Assistant Manager Maintenance
90+ Assistant Manager Maintenance Interview Questions and Answers
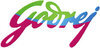
Asked in Godrej Industries

Q. 1. Cost saving initiative in utilities like boiler, air compressor, Cooling Tower etc 2. Types of flow, Reynolds number 3. Selection of heat exchanger as per process, diffrence between shell and tube and Plate...
read moreAnswering questions related to cost-saving initiatives in utilities and selection of heat exchangers.
For cost-saving initiatives, regular maintenance and monitoring of equipment can help identify areas for improvement.
Reynolds number is used to determine the type of flow in a fluid system.
Selection of heat exchangers depends on the process requirements and factors like heat transfer rate, pressure drop, and cost.
Shell and tube heat exchangers are suitable for high-pressure ap...read more
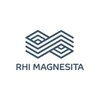
Asked in RHI Magnesita

Q. Can you explain how to read a hydraulic circuit and describe its various parts along with their functions?
A hydraulic circuit consists of various components like pumps, valves, cylinders, and hoses that work together to control the flow of hydraulic fluid.
Hydraulic pump: generates the flow of hydraulic fluid
Valves: control the direction and pressure of the fluid
Cylinders: convert fluid power into mechanical power
Hoses: transport the fluid between components
Reservoir: stores the hydraulic fluid
Filters: remove contaminants from the fluid
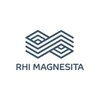
Asked in RHI Magnesita

Q. What are MTTR (Mean Time to Repair) and MTBF (Mean Time Between Failures)?
MTTR is the average time taken to repair a failed system, while MTBF is the average time between failures.
MTTR measures how quickly a system can be restored after a failure
MTBF measures the average time a system operates before experiencing a failure
MTTR = Total downtime / Number of failures
MTBF = Total uptime / Number of failures
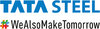
Asked in Tata Steel

Q. What is the difference between a servo valve and a proportional valve?
A servo valve is used for precise control of flow rate, while a proportional valve is used for controlling the flow rate proportionally to the input signal.
Servo valves are typically used in applications where precise control of flow rate is required, such as in aerospace or industrial automation.
Proportional valves are used to control the flow rate proportionally to the input signal, making them suitable for applications like hydraulic systems in construction equipment.
Servo...read more
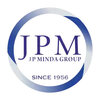
Asked in JPM Group

Q. 1) How to you resolve moulding related concern ? 2) What is MTTR & MTBF ? 3) how to you manage critical spare Parts ? 4) can you read the fixture drawing ?
Answering questions related to maintenance management
To resolve moulding related concerns, I would first identify the root cause and then take appropriate measures such as adjusting temperature and humidity levels, improving ventilation, and using mould inhibitors.
MTTR stands for Mean Time To Repair, which is the average time taken to repair a failed equipment. MTBF stands for Mean Time Between Failures, which is the average time between two consecutive failures of a piece of...read more
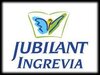
Asked in Jubilant Ingrevia

Q. What is cavitation, can it be possible in vertical pipes at home?
Cavitation is the formation of vapor bubbles in a liquid due to low pressure. It can occur in vertical pipes at home.
Cavitation is caused by low pressure in a liquid, which leads to the formation of vapor bubbles that collapse and cause damage to the pipe.
Vertical pipes at home can experience cavitation if there is a sudden change in pressure, such as when a valve is closed quickly.
Cavitation can cause erosion, noise, and vibration in pipes, which can lead to leaks and other ...read more
Assistant Manager Maintenance Jobs
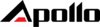

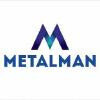
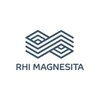
Asked in RHI Magnesita

Q. What is the difference between a flow control valve and a relief valve?
Flow control valve regulates the flow rate of a fluid, while relief valve protects equipment from overpressure by releasing excess fluid.
Flow control valve is used to regulate the flow rate of a fluid in a system.
Relief valve is designed to protect equipment from overpressure by releasing excess fluid to prevent damage.
Flow control valve is typically used to control the speed of hydraulic cylinders or motors.
Relief valve is commonly found in systems where pressure buildup cou...read more
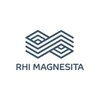
Asked in RHI Magnesita

Q. What is the procedure for opening a CNC machine ball screw assembly?
To open a CNC machine ball screw assembly, follow these steps:
Start by removing the protective covers from the ball screw assembly
Use the appropriate tools to loosen and remove the fasteners securing the ball screw assembly
Carefully lift the ball screw assembly out of the machine, taking care not to damage the components
Inspect the ball screw assembly for any signs of wear or damage
Clean the ball screw assembly and surrounding area before reassembly
Follow the manufacturer's g...read more
Share interview questions and help millions of jobseekers 🌟
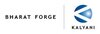
Asked in Bharat Forge

Q. Diffrerene between AC and DC drive, Induction motor and servo motor ,profibus and Ethernet.
AC drive is used for controlling the speed of AC motors, while DC drive is used for controlling the speed of DC motors.
AC drive is based on the principle of changing the frequency of the input voltage to control the speed of the motor.
DC drive is based on the principle of changing the voltage applied to the motor to control its speed.
AC drives are commonly used in industries for applications like pumps, fans, and conveyors.
DC drives are commonly used in applications like elec...read more
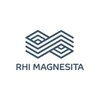
Asked in RHI Magnesita

Q. How should preventive maintenance be planned on a daily basis?
Preventive maintenance should be planned based on equipment criticality, historical data, manufacturer recommendations, and available resources.
Identify critical equipment that needs regular maintenance to prevent breakdowns.
Refer to historical data to determine common issues and plan preventive measures accordingly.
Follow manufacturer recommendations for maintenance schedules and procedures.
Allocate resources such as manpower, tools, and spare parts for daily maintenance tas...read more
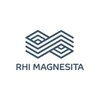
Asked in RHI Magnesita

Q. What is the step-by-step process for opening a profil valve?
The step-by-step process for opening a profil valve involves several key actions.
Ensure the valve is in the closed position before starting.
Locate the valve handle or actuator.
Turn the valve handle or actuator counterclockwise to open the valve.
Monitor the pressure or flow rate to ensure proper operation.
Close the valve by turning the handle or actuator clockwise when finished.
Perform any necessary maintenance or inspections after use.
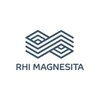
Asked in RHI Magnesita

Q. What is the working principle of a hydraulic press?
Hydraulic press works on the principle of Pascal's law, which states that a change in pressure applied to an enclosed fluid is transmitted undiminished to all portions of the fluid and to the walls of its container.
Hydraulic press uses a hydraulic cylinder to generate a compressive force.
When a force is applied to the small piston, it creates pressure in the enclosed fluid.
This pressure is transmitted through the fluid to the larger piston, resulting in a larger force being e...read more
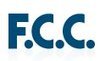
Asked in FCC Clutch

Q. Plant maintenance activities, Why why analysis of breakdowns, Energy saving projects
Plant maintenance activities include Why-Why analysis of breakdowns and energy saving projects.
Plant maintenance activities are crucial for ensuring smooth operations and preventing breakdowns.
Why-Why analysis is a problem-solving technique used to identify the root cause of breakdowns and prevent their recurrence.
Energy saving projects involve identifying opportunities to reduce energy consumption and implementing measures to achieve those savings.
Examples of energy saving p...read more
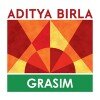
Asked in Grasim Industries

Q. How do you get adjusted with Tamil as a language barrier and Location.
I have experience working in diverse locations and have learned basic Tamil to communicate effectively.
I have previous experience working in diverse locations, which has helped me adapt quickly to new environments.
I have taken the initiative to learn basic Tamil to overcome the language barrier and communicate effectively with the local team.
I have found that immersing myself in the local culture and being open to learning new languages has helped me build strong relationship...read more
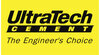
Asked in UltraTech Cement

Q. How many major shutdowns have you handled?
I have handled three major shutdowns in my career.
Managed a major shutdown at my previous company involving over 100 machines and equipment
Coordinated with various departments to ensure smooth execution of shutdown activities
Implemented preventive maintenance measures to reduce downtime during shutdowns
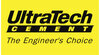
Asked in UltraTech Cement

Q. Pls tell about your section SPC, SHC, MTBF, MTTR, Availability and Cost in terms of budget.
SPC, SHC, MTBF, MTTR, Availability, and Cost are key performance indicators used to measure maintenance efficiency and effectiveness.
SPC (Scheduled Plant Capacity) measures the maximum output a plant can achieve under normal conditions.
SHC (Scheduled Hours Capacity) measures the total hours a plant is scheduled to operate.
MTBF (Mean Time Between Failures) measures the average time between equipment failures.
MTTR (Mean Time To Repair) measures the average time it takes to repa...read more
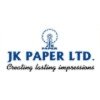
Asked in JK Paper

Q. Let's discuss salary expectations. What is your desired in-hand salary?
Discussing salary expectations is crucial; focus on in-hand salary after deductions and benefits.
Research industry standards for Assistant Manager Maintenance roles to set a baseline.
Consider your current salary and any expected increases based on your experience.
Factor in deductions such as taxes, insurance, and retirement contributions to determine in-hand salary.
Discuss potential bonuses or performance incentives that could affect total compensation.
Be prepared to negotiat...read more
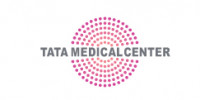
Asked in TATA MEDICAL CENTER

Q. What is downtime?
Downtime refers to the period of time when a machine or system is not operational or available for use.
Downtime can be caused by various factors such as equipment failure, maintenance, repairs, or upgrades.
It can result in lost productivity, revenue, and increased costs.
For example, if a manufacturing plant experiences downtime due to a machine breakdown, it may result in delayed production and missed deadlines.
To minimize downtime, preventive maintenance and regular inspecti...read more
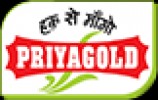
Asked in Surya Food & Agro

Q. How do you plan to manage overall maintenance operations?
I will implement structured processes, prioritize tasks, and foster team collaboration to ensure efficient maintenance operations.
Conduct regular assessments of maintenance needs to identify priority areas, such as equipment that frequently breaks down.
Implement a preventive maintenance schedule to reduce downtime, for example, servicing HVAC systems quarterly.
Utilize maintenance management software to track work orders and inventory, ensuring timely responses to maintenance ...read more
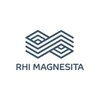
Asked in RHI Magnesita

Q. What is a servo valve, and how does it work?
A servo valve is a type of valve used in hydraulic systems to control the flow of fluid by varying the size of the flow passage.
Servo valves are used in applications where precise control of fluid flow is required, such as in aircraft control systems.
They work by using an electrical signal to move a spool inside the valve, which in turn adjusts the size of the flow passage.
The movement of the spool is proportional to the input signal, allowing for precise control of the fluid...read more
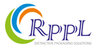
Asked in Rajshree Polypack

Q. How to maintain utility. How to manage manpower.Maintanance plan.
To maintain utility and manage manpower effectively, a maintenance plan should be developed and implemented.
Develop a comprehensive maintenance plan outlining schedules for regular inspections, repairs, and replacements.
Utilize computerized maintenance management systems (CMMS) to track equipment performance and maintenance history.
Implement preventive maintenance strategies to reduce downtime and extend equipment lifespan.
Train and empower maintenance staff to perform tasks ...read more

Asked in JSW Steel Coated Products

Q. What is the difference between a pressure relief valve and a flow control valve?
Pressure relief valve releases excess pressure to prevent damage, while flow control valve regulates the flow rate of a fluid.
Pressure relief valve opens to release excess pressure in a system
Flow control valve regulates the flow rate of a fluid in a system
Pressure relief valve is typically set to open at a specific pressure threshold
Flow control valve can be adjusted to control the flow rate within a desired range
Examples: Safety relief valve in a boiler system, flow control...read more
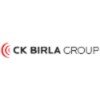
Asked in CK Birla Group

Q. How can an Engineering department improve patient experience?
The Engineering department can increase patient experience by ensuring efficient maintenance of medical equipment and facilities.
Regular maintenance and timely repairs of medical equipment to minimize downtime and ensure accurate diagnosis and treatment.
Ensuring a comfortable and safe environment for patients by maintaining the cleanliness, functionality, and aesthetics of facilities.
Implementing technology advancements to improve patient care, such as automated systems for a...read more
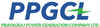
Asked in Prayagraj Power Generation

Q. What is a Hydraulic Power Pack?
A hydraulic power pack is a self-contained unit that generates hydraulic power to operate machinery or equipment.
Consists of a hydraulic pump, motor, reservoir, and control valves
Used in various industries such as construction, manufacturing, and transportation
Can power hydraulic cylinders, motors, and other hydraulic components
Can be customized to meet specific requirements of the application
Examples include power packs for hydraulic presses, lifts, and cranes
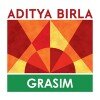
Asked in Grasim Industries

Q. What is your latest achievement in maintenance?
Implemented a preventive maintenance program that reduced equipment downtime by 20%.
Developed and implemented a preventive maintenance program
Reduced equipment downtime by 20%
Improved overall equipment reliability and efficiency
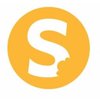
Asked in Sapphire Foods India

Q. How to handle operational change and how to identify priorities
Handling operational change involves assessing impact, communicating effectively, and prioritizing tasks based on urgency and importance.
Assess the impact of the operational change on maintenance processes and resources
Communicate the change to the maintenance team clearly and provide necessary training or support
Identify priorities by evaluating the urgency and importance of tasks, considering factors like safety, cost, and impact on production
Create a plan to address the hi...read more

Asked in JSW Steel Coated Products

Q. Does a vane pump provide flow or pressure?
Vane pumps provide flow, not pressure.
Vane pumps are designed to provide a consistent flow of fluid.
The pressure generated by a vane pump is a result of the resistance to flow in the system.
Vane pumps are commonly used in hydraulic systems to provide a steady flow of fluid to operate various components.
Unlike positive displacement pumps, vane pumps do not generate pressure directly.
The flow rate of a vane pump can be adjusted by changing the speed of the pump or the size of t...read more
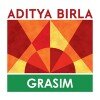
Asked in Grasim Industries

Q. What is the profile of a vane in a churn/mixer?
Vane in churn/mixer is a rotating blade that helps in mixing and churning ingredients efficiently.
Vane is typically made of stainless steel or other durable materials.
It is designed to create turbulence and promote thorough mixing of ingredients.
The shape and size of the vane can vary depending on the specific application.
Vanes are commonly used in industrial mixers, blenders, and churns.
Proper maintenance of vanes is essential to ensure optimal performance of the churn/mixer...read more
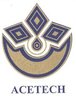
Asked in The Acetech Machinery Components

Q. What motivates you to work in the maintenance field?
My motivation in maintenance field is to ensure smooth functioning of equipment and machinery, and to minimize downtime.
I enjoy problem-solving and finding solutions to technical issues.
I take pride in maintaining high standards of safety and quality.
I am motivated by the challenge of optimizing maintenance processes and reducing costs.
I believe that effective maintenance is essential for the success of any organization.
For example, in my previous role as Maintenance Supervis...read more
Asked in Ralson Shine Carbon

Q. What is the definition of labor?
Labour refers to the physical or mental effort exerted by individuals in order to produce goods or services.
Labour is one of the factors of production, along with land, capital, and entrepreneurship.
It can include both physical work, such as construction or manufacturing, and mental work, such as designing or managing.
Labour is compensated through wages, salaries, or other forms of payment.
The efficiency and productivity of labour can impact the overall success of a business ...read more
Interview Experiences of Popular Companies
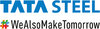
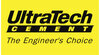
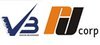
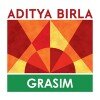
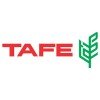
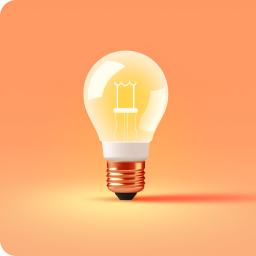
Calculate your in-hand salary
Confused about how your in-hand salary is calculated? Enter your annual salary (CTC) and get your in-hand salary
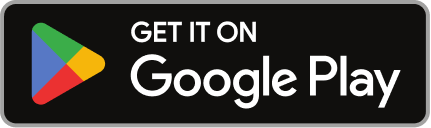
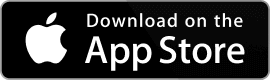
Reviews
Interviews
Salaries
Users
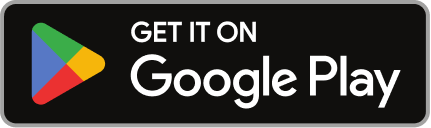
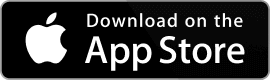