Assistant Manager - QA
20+ Assistant Manager - QA Interview Questions and Answers
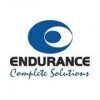
Asked in Endurance Technologies

Q. Which is customer complaint and how you ensure anticipation of defect.
Customer complaint is feedback from customers regarding issues with products or services. Anticipation of defects involves proactive measures to identify and address potential issues before they occur.
Customer complaint is any feedback or concern raised by a customer regarding a product or service.
Anticipation of defects involves implementing quality control measures to identify and address potential issues before they impact customers.
Methods for anticipating defects include...read more
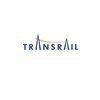
Asked in Transrail Lighting

Q. Do you know the grade of material and fabrication process?
Yes, the grade of material refers to its quality and the fabrication process refers to how it is made.
Grade of material refers to the quality or purity of the material used in manufacturing.
Fabrication process refers to the method used to shape, cut, and assemble materials into a final product.
Examples of grades of material include stainless steel grades like 304 or 316, and fabrication processes include welding, machining, and casting.
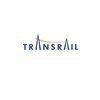
Asked in Transrail Lighting

Q. What is your experience with CAPA in response to customer complaints?
CAPA against customer complaints involves investigating root causes, implementing corrective actions, and preventing recurrence.
Investigate customer complaints thoroughly to identify root causes
Implement corrective actions to address the identified issues
Prevent recurrence of similar complaints by updating processes or procedures
Document all steps taken in the CAPA process for future reference
Regularly review and analyze customer complaints to identify trends or recurring iss...read more
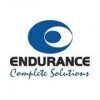
Asked in Endurance Technologies

Q. Which tool do you use for Root Cause Analysis?
The tool commonly used for Root Cause Analysis is the Fishbone Diagram (Ishikawa Diagram).
Fishbone Diagram (Ishikawa Diagram) is a visual tool used to identify the possible causes of a problem.
5 Whys technique is also commonly used for Root Cause Analysis.
Pareto Analysis can be used to prioritize the causes identified in the Fishbone Diagram.
Root Cause Analysis software like TapRooT or Apollo Root Cause Analysis can also be used.
Brainstorming sessions with cross-functional te...read more
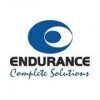
Asked in Endurance Technologies

Q. What are the CTQ parameters and controls?
CTQ parameters are critical to quality parameters that directly impact customer satisfaction. Controls are measures put in place to ensure these parameters are met.
CTQ parameters are key characteristics of a product or service that directly impact customer satisfaction
Controls are measures put in place to ensure CTQ parameters are met consistently
Examples of CTQ parameters include product dimensions, performance metrics, and customer service response times
Examples of controls...read more
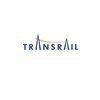
Asked in Transrail Lighting

Q. Do you know root cause analysis?
Root cause analysis is a systematic process used to identify the underlying causes of problems or issues.
Root cause analysis involves identifying the primary cause of a problem rather than just addressing the symptoms.
It helps in preventing the recurrence of issues by addressing the root cause.
Common techniques used in root cause analysis include 5 Whys, Fishbone Diagram, and Fault Tree Analysis.
Example: If a product is consistently failing quality checks, root cause analysis...read more
Assistant Manager - QA Jobs
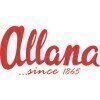

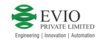
Asked in Wrig Nanosystems

Q. What is the difference between analog and digital signals?
Analog signals are continuous and can take any value within a range, while digital signals are discrete and can only take specific values.
Analog signals have infinite possible values, while digital signals have a finite number of possible values.
Analog signals are more susceptible to noise and interference, while digital signals are more resistant.
Examples of analog signals include sound waves and temperature readings, while examples of digital signals include binary data and...read more
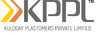
Asked in KPPL (Kuloday Plastomers)

Q. What do you think about working with the company?
I believe working with the company will enhance my skills and contribute to its success through quality assurance excellence.
The company's commitment to quality aligns with my professional values, as seen in my previous role where I improved testing processes by 30%.
I admire the innovative projects the company undertakes, which motivates me to contribute my expertise in QA to ensure their success.
Collaboration with cross-functional teams is essential, and I have successfully ...read more
Share interview questions and help millions of jobseekers 🌟
Asked in Assurgen Pharma

Q. What tools are currently used for investigations?
Some current tools for investigations include forensic software, data analysis tools, and surveillance equipment.
Forensic software such as EnCase and FTK are commonly used for digital investigations
Data analysis tools like Tableau and IBM SPSS help in analyzing large datasets for patterns and anomalies
Surveillance equipment like CCTV cameras and GPS trackers are used for physical investigations
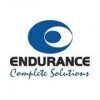
Asked in Endurance Technologies

Q. Which Tooling used and supplier name
We use JIRA for bug tracking and TestRail for test case management. Our main supplier for testing tools is SmartBear.
JIRA for bug tracking
TestRail for test case management
Main supplier: SmartBear
Asked in Assurgen Pharma

Q. Based on concurrent validation batches, can the materials be released to customers?
Concurrent validation allows for timely release of materials, but must meet strict regulatory standards.
Concurrent validation involves testing materials while production is ongoing.
Regulatory guidelines (e.g., FDA) require that concurrent validation is well-documented.
Example: A pharmaceutical company may release a batch of a drug after initial tests show compliance.
Quality assurance teams must ensure that all validation criteria are met before release.
Risks include potential...read more
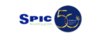

Q. What are weight measuring instruments
Weight measuring instruments are devices used to measure the weight of an object or substance.
Common weight measuring instruments include scales, balances, and load cells.
Scales are used for measuring the weight of objects in various settings such as kitchens, laboratories, and industries.
Balances are used for precise measurements in scientific experiments and research.
Load cells are used in industrial applications to measure the weight of heavy objects or materials.
Weight me...read more
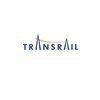
Asked in Transrail Lighting

Q. What about welding process?
Welding process involves joining two or more metal pieces together using heat and/or pressure.
Welding is a common manufacturing process used in various industries such as automotive, construction, and aerospace.
Different types of welding techniques include MIG welding, TIG welding, and arc welding.
Quality assurance in welding involves ensuring proper weld penetration, strength, and appearance.
Non-destructive testing methods like ultrasonic testing and X-ray inspection are use...read more
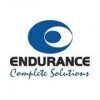
Asked in Endurance Technologies

Q. Why is the anodizing process required?
Anodizing process is required to increase corrosion resistance, improve durability, enhance aesthetic appeal, and provide better adhesion for paint or other coatings.
Increases corrosion resistance by forming a protective oxide layer on the surface of the metal
Improves durability by hardening the surface of the metal
Enhances aesthetic appeal by offering a variety of color options through dyeing
Provides better adhesion for paint or other coatings, resulting in a longer-lasting ...read more
Asked in Assurgen Pharma

Q. How will you qualify vendors?
Qualifying vendors involves assessing their capabilities, quality standards, and compliance with regulations.
Evaluate vendor's quality management system
Assess vendor's track record and reputation
Review vendor's compliance with industry regulations and standards
Conduct on-site audits or inspections if necessary
Consider vendor's pricing and delivery timelines
Asked in Creative Labels

Q. What is an error-proofing system?
Error proofing system is a method of preventing errors from occurring in a process or system.
It involves identifying potential errors and implementing measures to prevent them.
Examples include using checklists, visual aids, and automation.
The goal is to reduce the likelihood of errors and improve quality.
Error proofing is also known as poka-yoke in Japanese.
It can be applied in various industries such as manufacturing, healthcare, and software development.
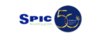

Q. How does a flapper nozzle work?
A flapper nozzle is a type of valve that opens and closes to control the flow of a fluid or gas.
Flapper nozzle consists of a flap or disc that moves up and down to regulate the flow
When the flap is lifted, fluid or gas can pass through the nozzle
When the flap is closed, the flow is stopped
Commonly used in fuel dispensers, fire sprinkler systems, and irrigation systems
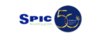

Q. How does an input converter work?
An i/p converter converts input signals into a different format for processing or transmission.
An i/p converter takes an input signal and converts it into a different format, such as analog to digital or vice versa.
It may involve sampling the input signal at regular intervals and quantizing it into discrete values.
Examples include analog-to-digital converters (ADCs) and digital-to-analog converters (DACs).
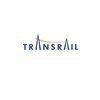
Asked in Transrail Lighting

Q. What is ISO? Please explain.
ISO stands for International Organization for Standardization. It is a global body that develops and publishes international standards.
ISO develops and publishes international standards to ensure quality, safety, and efficiency in products, services, and systems.
ISO standards cover various industries such as technology, healthcare, food safety, and environmental management.
ISO certification demonstrates that a company meets the requirements of specific ISO standards, enhancin...read more
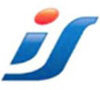
Asked in ILJIN ELECTRONICS

Q. What is ISO 9001?
ISO 9001 is a quality management system standard that outlines requirements for organizations to ensure customer satisfaction.
ISO 9001 is a set of standards developed by the International Organization for Standardization (ISO).
It outlines requirements for a quality management system that an organization must meet to ensure customer satisfaction.
ISO 9001 certification is often required by customers as a condition for doing business.
The standard covers areas such as customer fo...read more
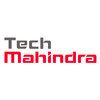
Asked in Tech Mahindra

Q. What are the 7 QC tools?
7QC tool is a set of quality control tools used to identify and solve quality-related problems in a process.
The 7QC tools include: Pareto chart, cause-and-effect diagram, check sheet, control chart, histogram, scatter diagram, and flowchart.
These tools help in identifying the root cause of a problem, analyzing data, and making data-driven decisions.
For example, a Pareto chart can be used to identify the most frequent defects in a process, while a control chart can be used to ...read more
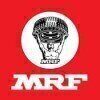
Asked in MRF Tyres

Q. What is a strain gauge?
A strain gauge is a device used to measure the strain or deformation of an object by detecting changes in resistance.
Strain gauges are often used in engineering applications to monitor the structural integrity of buildings, bridges, and machinery.
They work on the principle that the electrical resistance of a wire changes when it is stretched or compressed.
The strain gauge is attached to the object being measured and as the object deforms, the resistance of the gauge changes, ...read more
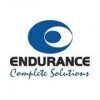
Asked in Endurance Technologies

Q. Which soft skills do you have?
Some of the soft skills I possess include strong communication, problem-solving abilities, leadership skills, and attention to detail.
Strong communication skills - able to effectively convey information and ideas
Problem-solving abilities - adept at identifying issues and finding solutions
Leadership skills - capable of guiding and motivating team members
Attention to detail - meticulous in ensuring accuracy and quality
Asked in Creative Labels

Q. What is 8D CAPA?
8D CAPA is a structured problem-solving approach used to identify, correct, and prevent recurring problems.
8D stands for 8 Disciplines
CAPA stands for Corrective and Preventive Action
It involves a team-based approach to problem-solving
It includes steps such as defining the problem, identifying the root cause, implementing corrective actions, and verifying effectiveness
It is commonly used in quality management systems
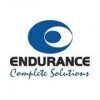
Asked in Endurance Technologies

Q. What is CTQ?
CTQ stands for Critical to Quality. It is a key measurable characteristic of a product or process that is essential for customer satisfaction.
CTQs are identified based on customer requirements and expectations.
They are used to define the quality standards that must be met for a product or process to be considered successful.
Examples of CTQs include product dimensions, performance metrics, and defect rates.
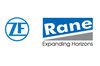
Asked in Zf Rane Automotive

Q. What are the levels of PPAP?
PPAP stands for Production Part Approval Process, which is a standardized method used in the automotive industry to ensure that suppliers can consistently deliver high-quality parts.
PPAP is a set of documentation and approval processes that suppliers must follow to demonstrate their ability to meet customer requirements
It includes various levels or submission levels, ranging from Level 1 to Level 5
Each level has specific requirements and documentation that need to be submitte...read more
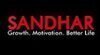
Asked in Sandhar Technologies

Q. Tell me about your problem-solving skills.
Effective problem-solving in QA involves identifying issues, analyzing root causes, and implementing solutions systematically.
Identify the problem clearly: For example, if a product fails a quality test, determine the specific failure criteria.
Analyze root causes: Use techniques like the 5 Whys to dig deeper into why the issue occurred.
Develop a solution: Create a corrective action plan, such as revising testing protocols or enhancing training for staff.
Implement the solution...read more
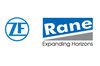
Asked in Zf Rane Automotive

Q. Phase of APQP
APQP stands for Advanced Product Quality Planning and consists of five phases.
Phase 1: Planning and Program Definition - This phase involves defining the project scope, establishing the team, and creating a timeline.
Phase 2: Product Design and Development - In this phase, the product design is developed, including prototypes and testing.
Phase 3: Process Design and Development - The manufacturing process is designed and developed, including creating control plans and conductin...read more
Interview Experiences of Popular Companies
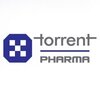
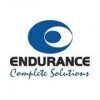
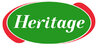
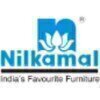
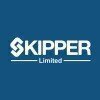
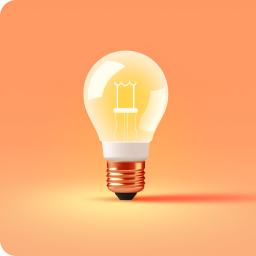
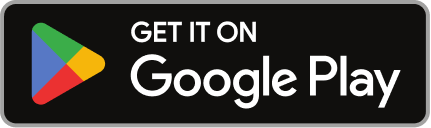
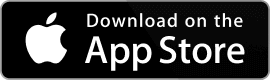
Reviews
Interviews
Salaries
Users
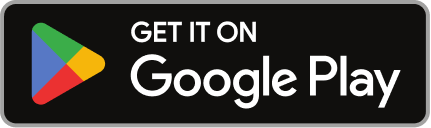
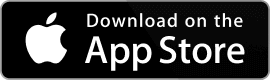