Assistant Manager Safety
40+ Assistant Manager Safety Interview Questions and Answers
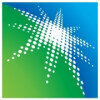
Asked in Saudi Aramco

Q. 1. What is HSE plan 2. What is HSE Policy. 3 .What is Safety program
HSE plan is a detailed strategy outlining how health, safety, and environmental risks will be managed. HSE Policy is a company's commitment to health, safety, and environmental protection. Safety program is a set of procedures and initiatives to ensure workplace safety.
HSE plan is a comprehensive document that outlines how an organization will identify, assess, and control health, safety, and environmental risks.
HSE Policy is a formal statement by an organization outlining it...read more
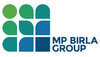
Asked in Birla Cement

Q. What you know about AI in safety field and hot to help it.
AI in safety field involves using artificial intelligence technology to improve safety measures and prevent accidents.
AI can be used to analyze data from sensors and cameras to identify potential safety hazards in real-time.
AI can help in predicting and preventing workplace accidents by analyzing patterns and trends in safety data.
AI can automate safety inspections and audits, saving time and reducing human error.
AI can be used to develop virtual reality training simulations ...read more
Assistant Manager Safety Interview Questions and Answers for Freshers
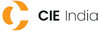
Asked in CIE Automotive

Q. How do you handle individuals who knowingly commit unsafe acts?
I address unsafe acts by educating, enforcing safety protocols, and providing incentives for safe behavior.
Educate employees on safety protocols and the consequences of unsafe acts
Enforce safety regulations consistently and fairly
Provide incentives for safe behavior such as rewards or recognition
Implement a reporting system for employees to raise concerns about unsafe acts
Lead by example by following safety protocols yourself
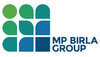
Asked in Birla Cement

Q. What is the procedure for a Safety Committee and Safety audit?
Safety Committee oversees safety practices and procedures, while Safety Audit evaluates the effectiveness of safety measures.
Safety Committee is responsible for developing safety policies, conducting safety training, and addressing safety concerns.
Members of the Safety Committee may include representatives from different departments to ensure comprehensive safety oversight.
Safety Audit involves evaluating the implementation of safety policies, identifying potential hazards, a...read more
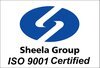
Asked in Sheela Foam

Q. What are main requirements in fire safety What is fire monitor?
Main requirements in fire safety include fire prevention, detection, evacuation, and suppression. A fire monitor is a device used to detect and alert individuals of a fire.
Fire prevention involves implementing measures to reduce the risk of fires, such as proper storage of flammable materials and regular maintenance of electrical systems.
Fire detection systems, such as smoke detectors and fire alarms, are essential for early warning of a fire.
Evacuation plans should be in pla...read more
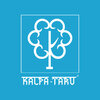
Asked in Kalpataru Limited

Q. What are the two main causes of Accidents or Incidents on site?
The two main causes of accidents on site are human error and unsafe conditions, both of which can lead to serious incidents.
Human Error: Mistakes made by workers, such as not following safety protocols. Example: A worker forgetting to wear a helmet.
Unsafe Conditions: Hazards present in the work environment, like slippery floors or faulty equipment. Example: A wet floor leading to slips.
Assistant Manager Safety Jobs
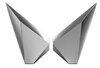
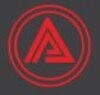

Asked in Whiteland Corporation

Q. What is Safety management and how it's running as well process.?
Safety management involves systematic processes to identify, assess, and mitigate risks in the workplace.
Identify hazards: Regular inspections to find potential risks, e.g., checking for slippery floors.
Risk assessment: Evaluate the likelihood and impact of identified hazards, such as assessing the risk of chemical spills.
Implement controls: Develop safety protocols, like using PPE (Personal Protective Equipment) for hazardous tasks.
Training: Conduct regular safety training s...read more
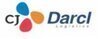
Asked in CJ Darcl Logistics Limited

Q. What is the relationship between ISO standards and CSMS in relation to occupational health and safety?
ISO standards provide frameworks for safety management, while CSMS focuses on continuous improvement in occupational health and safety.
ISO 45001: This standard outlines requirements for an occupational health and safety management system (OHSMS), promoting safe and healthy workplaces.
CSMS (Continuous Safety Management System): This approach emphasizes ongoing evaluation and improvement of safety practices, aligning with ISO standards.
Integration: Organizations can integrate I...read more
Share interview questions and help millions of jobseekers 🌟
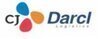
Asked in CJ Darcl Logistics Limited

Q. What recent initiative have you taken for safety improvement at the site?
I implemented a safety training program that significantly reduced incidents and improved overall safety awareness among employees.
Safety Training Program: Developed a comprehensive training program that included hands-on workshops and online modules to educate employees on safety protocols.
Regular Safety Audits: Initiated monthly safety audits to identify potential hazards and ensure compliance with safety regulations, leading to a 30% reduction in near-miss incidents.
Employ...read more
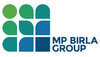
Asked in Birla Cement

Q. How do you implement the hierarchy control method?
Hierarchy control method involves implementing controls in a specific order of effectiveness.
Identify hazards and risks in the workplace
Implement elimination or substitution controls first
If elimination or substitution is not feasible, implement engineering controls
If engineering controls are not sufficient, implement administrative controls
Personal protective equipment (PPE) should be used as a last resort
Regularly review and update the hierarchy of controls
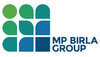
Asked in Birla Cement

Q. How do you liaise with local workers and vendors?
To liaise with local workers and vendors, establish clear communication channels, build relationships, and ensure mutual understanding and cooperation.
Establish regular communication channels with local workers and vendors
Build relationships based on trust and mutual respect
Ensure clear understanding of expectations and responsibilities
Provide necessary training and support to local workers and vendors
Address any issues or conflicts promptly and professionally
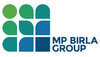
Asked in Birla Cement

Q. How to minimise incident and how to increase SOT.
To minimize incidents, focus on proactive safety measures and training. To increase SOT, implement efficient work processes and prioritize safety.
Implement regular safety training for all employees
Conduct regular safety inspections and audits to identify potential hazards
Encourage reporting of near misses to prevent future incidents
Implement a safety incentive program to promote safe behaviors
Invest in safety equipment and technology to reduce risks
Establish clear safety prot...read more
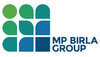
Asked in Birla Cement

Q. What do you know about Contractor Safety Management?
Contractor Safety Management involves ensuring that contractors working on site follow safety protocols to prevent accidents and injuries.
Developing contractor safety policies and procedures
Conducting pre-qualification assessments of contractors
Providing safety training to contractors
Implementing safety audits and inspections for contractors
Ensuring compliance with safety regulations and standards
Establishing clear communication channels for reporting safety concerns
Monitorin...read more
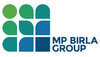
Asked in Birla Cement

Q. What do you know about safety legal compliances?
Safety legal compliances refer to laws and regulations that organizations must follow to ensure the safety of their employees and the public.
Safety legal compliances include OSHA regulations, local building codes, and industry-specific guidelines.
Employers must provide a safe work environment, conduct regular safety training, and maintain proper records.
Examples of safety legal compliances include having fire extinguishers in the workplace, conducting regular safety inspectio...read more
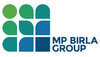
Asked in Birla Cement

Q. What is process hazard and how do you identify it?
Process hazard is a potential source of harm or danger within a process industry setting.
Process hazard is any condition that poses a risk to the safety or health of employees, the public, or the environment.
Common process hazards include chemical reactions, fires, explosions, and toxic releases.
Process hazards can be identified through process hazard analysis (PHA) techniques such as HAZOP, FMEA, and What-If analysis.
Regular inspections, audits, and incident investigations c...read more
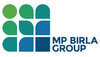
Asked in Birla Cement

Q. Which tools do you use for incident investigation?
Common tools for incident investigation include root cause analysis, fishbone diagrams, 5 Whys, and incident reporting forms.
Root cause analysis helps identify the underlying causes of incidents.
Fishbone diagrams visually display the potential causes of an incident.
5 Whys technique involves asking 'why' multiple times to uncover the root cause.
Incident reporting forms document details of the incident for analysis and prevention.
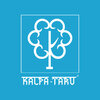
Asked in Kalpataru Limited

Q. How would you tackle the safety challenges on site?
I would implement proactive measures, training, and continuous monitoring to address safety challenges effectively on site.
Conduct regular safety audits to identify potential hazards and mitigate risks.
Implement a comprehensive training program for all employees, emphasizing safety protocols and emergency procedures.
Encourage a safety-first culture by promoting open communication and reporting of unsafe conditions without fear of reprisal.
Utilize personal protective equipment...read more
Asked in Whiteland Corporation

Q. How do you control Contractor HSE at an unsafe workplace?
Implementing strict HSE protocols and continuous monitoring ensures contractor safety in hazardous workplaces.
Conduct thorough risk assessments before work begins to identify potential hazards.
Establish clear HSE guidelines and ensure all contractors are trained on these protocols.
Implement regular safety audits and inspections to monitor compliance and identify unsafe practices.
Encourage open communication about safety concerns, allowing workers to report hazards without fea...read more
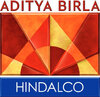
Asked in Hindalco Industries

Q. What are the legal requirements in a manufacturing establishment?
Legal requirements in a manufacturing establishment include compliance with occupational health and safety regulations, environmental laws, and labor standards.
Compliance with Occupational Safety and Health Administration (OSHA) regulations
Adherence to environmental protection laws and regulations
Ensuring workplace safety measures are in place, such as proper training, safety equipment, and emergency procedures
Compliance with labor standards, including fair wages, working hou...read more
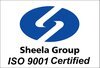
Asked in Sheela Foam

Q. What pumps are used in a pump house?
Various types of pumps are used in pump houses depending on the specific requirements and applications.
Centrifugal pumps are commonly used for general water pumping applications
Submersible pumps are used for pumping water from wells or underground sources
Booster pumps are used to increase water pressure in a system
Sump pumps are used to remove water that has accumulated in a sump pit
Diaphragm pumps are used for pumping fluids with high solid content or viscosity
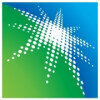
Asked in Saudi Aramco

Q. How do you investigate accidents in the workplace?
Accident investigation at workplace involves identifying root causes, gathering evidence, interviewing witnesses, and implementing corrective actions.
Identify the accident scene and secure it to preserve evidence
Interview witnesses to gather information about the incident
Review relevant documents such as safety procedures and training records
Analyze the sequence of events leading up to the accident
Identify root causes such as human error, equipment failure, or unsafe work pra...read more
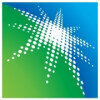
Asked in Saudi Aramco

Q. What is Safety commitment & Safety program
Safety commitment is the dedication of an organization to prioritize and uphold safety standards, while a safety program is a structured plan to implement safety measures.
Safety commitment involves top management support and involvement in safety initiatives
Safety program includes policies, procedures, training, and audits to ensure a safe work environment
Examples of safety programs include regular safety meetings, hazard identification programs, and emergency response plans
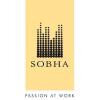
Asked in Sobha

Q. What are the check points in a Batching Plant?
Check points in Batching Plant include material storage, weighing systems, mixing systems, and delivery systems.
Material storage area should be organized and free from debris to prevent contamination.
Weighing systems should be calibrated regularly to ensure accurate measurements.
Mixing systems should be checked for proper functioning and cleanliness to avoid cross-contamination.
Delivery systems should be inspected for leaks or blockages to ensure smooth transportation of mate...read more
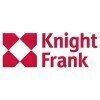
Asked in Knight Frank

Q. How do you calculate risk assessment?
Risk assessment is calculated by identifying hazards, evaluating the likelihood and severity of potential harm, and determining risk levels.
Identify hazards present in the workplace or environment
Evaluate the likelihood of those hazards causing harm
Assess the potential severity of harm that could result from the hazards
Determine the risk level by combining likelihood and severity assessments
Use risk assessment tools such as risk matrices or risk assessment codes
Regularly revi...read more
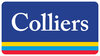
Asked in Colliers India

Q. What are some common unsafe acts observed on a site?
Common unsafe acts on a site include improper use of equipment, lack of PPE, and ignoring safety protocols.
Improper use of ladders: Workers may stand on the top rung, risking falls.
Failure to wear personal protective equipment (PPE): Not using helmets or gloves can lead to injuries.
Ignoring safety signs: Bypassing warning signs can result in accidents.
Operating machinery without training: Untrained personnel may misuse equipment, causing harm.
Poor housekeeping: Cluttered work...read more
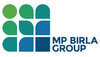
Asked in Birla Cement

Q. What is a critical lifting plan?
A critical lifting plan is a detailed document outlining the procedures and precautions to be taken when lifting heavy objects to ensure safety.
Identifies the specific equipment needed for the lift
Outlines the steps to be taken before, during, and after the lift
Includes information on weight limits, proper lifting techniques, and potential hazards
Specifies the roles and responsibilities of individuals involved in the lift
Should be reviewed and approved by a qualified safety p...read more
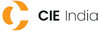
Asked in CIE Automotive

Q. How do you conduct a HIRA study?
HIRA study is conducted by identifying hazards, assessing risks, and implementing control measures.
Identify all potential hazards in the workplace or process.
Assess the risks associated with each hazard by considering the likelihood and severity of potential harm.
Prioritize the risks based on the level of risk and potential impact.
Implement control measures to eliminate or reduce the risks identified.
Regularly review and update the HIRA study to ensure effectiveness.
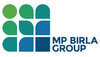
Asked in Birla Cement

Q. What are the differences between HIRA, JSA, and SOP?
HIRA identifies hazards, JSA breaks down tasks, SOP provides step-by-step instructions.
HIRA (Hazard Identification and Risk Assessment) is a systematic process to identify hazards and assess risks in the workplace.
JSA (Job Safety Analysis) breaks down a job into its individual tasks to identify potential hazards and develop safety measures.
SOP (Standard Operating Procedure) provides step-by-step instructions on how to perform a specific task safely and efficiently.
HIRA focuse...read more
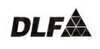
Asked in DLF

Q. What is HIRA CORA Inspection report Auditing
HIRA, CORA, Inspection report, and Auditing are all important aspects of safety management in a workplace.
HIRA stands for Hazard Identification and Risk Assessment, which involves identifying potential hazards in the workplace and assessing the risks associated with them.
CORA stands for Consequence of Risk Analysis, which involves analyzing the potential consequences of identified risks.
Inspection reports are documents that detail the findings of safety inspections conducted ...read more
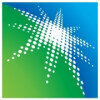
Asked in Saudi Aramco

Q. What is BOCW Act & Safety plan
The BOCW Act stands for Building and Other Construction Workers Act, which aims to regulate the safety, health, and welfare of construction workers. A safety plan is a document outlining safety measures and procedures to prevent accidents and injuries on a construction site.
BOCW Act is a legislation in India that focuses on the welfare of construction workers
It mandates safety measures, health provisions, and welfare amenities for construction workers
Safety plan is a document...read more
Interview Experiences of Popular Companies
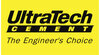
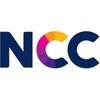
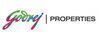
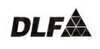
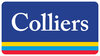
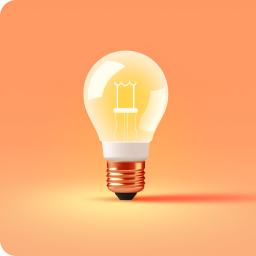
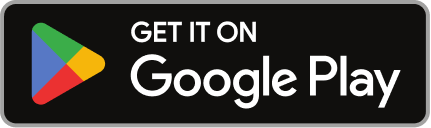
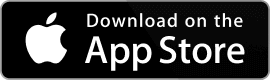
Reviews
Interviews
Salaries
Users
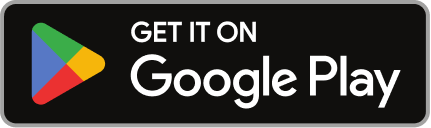
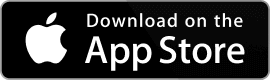