Assistant Manager Quality
60+ Assistant Manager Quality Interview Questions and Answers
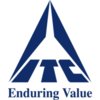
Asked in ITC Limited Foods Division

Q. How do you handle a consumer who has undergone an allergic reaction after consuming your product?
I would apologize and investigate the issue thoroughly to prevent future occurrences.
Express empathy and concern for the consumer's well-being
Ask for details about the allergic reaction and any medical attention received
Collect information about the product and its ingredients
Investigate the manufacturing process and quality control measures
Take appropriate corrective actions to prevent future occurrences
Follow up with the consumer to ensure their satisfaction and address any...read more
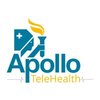
Asked in Apollo Telehealth Services

Q. On what tools do you train people? or How do you train people?
We train people on various tools such as Lean Six Sigma, Root Cause Analysis, Fishbone Diagram, and Pareto Chart.
We use Lean Six Sigma to improve processes and reduce waste.
Root Cause Analysis helps identify the underlying cause of a problem.
Fishbone Diagram is used to identify the potential causes of a problem.
Pareto Chart helps prioritize the most significant issues to address.
We also provide on-the-job training and mentorship to ensure practical application of these tools.
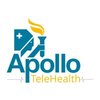
Asked in Apollo Telehealth Services

Q. What are the main Quality Parameters?
The main Quality Parameters are characteristics that define the quality of a product or service.
Performance
Reliability
Durability
Serviceability
Aesthetics
Safety
Perceived Quality
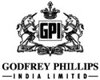
Asked in Godfrey Phillips India

Q. Are you willing to explore new opportunities in food quality?
Yes, I am willing to search for new opportunities in the quality of food.
I am passionate about food quality and always looking for ways to improve it.
I have experience in implementing quality control measures in food production.
I am familiar with food safety regulations and standards.
I enjoy staying updated with the latest trends and advancements in the food industry.
I am open to exploring new opportunities that allow me to contribute to the quality of food.
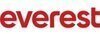
Asked in Everest Industries

Q. Tolerance & Acceptance Criteria for some physical parameters, welding Criteria, etc.
Tolerance and acceptance criteria for physical parameters and welding criteria are essential for ensuring quality standards are met.
Tolerance and acceptance criteria are set based on industry standards and requirements
Physical parameters such as dimensions, surface finish, and material properties must fall within specified tolerances
Welding criteria include parameters like weld size, penetration depth, and visual inspection standards
Criteria are established to ensure product ...read more
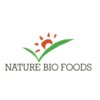
Asked in Nature Bio Foods

Q. Tell me about your knowledge of Genetic Engineering, which you mentioned in your CV.
Genetic engineering is the manipulation of an organism's genes using biotechnology.
It involves altering the DNA sequence of an organism to produce desired traits.
Examples include creating crops that are resistant to pests or diseases, or producing insulin for diabetes treatment.
It has ethical concerns regarding the potential for creating genetically modified organisms that could harm the environment or human health.
It has also led to advancements in medical research and treat...read more
Assistant Manager Quality Jobs
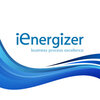
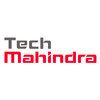
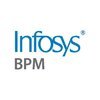
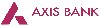
Asked in Axis Bank

Q. Quality parameters and scenarios wise related to sale improvement .
Quality parameters and scenarios related to sales improvement involve identifying customer needs, improving product quality, and enhancing customer experience.
Identify customer needs and preferences through surveys and feedback
Improve product quality through rigorous testing and quality control measures
Enhance customer experience through personalized service and timely resolution of complaints
Implement effective sales strategies and promotions to attract and retain customers
M...read more
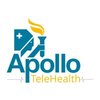
Asked in Apollo Telehealth Services

Q. What do you mean by KPI and KRA?
KPI stands for Key Performance Indicator and KRA stands for Key Result Area.
KPIs are measurable values that indicate how effectively an individual or organization is achieving their objectives.
KPIs are used to track progress, identify areas for improvement, and measure success.
KPIs are specific to each role or department and can vary depending on the goals and objectives.
KRA refers to the main areas of responsibility or outcomes that an individual or team is expected to achie...read more
Share interview questions and help millions of jobseekers 🌟
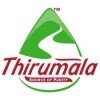
Asked in Tirumala Milk Products

Q. What is short term goal and long term goal?
Short term goals are achievable within a few months to a year, while long term goals take several years to accomplish.
Short term goals help in achieving long term goals
Short term goals are specific and measurable
Long term goals are broader and require more planning
Examples of short term goals include learning a new skill or completing a project
Examples of long term goals include career advancement or starting a business
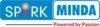
Asked in Spark Minda

Q. How do you implement core tools in an organization with limited resources?
Implementing core tools in a limited resources organization requires strategic planning and prioritization.
Prioritize core tools based on the organization's specific needs and goals.
Train existing staff on how to effectively use core tools to maximize resources.
Utilize free or low-cost resources such as online training modules or open-source software.
Collaborate with other organizations or industry partners to share resources and best practices.
Regularly assess and adjust the...read more
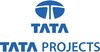
Asked in Tata Projects

Q. What methods can be used to check the quality of concrete?
Various methods exist to assess concrete quality, ensuring structural integrity and durability.
Visual Inspection: Check for surface defects, cracks, or discoloration.
Slump Test: Measures workability and consistency of fresh concrete.
Compression Test: Evaluates strength by testing concrete samples under pressure.
Air Content Test: Determines the amount of air in the mix, affecting durability.
Core Sampling: Extracts samples from hardened concrete for laboratory testing.
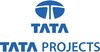
Asked in Tata Projects

Q. What methods can be used to check the quality of reinforcement?
Various methods ensure the quality of reinforcement in construction, including visual inspections, testing, and compliance checks.
Visual Inspection: Check for rust, deformation, or damage on the surface of reinforcement bars.
Dimensional Checks: Measure the diameter and length of reinforcement bars to ensure they meet specifications.
Material Testing: Conduct tensile strength tests to verify the mechanical properties of the reinforcement.
Documentation Review: Ensure that all re...read more
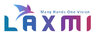
Asked in LCC Projects

Q. How can a project maintain good progress while ensuring safety and quality?
Balancing safety and quality ensures project efficiency and minimizes risks, leading to successful outcomes.
Implement regular safety training sessions for all team members to ensure awareness and compliance.
Use quality management systems (QMS) to monitor processes and identify areas for improvement, such as ISO 9001.
Conduct risk assessments at each project phase to identify potential hazards and develop mitigation strategies.
Encourage open communication among team members to ...read more
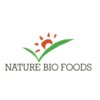
Asked in Nature Bio Foods

Q. Do you know how Non-GMO testing is carried out?
Non-GMO testing involves DNA analysis to detect the presence of genetically modified organisms in food products.
Samples are collected from the food product
DNA is extracted from the samples
PCR (Polymerase Chain Reaction) is used to amplify the DNA
The amplified DNA is then analyzed to detect the presence of GMOs
The results are compared to a database of known GMOs to determine if the product is non-GMO

Asked in Patton International

Q. What was the tonnage of products dispatched at your previous company?
I dispatched an average of 500 tonnage products per month in my previous company.
Dispatched an average of 500 tonnage products per month
Managed logistics for timely delivery
Ensured accurate documentation for each dispatch
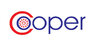
Asked in Cooper Pharma

Q. How would you manage the quality control department with a suitable work team?
Effective management of a quality control department involves teamwork, clear communication, and continuous improvement strategies.
Establish Clear Objectives: Define quality standards and goals for the team, such as reducing defect rates by 20% within a year.
Foster Team Collaboration: Encourage open communication and regular meetings to discuss challenges and share best practices, enhancing team cohesion.
Implement Training Programs: Provide ongoing training for team members o...read more
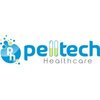
Asked in Pell Tech Healthcare Private Limited

Q. HPLC analysis of any product procedure What ALCOA plus
HPLC analysis is a procedure used to separate, identify, and quantify components in a sample.
HPLC stands for High-Performance Liquid Chromatography.
It is commonly used in pharmaceutical, chemical, and food industries.
The procedure involves injecting a sample into a column filled with a stationary phase and a mobile phase.
The components in the sample interact differently with the stationary phase, leading to separation.
The separated components are then detected and quantified ...read more
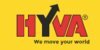
Asked in Hyva

Q. How will you handle customer complaints?
I will listen to the customer, apologize for the inconvenience caused and take necessary actions to resolve the issue.
Listen to the customer's complaint patiently
Apologize for the inconvenience caused
Ask questions to understand the issue better
Take necessary actions to resolve the issue
Follow up with the customer to ensure satisfaction
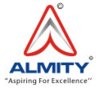
Asked in Almighty Auto Ancillary

Q. What is PPM and how do you control it?
PPM stands for Parts Per Million and is a measure of the number of defective parts in a million parts produced.
PPM is a key performance indicator used to measure the quality of products in manufacturing.
It is calculated by dividing the number of defective parts by the total number of parts produced and multiplying by one million.
Controlling PPM involves implementing quality control measures, conducting regular inspections, and addressing root causes of defects.
Examples of con...read more
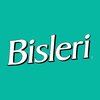
Asked in Bisleri

Q. What are the processes involved in a water treatment plant?
Water treatment plants purify water through various processes to ensure it is safe for consumption and environmental discharge.
Coagulation: Chemicals like alum are added to clump particles together.
Sedimentation: Heavy particles settle at the bottom of the tank.
Filtration: Water passes through filters to remove remaining impurities.
Disinfection: Chlorine or UV light is used to kill pathogens.
pH Adjustment: Chemicals are added to balance the water's acidity.
Fluoridation: Fluor...read more
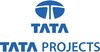
Asked in Tata Projects

Q. What is the procedure for checking footing reinforcement?
The procedure for checking footing reinforcement ensures structural integrity and compliance with design specifications.
Review the structural drawings to understand the reinforcement requirements.
Check the quantity and type of rebar against the specifications.
Verify the placement of rebar in accordance with the design, ensuring proper cover and spacing.
Use a caliper or measuring tape to confirm the diameter of the rebar.
Inspect for any damage or corrosion on the rebar before ...read more
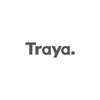
Asked in Traya Health

Q. Why is call quality important in customer experience?
Call quality is crucial for ensuring customer satisfaction, loyalty, and effective communication in service interactions.
Enhances customer satisfaction: High call quality leads to clearer communication, reducing misunderstandings.
Builds trust and loyalty: Consistent quality in calls fosters a positive relationship with customers, encouraging repeat business.
Increases efficiency: Clear calls reduce the time spent resolving issues, allowing for quicker service.
Reflects brand im...read more
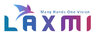
Asked in LCC Projects

Q. Why is safety prioritized over quality during project progression?
Safety is paramount in projects to protect individuals and ensure a solid foundation for quality outcomes.
Safety prevents accidents that can halt project progress, e.g., a construction site incident can lead to project delays.
Prioritizing safety fosters a culture of responsibility, encouraging team members to adhere to quality standards.
In industries like manufacturing, unsafe practices can lead to defective products, impacting overall quality.
Regulatory compliance often mand...read more
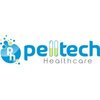
Asked in Pell Tech Healthcare Private Limited

Q. What is the audit trail for HPLC analysis for routine analysis?
Audit trail for HPLC analysis is a record of all activities and changes made during the analysis process.
Audit trail should include information on who performed the analysis, when it was performed, and any changes made to the system or method.
It should also include information on the calibration and maintenance of the HPLC system.
Examples of changes that should be recorded include changes to the sample preparation, changes to the mobile phase, and changes to the column.
The au...read more
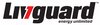
Asked in Livguard

Q. What challenges did you face during spot welding installation?
Challenges faced during spot welding installation include equipment maintenance, operator training, and quality control.
Ensuring proper maintenance of spot welding equipment to prevent breakdowns
Providing thorough training to operators to ensure they are proficient in spot welding techniques
Implementing quality control measures to monitor the accuracy and consistency of spot welds
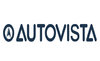
Asked in Excell Autovista

Q. How do you control the number of dissatisfied customers?
To control dissatisfied customers, it is important to identify the root cause of their dissatisfaction and take appropriate corrective actions.
Listen to the customer's complaints and concerns with empathy
Investigate the issue thoroughly to identify the root cause
Take corrective actions to address the root cause and prevent recurrence
Follow up with the customer to ensure their satisfaction has been restored
Implement a system for tracking and analyzing customer complaints to id...read more
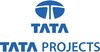
Asked in Tata Projects

Q. What codes are followed for construction?
Construction codes ensure safety, quality, and compliance in building projects, guiding materials and methods used.
International Building Code (IBC) - sets minimum safety standards for buildings.
National Fire Protection Association (NFPA) codes - focus on fire safety in construction.
American Concrete Institute (ACI) standards - guidelines for concrete design and construction.
Occupational Safety and Health Administration (OSHA) regulations - ensure worker safety on constructio...read more
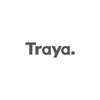
Asked in Traya Health

Q. What do you know about quality audit or analysis?
Quality audit involves systematic examination of processes to ensure compliance with standards and improve overall quality.
Quality audits assess adherence to established standards, such as ISO 9001.
They identify areas for improvement, enhancing efficiency and effectiveness.
Audits can be internal or external; internal audits help prepare for external evaluations.
For example, a manufacturing company may conduct a quality audit to ensure product specifications are met.
Auditors u...read more
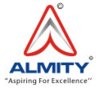
Asked in Almighty Auto Ancillary

Q. How many mandatory clauses are in IATF?
There are 14 mandatory clauses in IATF.
IATF 16949:2016 has 14 mandatory clauses that organizations must comply with to achieve certification.
These clauses cover areas such as quality management system requirements, leadership commitment, planning, support, operation, performance evaluation, and improvement.
Examples of mandatory clauses include clause 4.3 on determining the scope of the quality management system and clause 8.5.1 on control of production and service provision.
Asked in PBM Insulations

Q. What is the process of statistical control?
Statistical control is a method used to monitor and maintain the quality of a process by analyzing data and making adjustments as needed.
Statistical control involves collecting data on a process over time
The data is analyzed using statistical tools to determine if the process is in control or not
If the process is out of control, adjustments are made to bring it back into control
Examples of statistical control tools include control charts, histograms, and process capability an...read more
Interview Experiences of Popular Companies
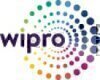
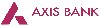
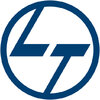
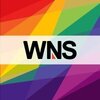
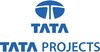
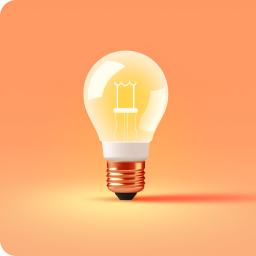
Calculate your in-hand salary
Confused about how your in-hand salary is calculated? Enter your annual salary (CTC) and get your in-hand salary
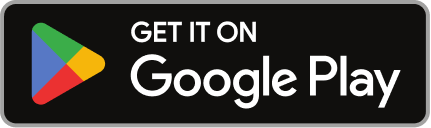
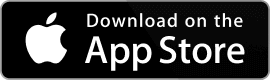
Reviews
Interviews
Salaries
Users
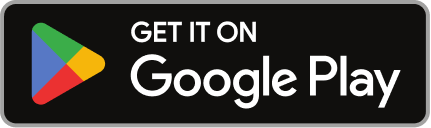
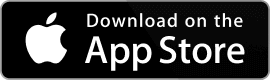