference for training new employees, helping them quickly understand quality processes.
Enables effective communication among...read more
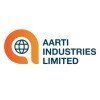
Asked in Aarti Industries

Q. What is the process for handling out-of-specification results?
Handling out-of-specification results involves investigation, documentation, and corrective actions to ensure quality compliance.
Identify the out-of-specification (OOS) result and document it immediately.
Conduct an investigation to determine the root cause, which may include reviewing testing procedures and equipment calibration.
Implement corrective actions based on the investigation findings, such as retraining staff or adjusting processes.
Perform a risk assessment to evalua...read more
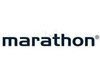
Asked in Marathon Electric India

Q. Questions from FMEA table. Difference is cp and cpk.
Cp and Cpk are statistical process capability indices used in FMEA to measure the ability of a process to produce products within specifications.
Cp measures the potential capability of a process to produce products within specifications, assuming the process is centered at the mean.
Cpk measures the actual capability of a process to produce products within specifications, taking into account the process mean and variation.
Cpk is a more accurate measure of process capability th...read more
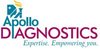
Asked in Apollo Diagnostics

Q. What diagnostics do you use to check for accuracy?
In diagnostics for accuracy check, I perform various tests and analyses to ensure the accuracy of the results.
Conducting quality control tests on diagnostic equipment
Comparing test results with known standards or reference values
Performing statistical analysis to identify any discrepancies
Verifying the accuracy of measurements and calculations
Troubleshooting and resolving any issues or errors
Documenting and reporting findings to the relevant stakeholders
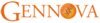
Asked in Gennova Biopharmaceuticals

Q. What is validation, and what is its importance in the pharmaceutical industry?
Validation ensures that pharmaceutical processes consistently produce safe and effective products, crucial for patient safety.
Validation is a documented process that confirms a system or process meets predetermined specifications.
In pharmaceuticals, it includes validating manufacturing processes, analytical methods, and cleaning procedures.
For example, validating a drug manufacturing process ensures that each batch meets quality standards.
It helps in identifying potential iss...read more
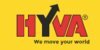
Asked in Hyva

Q. How will you handle customer complaints?
I will listen to the customer, apologize for the inconvenience, investigate the issue, and provide a solution.
Listen attentively to the customer's complaint
Apologize for the inconvenience caused
Investigate the issue to identify the root cause
Provide a solution to the customer
Follow up with the customer to ensure satisfaction
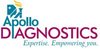
Asked in Apollo Diagnostics

Q. How do you take corrective action if IQC fails?
Corrective action for IQC failure involves identifying root cause, implementing corrective measures, and retesting.
Identify the root cause of the failure through thorough investigation
Implement corrective measures to address the root cause
Retest the failed samples to ensure the corrective actions were effective
Update procedures or processes to prevent similar failures in the future
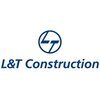
Asked in L&T Construction

Q. Describe the various processes and method statements for construction activities.
Various processes and method statements for construction activities
Developing a project plan outlining the scope, schedule, and budget
Conducting risk assessments to identify potential hazards and develop mitigation strategies
Implementing quality control measures to ensure compliance with specifications and standards
Documenting all construction activities and maintaining accurate records
Regularly inspecting work progress to identify any deviations from the plan
Training and sup...read more
Asked in Putzmeister India

Q. How do you take corrective action on customer complaints?
I investigate root causes of complaints, implement corrective actions, and monitor effectiveness.
Investigate the root cause of the complaint to determine the underlying issue
Implement corrective actions to address the root cause and prevent future occurrences
Monitor the effectiveness of the corrective actions to ensure the issue is resolved
Communicate with the customer to provide updates and ensure satisfaction
Document the entire process for future reference and continuous im...read more
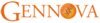
Asked in Gennova Biopharmaceuticals

Q. What is the approach for managing non-compliance when it occurs?
Managing non-compliance involves identifying issues, assessing impact, and implementing corrective actions to prevent recurrence.
Identify the non-compliance issue promptly, e.g., a missed quality check in production.
Assess the impact of the non-compliance on product quality and safety, e.g., potential risks to patients in a medical device.
Implement corrective actions, such as retraining staff or revising procedures, to address the root cause.
Document the non-compliance incide...read more
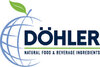
Asked in Doehler

Q. Give an example of a customer complaint and how you solved it.
Customer complained about receiving a damaged product. Resolved by offering a replacement and ensuring better packaging in the future.
Listen to the customer's complaint and empathize with their situation.
Apologize for the inconvenience caused and assure them that their feedback is valuable.
Offer a solution such as a replacement product or a refund.
Take steps to prevent similar issues in the future, such as improving packaging or quality control processes.
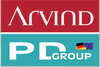
Asked in Arvind Pd Composites

Q. What is PPAP.What are the total documents list under PPAP.
PPAP (Production Part Approval Process) ensures that suppliers meet quality standards before mass production.
1. PPAP is a standardized process used in the automotive and manufacturing industries.
2. It includes documentation to verify that a supplier can produce parts that meet specifications.
3. Key documents include: Design Records, Engineering Change Documents, and Process Flow Diagrams.
4. Other documents are: Control Plans, Measurement System Analysis, and Initial Sample In...read more
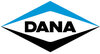
Asked in DANA Graziano India

Q. Process of heat treatment Normalising, Hardening, Annealing etc
Heat treatment processes include normalising, hardening, and annealing.
Normalising involves heating the material above its critical temperature and then cooling it in still air.
Hardening involves heating the material to a high temperature and then rapidly cooling it, usually in water or oil.
Annealing involves heating the material to a specific temperature and then slowly cooling it, often in a controlled environment.
Other heat treatment processes include tempering, case harde...read more

Asked in AMPLUS SOLAR

Q. How can a module be installed over a shed?
Installing a module over a shed involves structural considerations, ensuring stability and compliance with safety regulations.
Structural Assessment: Evaluate the shed's roof to ensure it can support the weight of the module, considering factors like material and design.
Permits and Regulations: Check local building codes and obtain necessary permits before installation to ensure compliance with safety standards.
Mounting Solutions: Use appropriate mounting hardware designed for...read more

Asked in AMPLUS SOLAR

Q. What is the process for calculating wind load?
Calculating wind load involves assessing wind speed, building height, and surface area to determine structural impact.
Determine Basic Wind Speed: Use local building codes to find the basic wind speed for the area, e.g., 90 mph in a hurricane-prone zone.
Calculate Exposure Category: Assess the terrain and surroundings (open, suburban, or urban) to classify the exposure category, affecting wind pressure.
Use the Height of the Structure: Wind load increases with height; apply the ...read more
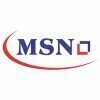
Asked in MSN Laboratories

Q. Water system qualification Phases and How to qualify Pharmaceutical water
Water system qualification involves multiple phases to ensure pharmaceutical water meets quality standards.
Phases include design qualification (DQ), installation qualification (IQ), operational qualification (OQ), and performance qualification (PQ)
DQ ensures the water system is designed correctly for its intended use
IQ verifies that the system is installed correctly according to design specifications
OQ tests the system under normal operating conditions to ensure it functions ...read more
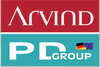
Asked in Arvind Pd Composites

Q. What do you do when a problem occurs on the production line?
I assess the issue, implement corrective actions, and ensure quality standards are maintained to prevent future occurrences.
Identify the problem: Quickly determine the nature of the issue, such as equipment malfunction or quality deviation.
Assess impact: Evaluate how the problem affects production and product quality, prioritizing urgent issues.
Implement corrective actions: Take immediate steps to resolve the issue, such as stopping the line or adjusting parameters.
Communicat...read more
Interview Experiences of Popular Companies
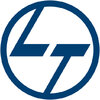
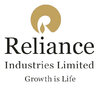
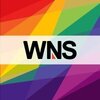
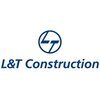
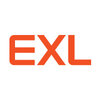
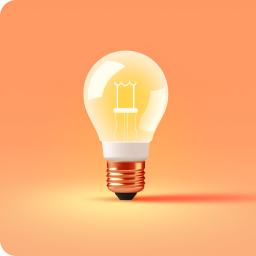
Calculate your in-hand salary
Confused about how your in-hand salary is calculated? Enter your annual salary (CTC) and get your in-hand salary
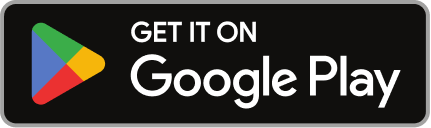
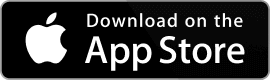
Reviews
Interviews
Salaries
Users
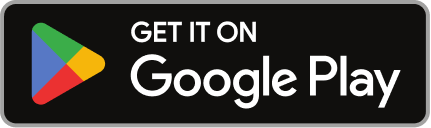
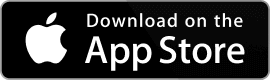