Mechanical Engg. Design
300+ Mechanical Engg. Design Interview Questions and Answers
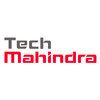
Asked in Tech Mahindra

Q. What are the Drawing softwares you're aware of And How much relevant experience you have in for each software
I am proficient in AutoCAD, SolidWorks, and CATIA with over 3 years of experience in each software.
Proficient in AutoCAD, SolidWorks, and CATIA
Over 3 years of experience in each software
Able to create 2D and 3D models, assemblies, and drawings
Familiar with GD&T and ANSI standards
Experience in designing mechanical components and systems
Ability to work with large assemblies and complex geometries
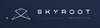
Asked in Skyroot Aerospace

Q. If there are two pipes, one with an 8 mm diameter carrying Helium and another with a 10 mm diameter carrying Nitrogen, which pipe will have a higher mass flow rate, and which will have a higher volume flow rate...
read moreThe pipe with 10mm diameter carrying Nitrogen will have higher mass flow rate due to higher density. The pipe with 8mm diameter carrying Helium will have higher volume flow rate due to lower density.
Nitrogen has a higher density than Helium, so the pipe with 10mm diameter will have higher mass flow rate
Helium has a lower density than Nitrogen, so the pipe with 8mm diameter will have higher volume flow rate
Mechanical Engg. Design Interview Questions and Answers for Freshers
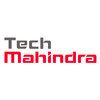
Asked in Tech Mahindra

Q. Why is a flat process used in sheet metal fabrication?
Flat process is preferred in sheet metal fabrication for ease of manufacturing and cost-effectiveness.
Flat process involves cutting and bending sheet metal in a single plane, reducing the need for complex tooling and machinery.
It also allows for easier handling and transportation of the sheet metal.
Flat process is more cost-effective than other processes like deep drawing or hydroforming.
Examples of products made using flat process include metal cabinets, enclosures, and pane...read more
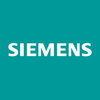
Asked in Siemens

Q. What is the purpose of alloy steel, and what are its different types?
Alloy steel is used for its high strength and durability. It is made by adding other elements to iron.
Alloy steel is made by adding other elements to iron to improve its properties.
It is used for its high strength, durability, and resistance to corrosion.
Some common types of alloy steel include stainless steel, tool steel, and high-strength low-alloy steel.
Stainless steel contains chromium and nickel, making it resistant to rust and corrosion.
Tool steel is used for making too...read more
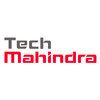
Asked in Tech Mahindra

Q. What thicknesses are commonly used in manufacturing in your industry?
The thickness used to manufacture in the mechanical engineering design industry varies depending on the specific application and materials involved.
The thickness of components can range from very thin, such as sheet metal with thicknesses measured in millimeters, to thick structures like heavy machinery components with thicknesses measured in centimeters or even meters.
The choice of thickness is determined by factors such as the mechanical strength requirements, material prop...read more
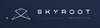
Asked in Skyroot Aerospace

Q. If three pipes with diameters of 4mm, 5mm, and 8mm are flowing water, which pipe can fill a tank faster, assuming the highest flow rate for the lowest diameter?
The pipe with the highest flow rate for the lowest diameter (4mm) will fill the tank fastest.
The pipe with the smallest diameter (4mm) will have the highest flow rate for water flow.
Smaller diameter pipes have higher flow rates due to higher velocity of water flow.
Therefore, the 4mm diameter pipe will fill the tank fastest compared to the 5mm and 8mm diameter pipes.
Mechanical Engg. Design Jobs
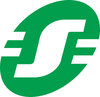
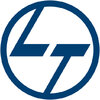
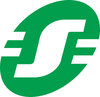
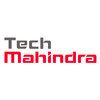
Asked in Tech Mahindra

Q. How do you select flanges, and where are they used?
Flanges are selected based on factors like pressure rating, material compatibility, and application requirements.
Flanges are selected based on the pressure rating required for the specific application.
Material compatibility is crucial in selecting flanges to ensure they can withstand the intended environment.
Application requirements such as temperature, fluid type, and pipe size also influence flange selection.
Common types of flanges include weld neck, slip-on, socket weld, a...read more
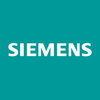
Asked in Siemens

Q. If you are given a technical calculation task on your first day, how will you proceed?
I would first gather all the necessary information and data required for the calculation and then proceed with the calculation process.
Gather all the necessary information and data required for the calculation
Understand the problem statement and requirements
Identify the relevant formulas and equations
Check for any assumptions or constraints
Perform the calculation accurately
Verify the results and ensure they meet the requirements
Share interview questions and help millions of jobseekers 🌟
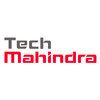
Asked in Tech Mahindra

Q. Draw shear force and Bending Moment Diagram for the Given Drawing (Cantilever Beam)
Draw shear and bending moment diagrams for a cantilever beam.
Calculate reactions at the support
Determine the equation of the shear force diagram
Determine the equation of the bending moment diagram
Plot the diagrams using the equations
Check for accuracy and consistency
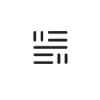
Asked in Univlabs

Q. What is the factor of safety?
Factor of safety is the ratio of the maximum stress a material can withstand to the actual stress it is subjected to.
Factor of safety is used to ensure the safety and reliability of a design.
It is calculated by dividing the ultimate strength of a material by the maximum stress it is expected to experience.
A factor of safety greater than 1 indicates that the design is safe and can withstand the expected loads.
For example, if a bridge is designed to support a maximum load of 10...read more
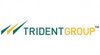
Asked in Trident Group

Q. What type of design software did you use in your previous job?
I have used SolidWorks and AutoCAD for designing in my previous job.
I have experience in creating 3D models, assemblies, and drawings using SolidWorks.
I have also used AutoCAD for 2D drafting and detailing.
I am familiar with creating parametric models and using design tables in SolidWorks.
I have worked on projects involving sheet metal design, weldments, and surface modeling.
I have collaborated with other engineers and stakeholders to ensure designs meet requirements and stan...read more
Asked in Hitech Hydraulics

Q. What is installed between a motor and a cylinder in a hydraulic system?
A hydraulic pump is installed between a motor and a cylinder in a hydraulic system.
A hydraulic pump is used to convert mechanical energy from the motor into hydraulic energy.
The pump pressurizes the hydraulic fluid, which is then used to move the cylinder.
The pump can be driven directly by the motor or through a system of gears or belts.
Examples of hydraulic pumps include gear pumps, vane pumps, and piston pumps.
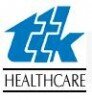
Asked in TTK Healthcare

Q. Which angle of projection is used for drawings in India?
The angle of projection used for drawing in India is 45 degrees.
The angle of projection used in India is the first angle projection system.
This means that the object is placed in the first quadrant and the viewing plane is in front of the object.
The angle of projection used is 45 degrees, which is the same as the standard angle used in ISO standards.
This angle is used for both mechanical and architectural drawings in India.
Asked in Focus Controls

Q. Tell about your experience,and what you have knowledge on hydraulics & pneumatics?
I have experience in designing hydraulic and pneumatic systems for various industrial applications.
Designed hydraulic systems for heavy machinery like cranes and excavators
Developed pneumatic systems for automated assembly lines
Knowledge of fluid mechanics and control systems
Experience in selecting appropriate components like pumps, valves, and actuators
Familiarity with industry standards and safety regulations

Asked in GGS Engineering Services

Q. How many symbols are there in GD&T?
There are 14 symbols in GD&T (Geometric Dimensioning and Tolerancing).
GD&T uses symbols to communicate design requirements and tolerances.
These symbols are used to specify the shape, size, and orientation of features on a part.
Some common symbols in GD&T include concentricity, perpendicularity, flatness, and position.
Each symbol has a specific meaning and is used to ensure proper functionality and interchangeability of parts.
GD&T symbols are standardized and widely used in en...read more
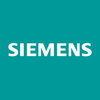
Asked in Siemens

Q. Derive the expression for hoop stress and longitudinal stress in a pressure vessel.
Derive expressions for hoop stress and longitudinal stress in a pressure vessel.
Hoop stress is the circumferential stress in the cylindrical wall of the vessel and is given by σh = pd/2t
Longitudinal stress is the axial stress in the cylindrical wall of the vessel and is given by σl = pd/4t
Where p is the internal pressure, d is the diameter of the vessel, and t is the thickness of the wall
These stresses are important in designing pressure vessels to ensure they can withstand t...read more
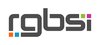
Asked in RGBSI

Q. What are the different types of stresses?
Different types of stresses include tensile, compressive, shear, bending, and torsional stress.
Tensile stress occurs when a material is pulled apart, like stretching a rubber band.
Compressive stress occurs when a material is pushed together, like squeezing a sponge.
Shear stress occurs when a material is twisted or cut, like cutting a piece of paper with scissors.
Bending stress occurs when a material is bent, like bending a piece of wire.
Torsional stress occurs when a material...read more
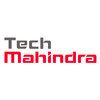
Asked in Tech Mahindra

Q. How do you calculate bending allowances?
Bending allowances are given to compensate for material stretching during bending process.
Bending allowances are added to the flat pattern of a sheet metal part before bending.
The amount of bending allowance depends on the material type, thickness, bend radius, and angle.
Bending allowances are typically specified in a table or chart provided by the manufacturer.
The bending allowance formula is: BA = (π/180) x R x (180 - α) x K
Where R is the bend radius, α is the bend angle, a...read more
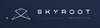
Asked in Skyroot Aerospace

Q. What is the pressure ratio for choking condition?
Pressure ratio for chocking condition is the critical pressure ratio at which the flow of a fluid becomes choked.
The pressure ratio for chocking condition is the ratio of the outlet pressure to the inlet pressure at which the flow becomes choked.
It is a critical parameter in the design of nozzles, valves, and other flow control devices.
For air flowing through a nozzle, the pressure ratio for chocking condition is approximately 0.528.
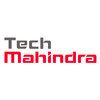
Asked in Tech Mahindra

Q. Explain sheet metal fabrication processes.
Sheet metal fabrication processes involve various techniques to shape and form sheet metal into desired products.
Cutting: Techniques like shearing, laser cutting, and waterjet cutting are used to cut sheet metal into desired shapes.
Bending: Sheet metal is bent using techniques like press brake bending or roll forming to create angles and curves.
Forming: Processes like deep drawing, hydroforming, and stamping are used to shape sheet metal into complex forms.
Joining: Welding, r...read more
Asked in Focus Controls

Q. What is your knowledge of Fits & Tolerance, and where would you apply it?
Yes, I am knowledgeable about Fits & Tolerance and its application in mechanical design.
Fits & Tolerance are used to ensure proper functioning of mechanical parts.
It involves specifying the allowable deviation in dimensions of mating parts.
Tolerance can be applied to various aspects such as size, shape, position, and orientation.
Fits can be classified as clearance, interference, or transition fits.
Examples of application include designing bearings, gears, and shafts.
Proper ap...read more
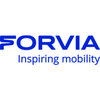
Asked in Forvia

Q. What is the minimum draft angle required for a product with graining or texture, such as car interior plastic parts?
The minimum draft angle for products with graining/texture, like car interior plastic parts, is typically 1-3 degrees.
Draft angle is the angle between the vertical direction and the sidewall of a molded part.
Graining or texture on plastic parts can make it difficult to release the part from the mold.
A minimum draft angle of 1-3 degrees helps ensure easy ejection of the part from the mold.
Insufficient draft angle can result in sticking, deformation, or damage to the part durin...read more
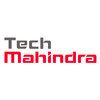
Asked in Tech Mahindra

Q. Why are tolerances used in CAD drawings?
Tolerances are used in CAD drawings to ensure that the manufactured part meets the required specifications.
Tolerances help to control the variation in dimensions and ensure that the parts fit together properly.
They also help to reduce manufacturing costs by allowing for a range of acceptable dimensions rather than requiring every part to be made to exact specifications.
Tolerances can be specified for various dimensions such as length, width, diameter, and angles.
Examples of t...read more
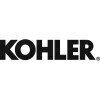
Asked in Kohler

Q. Two shafts have the same cross-section. One is hollow, and the other is solid. If the same load is applied to both, will the stress induced be the same on both shafts?
Hollow and solid shafts with same cross section and load have different stress induced.
The stress induced in the hollow shaft is less than that in the solid shaft.
The stress is directly proportional to the distance from the neutral axis.
The neutral axis is closer to the center of the solid shaft than the hollow shaft.
The hollow shaft has more material away from the neutral axis, reducing stress.
This is why hollow shafts are preferred in many applications, as they are lighter ...read more
Asked in Swift Machines

Q. How proficient are you in Solidworks sheet metal and weldments?
I am highly proficient in SolidWorks, particularly in sheet metal and weldments, with extensive practical experience.
Experienced in creating complex sheet metal parts using the Sheet Metal feature, including flanges and bends.
Proficient in using the Weldments tool to design structural frames and supports, ensuring proper joint configurations.
Utilized the 'Convert to Sheet Metal' feature to streamline the design process for existing solid models.
Implemented design tables for p...read more
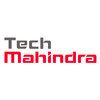
Asked in Tech Mahindra

Q. Possible GD & T Diagram for the rectangular Box
Geometric Dimensioning and Tolerancing (GD&T) diagram for a rectangular box.
Use basic GD&T symbols such as perpendicularity, flatness, and parallelism to specify the dimensions and tolerances of the box.
Include datum features to establish a reference frame for the measurements.
Consider the functional requirements of the box, such as its ability to stack or fit with other components.
Use profile tolerance to control the overall shape of the box.
Consider the manufacturing proces...read more
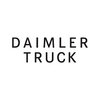
Asked in Daimler Truck

Q. What is the center of gravity? Write the formula to calculate it for an asymmetrical I section.
Centre of gravity is the point where the entire weight of an object can be considered to act upon. Formula for an asymmetrical I section is (A1*d1 + A2*d2)/(A1+A2)
Centre of gravity is important in designing structures and machines to ensure stability and balance
It is the point where the object will balance perfectly in any orientation
For an asymmetrical I section, the formula is (A1*d1 + A2*d2)/(A1+A2) where A1 and A2 are the areas of the two flanges and d1 and d2 are the dis...read more
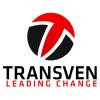
Asked in Transven

Q. Head load, it's parameters, the ways to calculate plumbing load, water demand, fire load calculation, system design of plumbing firefighting and HVAC systems
Explanation of head load, plumbing load, water demand, fire load calculation, and system design of plumbing firefighting and HVAC systems.
Head load is the pressure exerted by water on the plumbing system and is calculated using the formula P = ρgh.
Plumbing load is the total load on the plumbing system and is calculated by adding the head load and friction loss.
Water demand is the amount of water required by a building and is calculated based on the number of occupants and the...read more
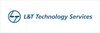
Asked in L&T Technology Services

Q. In CREO, how do you copy a feature in a part and parts in an assembly?
In CREO, features can be copied in parts and parts can be copied in assemblies using the Copy/Paste feature.
To copy a feature in a part, simply select the feature and use the Copy/Paste function.
To copy parts in an assembly, select the part(s) you want to copy and use the Copy/Paste function.
You can also use the Mirror feature to create a mirrored copy of a feature or part.
Copying features and parts can help in reusing designs and saving time in the design process.
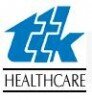
Asked in TTK Healthcare

Q. Draw the Front view, Top view, Side View, Cross-section view along with isometric of the given Product or Model
Draw front, top, side, cross-section views and isometric of given product/model.
Create a 2D drawing of the product/model from different angles
Include dimensions and annotations
Use appropriate scales for each view
Create an isometric view to show the product/model in 3D
Ensure accuracy and clarity in the drawings
Interview Experiences of Popular Companies
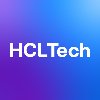
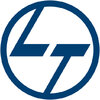
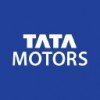
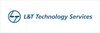
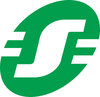
Top Interview Questions for Mechanical Engg. Design Related Skills
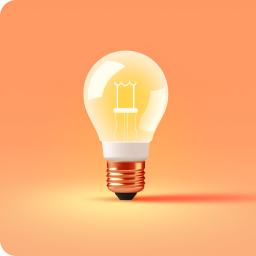
Calculate your in-hand salary
Confused about how your in-hand salary is calculated? Enter your annual salary (CTC) and get your in-hand salary
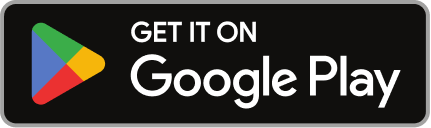
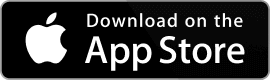
Reviews
Interviews
Salaries
Users
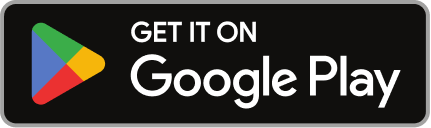
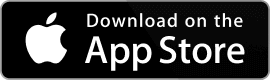